BMW Group invests in Bcomp for high-performance natural fiber components
Collaborative partnership in motorsport moves to the next level for the use of renewable raw materials for future vehicle model components, and joint R&D materials work for production vehicles is underway.
Share
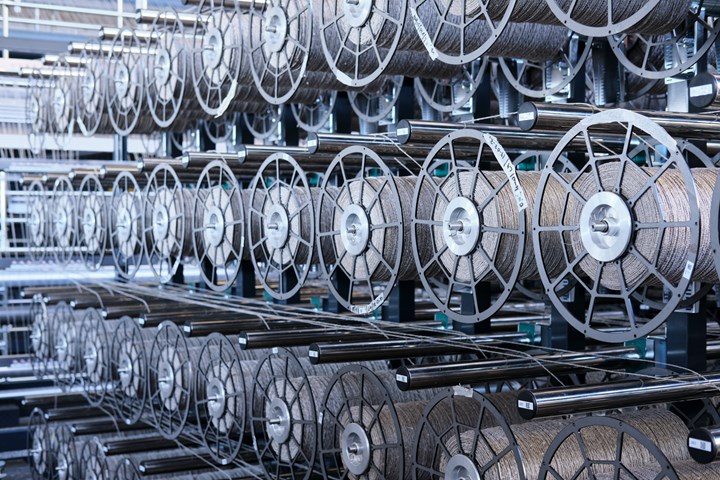
Bcomp natural fiber production. Photo Credit, all images: Bcomp
The BMW Group (Munich, Germany) is expanding its involvement in the field of sustainable, resource-efficient manufacturing of vehicle components made from natural fiber-reinforced materials. BMW i Ventures (Mountain View, Calif., U.S.), the premium carmaker’s venture capital firm, is now investing in Swiss clean tech company Bcomp Ltd. (Fribourg, Switzerland), a leading manufacturer of high-performance components made from natural fibers. At the same time, the two companies are also strengthening their partnership on the motorsport side, with Bcomp now an official BMW M Motorsport partner with the new BMW M4 GT4 racing car. Plus, BMW Group Research and Bcomp are also setting up a development alliance with the aim of using a higher proportion of renewable raw materials for components in future vehicle models.
Bcomp’s fiber reinforcement solutions were reportedly first deployed by BMW M Motorsport in Formula E in 2019. The flax cooling shaft on the BMW iFE.20 made it what BMW says was the first racing car with parts constructed from renewable textile fibers. Meanwhile, the Bcomp-developed powerRibs and ampliTex reinforcement solutions made from natural composite materials have been used in DTM touring cars from BMW M Motorsport to substitute selected carbon fiber-reinforced plastic (CFRP) components. Such advances underline BMW M Motorsport’s vital role as a technology lab for the BMW Group, which is now set to continue with the collaboration on the BMW M4 GT4. Taking the findings and experience gained on the track as a basis, BMW Group adds that these material technologies will also find their way into BMW M models and BMW M Performance Parts.
“Product sustainability is increasing in importance in the world of motorsport too,” says Franciscus van Meel, chairman of the board of management at BMW M GmbH. “We are delighted to have Bcomp on board as an official BMW M Motorsport partner for the BMW M4 GT4 project.”
Inspired by leaf veins, the powerRibs reinforcement technology developed by Bcomp reportedly maximizes stiffness with minimal weight by creating a 3D structure on one side of a thin-walled shell element. This enables a decrease in the amount of base material used, thereby reducing weight, costs and consumables in production. The ampliTex reinforcements add a visible layer of flax fibers as a carbon-neutral replacement for the conventional covering material. Combining the two materials makes it possible to cut the amount of plastic used for interior paneling by up to 70%, BMW Group claims, while simultaneously reducing CO2 emissions by as much as 75%. The result is more sustainable vehicle components, whose ductile fracture properties have the additional benefit of increasing safety. The natural fiber composites also lend themselves to use with classical motor sport accessories, such as those in the BMW M Performance Parts range.

BMW M motorsport vehicle.
The development partnership between BMW Group Research and Bcomp is also working on the use of novel sustainable material solutions for future production models. BMW Group is seeking to lower its vehicles’ lifecycle carbon emissions by more than 40% by 2030 compared to 2019 levels.
At the current time, natural fibers are particularly well-suited to use in visible and paneling parts in vehicle interiors. “In order to reduce carbon emissions across its entire fleet, the BMW Group isn’t just focusing on the use phase — it is also paying attention to energy-saving processes during manufacture,” explains Florian Preuß, senior vice president, development complete vehicle, at the BMW Group. “Innovative material selection and composition are an important step here as we move towards climate neutrality.”
Related Content
The state of recycled carbon fiber
As the need for carbon fiber rises, can recycling fill the gap?
Read MoreComposite rebar for future infrastructure
GFRP eliminates risk of corrosion and increases durability fourfold for reinforced concrete that meets future demands as traffic, urbanization and extreme weather increase.
Read MoreCarbon fiber in pressure vessels for hydrogen
The emerging H2 economy drives tank development for aircraft, ships and gas transport.
Read MoreMaterials & Processes: Composites fibers and resins
Compared to legacy materials like steel, aluminum, iron and titanium, composites are still coming of age, and only just now are being better understood by design and manufacturing engineers. However, composites’ physical properties — combined with unbeatable light weight — make them undeniably attractive.
Read MoreRead Next
Bcomp developments continue to drive natural fiber toward scalability in motorsports
The Swiss sustainable lightweight manufacturer announces new developments for vehicle interiors, sustainability analyses results for ampliTEX and powerRibs reinforcements and recent technology recognition.
Read MoreBercella, Formula Seven target motorsport innovation with natural fiber composite developments
AmpliTex flax fiber used to develop Formula SAE single-seater racing seat for better resistance, vibration absorption and reduced environmental impact.
Read MoreBMW rolls out multi-material Carbon Cage with 2022 iX vehicle line
For its new battery-electric iX sports activity vehicle, BMW combines CFRP strategies from previous i3, i8 and 7-Series designs and adds CFRTP for a lightweight, rigid frame.
Read More