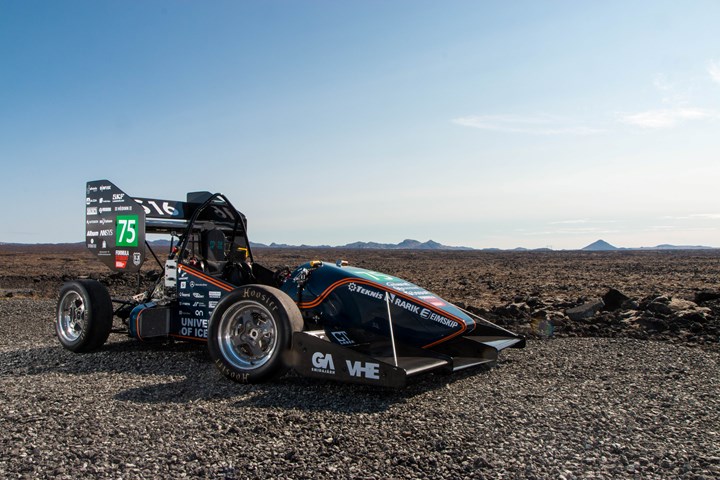
Student members of the University of Iceland’s Formula Student Team, Team Spark, worked with sponsor company Össur to develop a better airfoil/wing that is one seamless piece requiring only one mold and no post-processing. Photo Credit, all images: Technology Transfer Office Iceland
Airfoils, also called wings, are a staple aerodynamic component on racecars, including those developed for university engineering and racing competitions like Formula Student (in Europe) and Formula SAE (in the U.S.). These components, often made from composite materials, are designed to control airflow around the back of the vehicle, with the goal of enabling the highest speeds possible.
Typically, the manufacturing process includes the design and build of two molds, hand layup and cure of the airfoil in two pieces and then adhesive bonding to join the parts together into one component. However, former University of Iceland (Reykjavik) Formula Student team members Sólrún Traustadóttir and Andri Orrason recognized a number of issues using this traditional method. For a sponsor-funded student team, the development of two separate molds for one part could be prohibitively expensive. In addition, the adhesive used to bond the trailing and leading edges of the two airfoil pieces added weight to a part that is meant by design to be lightweight and aerodynamic, and was weaker at the joint. “These things caused us to look for alternative solutions and we ended up with the Spark design,” Traustadóttir and Orrason say.
In 2016, Traustadóttir and Orrason led the development of a new method for producing a one-piece airfoil — a method that the team still uses today. For its method, the University of Iceland’s Formula Student team — named Team Spark — drew inspiration from and worked with one of its sponsors, Össur (Reykjavik, Iceland), a company that makes carbon fiber-reinforced plastic (CFRP) medical prosthetics.
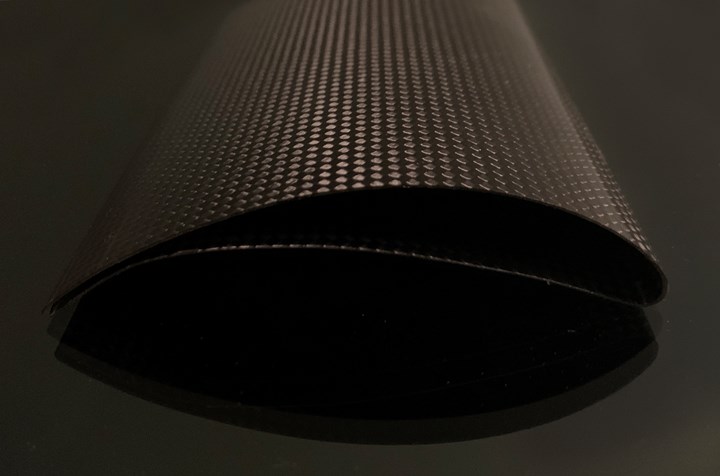
The student researchers patented their process in 2019 and aim to extend “the Spark method” to production of parts for other markets or applications as well.
A typical process would first involve designing and building two negative/female molds for fabricating the two airfoil halves. In the new process, one positive/male mold is built in the shape of the entire airfoil part. The mold is then covered by an adhesive layer, followed by hand layup of carbon fiber prepreg. Additional material layers such as Teflon or silicone can also be used. The entire set-up is then vacuum bagged and cured via autoclave. Once cured and demolded, no further post-processing or assembly steps are needed.The process saves time both by the use of only one mold and the elimination of bonding/post-processing steps.
The resulting one-piece, seamless airfoil/wing and its manufacturing method are said to have caught the attention of other Formula Student teams as well as Formula 1. Traustadóttir and Orrason note that this method can be adjusted to a variety of materials and processes, as well — including less expensive alternatives to prepreg and autoclave cure.
The technology, patented in the U.S. in 2019, is said to have achieved technology readiness level (TRL) 7. Through the Technology Transfer Office Iceland (Reykjavik) Traustadóttir and Orrason are open to licensing opportunities with commercial partners. The Spark team hopes to translate this technology into commercial applications in a variety of end markets, seeing potential for industries such as wind, drones, space, aerospace, automotive and more.
For more information and licensing opportunities, please contact susan@ttoiceland.is at Technology Transfer Office Iceland.
Related Content
Infinite Composites: Type V tanks for space, hydrogen, automotive and more
After a decade of proving its linerless, weight-saving composite tanks with NASA and more than 30 aerospace companies, this CryoSphere pioneer is scaling for growth in commercial space and sustainable transportation on Earth.
Read MoreMaterials & Processes: Fabrication methods
There are numerous methods for fabricating composite components. Selection of a method for a particular part, therefore, will depend on the materials, the part design and end-use or application. Here's a guide to selection.
Read MorePrice, performance, protection: EV battery enclosures, Part 1
Composite technologies are growing in use as suppliers continue efforts to meet more demanding requirements for EV battery enclosures.
Read MoreNew polymer expands composites options in demanding environments
Aromatic thermosetting copolyester offers unique properties, availability in multiple form factors.
Read MoreRead Next
3D printing, composite materials enable motorsports design flexibility
A collegiate Formula SAE racing team used Windform carbon fiber-filled composite materials and laser sintering technology to streamline part design.
Read MoreRacing to build tomorrow’s automotive composites workforce
Recent graduates share experiences gained from collegiate automotive design, engineering and motorsport competition Formula SAE.
Read MoreItalian student design team uses composites to improve automotive performance
Politecnico di Milano’s Formula SAE team worked with Exel Composites to transition to lighter, better-performing composite vehicle components.
Read More