Share
Read Next
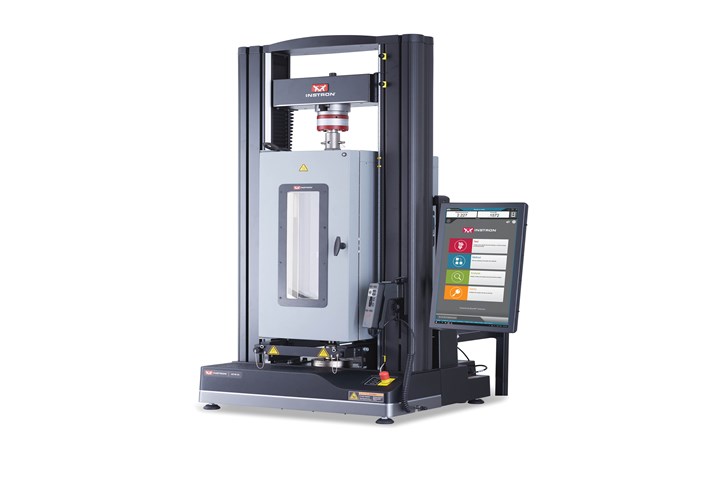
Figure 1. Instron 6800 Series Universal Testing System with an environmental chamber, used for testing composites at non-ambient temperatures. Photo Credit: Instron
In Part 1 and Part 2 of this series on composites testing, I covered the types of standardized mechanical tests currently available for composite materials and recent developments in strain measurement, respectively. In the final installment of this series, I will discuss the recommended system requirements that will help you test these materials accurately and efficiently.
Testing systems for composites
Several factors need to be considered when configuring a system for testing composites (Fig. 1). First and foremost, tests need to be conducted in compliance with the appropriate standards and audit requirements. This means the system must be able to accommodate the fixtures needed for each test and meet requirements regarding specimen alignment and other factors. This includes providing the correct test environment, so that any required fixtures can operate reliably within it. Moreover, the process for changing the test setup should be simple in order to maintain high levels of productivity, and the system should be easy to use and minimize the skill level required by the operator, which reduces the likelihood of errors and optimizes productivity.
Because composite specimens can experience explosive failures, testing machines should have a high axial stiffness and be very robust to reduce and resist wear and tear from these repeatedly large shock forces. They should also have a high lateral stiffness and an accurate guidance system to maintain alignment, particularly when performing compression tests.
It is desirable to have a force measurement system (load cell and electronic signal processing) with a wide measurement range, as this eliminates the need to change the load cell when switching from high force tests (e.g., tension/compression) to low force tests (e.g., ILSS). It is also important that machine electronics are protected against the ingress of carbon fiber dust and debris, which is conductive and can damage electronics.
Test environment
The most common testing environment for composite materials is at elevated temperatures, generally in the range of 80-250°C. Specimens may be conditioned in specific environments prior to testing, typically to temperature, humidity and exposure to liquids such as water, fuel and hydraulic fluids. The time taken for polymer composite materials to achieve equilibrium with a conditioning medium is usually on the order of days or weeks, and the majority of short-duration static property testing is conducted in a chamber providing a temperature-only environment. Chambers designed for testing at low and high temperatures are generally equipped with electrical heating elements and cryogenic injection systems for cooling (usually liquid nitrogen or carbon dioxide). Mechanical cooling (refrigeration) systems are also available. Although mechanical systems generally do not provide the high cooling rates and minimum temperatures that can be achieved with cryogenic injection cooling, they are suited to providing constant temperatures for long-term tests.
Grips and fixtures
Suitable grips for composites testing include manual and hydraulic wedge grips. For demanding aerospace testing, hydraulic wedge grips are generally preferred because of their accurate alignment and repeatability. However, well-designed mechanical wedge grips can also provide acceptable alignment. For safety and reliability, hydraulic grip solutions for non-ambient testing will usually place the hydraulic components outside of the temperature chamber. In most cases, it is best to leave the grips permanently fixed in place on the test machine and use “piggyback” adapters as necessary to mount any test fixtures such as compression platens or bend fixtures onto the grips. This approach reduces the need for handling heavy items and maintains grip alignment.
Alignment
Accurate alignment is very important when testing composite materials due to the anisotropic and often brittle nature of composite specimens. Adjustable alignment fixtures are available to ensure that testing systems meet the alignment criteria required by specific audit programs used by the aerospace industry, such as Nadcap AC7122/1. To be effective, alignment fixtures need to allow adjustment of both concentricity and angularity while the machine load string is under load. The accepted method of confirming alignment is to use a strain gauged “alignment cell or specimen” to check the alignment under load. The alignment cell should have dimensions that are as close as possible to the specimens being tested. Typically, the alignment cell will be fitted with two or three groups of four strain gauges. It is possible to record the outputs of the gauges and manually calculate the bending caused by misalignment, but this is a complex and tedious process. Fortunately, software is available that provides a display of both the bending and the concentricity and angularity errors in real time (Fig. 2).
Test machine software
Software is responsible for controlling the testing machine, collecting data from the test and analyzing the data to produce test results. The latest generation of testing software is capable of all of this and much more. For instance, touchscreen technology can simplify and enhance the way in which an operator interacts with the system. Data and reports can also be exported to networks and databases, and software can integrate the system with other devices such as temperature chambers and dimensional measurement devices. Libraries of pre-configured test methods for standard composite test types are available to help simplify the management of the wide range of tests commonly encountered in a composite testing lab.
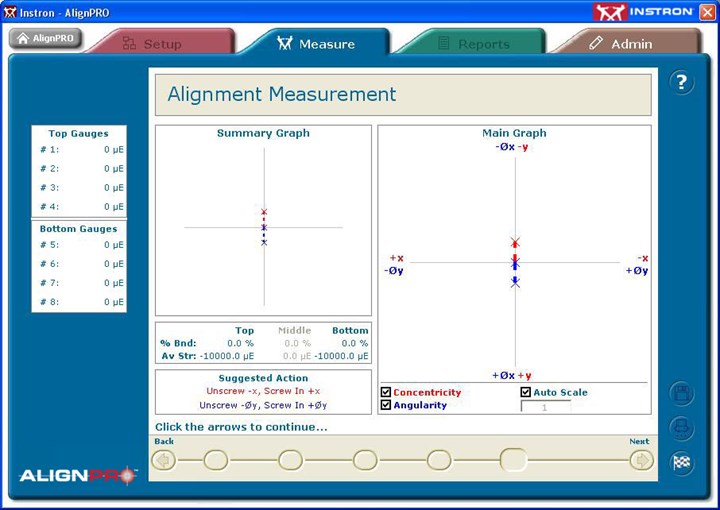
Fig. 2. Alignment software display.
Security is also an important consideration. Key elements of security are verification and validation of users, electronic signatures and traceability. Typically, verification and validation of users means regulating the access of specific individuals to different functions within the software. For example, a lab manager will be able to create and modify test methods, while an operator will have limited access to the test parameters and only be able to run methods that have already been pre-configured. Electronic signatures enable users with the appropriate rights to approve test results and documents.
It is also possible to produce audit trails of changes to methods and test results. For example, when a new version of a test standard is published and a test method is modified, this will be recorded in a file revision number along with a list of all changes.
The future of composites testing
Composites testing will continue to be driven by the development of new materials and processes and the expansion of new markets for composite materials. The mechanical testing of composite materials is complex and involves a range of test types and standards, along with the need to condition and test in a variety of environments. Integrated test systems with aligned grips, interchangeable fixtures and intuitive software with pre-configured methods will continue to make testing as easy, accurate and efficient as possible.
Related Content
Glass-coated magnetic microwires for nondestructive composites monitoring
Glass-coated, amorphous microwires combine nanometer to micrometer diameters, enabling embedding into composites without degrading mechanical properties.
Read MoreMaterial equivalence testing in shared composites databases
In response to traditionally proprietary polymer matrix composites (PMC) qualifications, NCAMP continues its efforts to make material property databases publicly available.
Read MoreNumerical tool with mean stress correction demonstrated for fatigue life estimation of thermoplastic composites
To aid design of fatigue-resistant structures, Econ Engineering has developed an algorithm to evaluate ply-based cyclic stiffness degradation combined with an FE failure check, validated for a CF/PAEK pressure vessel.
Read MoreMeasuring ply-wise deformation during consolidation using embedded sensors
Strip-type shape sensor method claims real-time measurement of ply-wise deformation.
Read MoreRead Next
Composite testing challenges, Part 1: Introduction to mechanical testing of composites
A range of standardized mechanical tests for complex composites are available and still under development for materials development, design and quality control requirements.
Read MoreComposite testing challenges, Part 2: Strain measurement for the mechanical testing of composites
Recent developments in contact and noncontact strain measurement methods offer similar performance with additional benefits for composite material testing.
Read MoreFrom the CW Archives: The tale of the thermoplastic cryotank
In 2006, guest columnist Bob Hartunian related the story of his efforts two decades prior, while at McDonnell Douglas, to develop a thermoplastic composite crytank for hydrogen storage. He learned a lot of lessons.
Read More