Compression Molding of Composites
Compression molding is a widely employed technique in composite manufacturing, involving the use of heat and pressure to shape composite materials. In this process, a pre-measured amount of composite material, often in the form of sheets or pellets, is placed into a mold cavity. The mold is then closed and subjected to high pressure and temperature, allowing the material to conform to the shape of the mold. As the material compresses and solidifies, it forms the desired product. Compression molding is favored for its ability to produce complex shapes with high fiber volume fractions, ensuring strong and consistent composite parts.
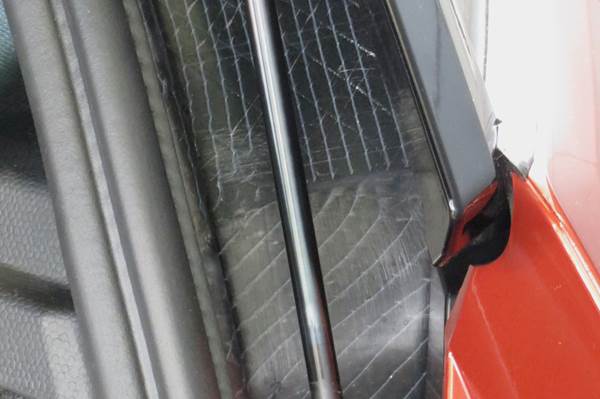
Latest Compression Molding Articles
VIEW ALLHyWaSand demonstrates large-series production potential for automotive TP sandwich components
Storage compartment flap for truck interior produced via fully automated continuous fiber thermoplastic sandwich molding technology shows suitability for series manufacture.
Read MoreInduction heating platen achieves dynamic temperature management
JEC World 2024: Roctool is introducing the R-IDS, a patented heated platen that aims to make mass production more accessible for composites manufacturing.
Read MoreThermoplastic tape friction tester completed at TPRC
Delivered and implemented at Toray Advanced Composites, the setup seeks to eliminate defects during hot press forming thermoplastic tapes.
Read MoreENRX, Roctool collaborate to advance mold electrification
Plastics and composites manufacturers will benefit from Roctool’s heat and cooling induction for molding processes, with increased technical service support and capability demonstrations on a global scale.
Read MoreImproving carbon fiber SMC simulation for aerospace parts
Simutence and Engenuity demonstrate a virtual process chain enabling evaluation of process-induced fiber orientations for improved structural simulation and failure load prediction of a composite wing rib.
WatchComposite molding compound replaces Invar for lightweight small satellite structures
Patz Materials and Technologies and Lawrence Livermore National Laboratory developed a new monolithic optics housing with 80% less weight, near-zero CTE and the high-volume manufacturing required for commercial space.
Read MoreKnowledge Centers
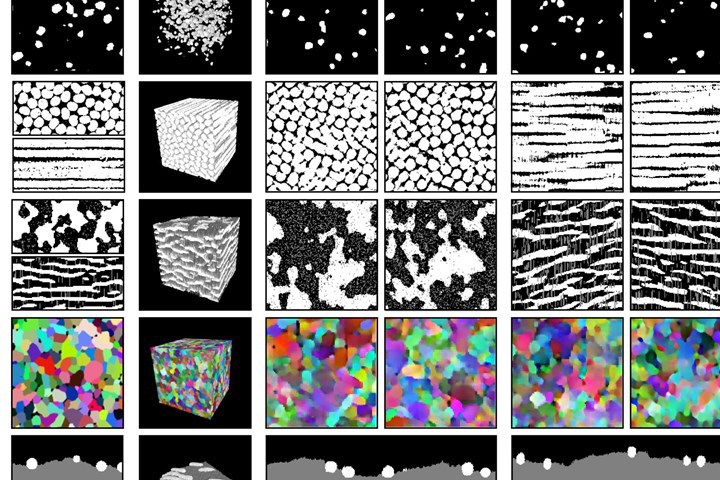
Review the state of the art in design, simulation, failure analysis, digital twins, virtual testing and virtual inspection.
LEARN MORELatest Compression Molding News And Updates
Heating platens deliver precise, uniform compression molding temperature control
CAMX 2023: Venango Machine features MultiZone heating platens with a control system included, capable of reducing mold surface temperature variation by almost 400% during the compression molding process.
Read MoreTool Gauge, Victrex partner to develop co-molded composite aircraft parts
Novel hybrid overmolding technology achieves novel thermoplastic composite parts to replace machined aluminum components on commercial aircraft, as well as reduce manufacturing costs and timeline.
Read MoreOrbital Composites licenses AMCM technology
Additive manufacturing compression molding (AMCM), co-developed with ORNL, combines robotic AM and continuous fiber technologies to revolutionize high-volume composites manufacturing.
Read MoreToray develops rapid integrated press molding technology for CFRP mobility components
The process and material innovation simultaneously shapes, molds, thermosets and bonds the core and skin in the same mold, achieving this 10 times faster than conventional autoclave molding setups.
Read MoreTNL Applied Composites Manufacturing course begins February 2023
Hybrid, seven-session class helps participants learn the tricks of different composites manufacturing technologies from wet layup to pultrusion.
Read MoresensXPERT Digital Mold earns 2022 AVK Innovation Award
Data-driven sensor technology optimizes and increases composites manufacturing efficiencies in real time, achieved through collaborative network.
Read MoreFeatured Posts
Plant tour: Arris Composites, Berkeley, Calif., U.S.
The creator of Additive Molding is leveraging automation and thermoplastics to provide high-volume, high-quality, sustainable composites manufacturing services.
Read MoreHybrid process marries continuous, discontinuous composites design
9T Labs and Purdue applied Additive Fusion Technology to engineer a performance- and cost-competitive aircraft bin pin bracket made from compression-molded continuous and discontinuous CFRTP.
Read MoreManufacturing the MFFD thermoplastic composite fuselage
Demonstrator’s upper, lower shells and assembly prove materials and new processes for lighter, cheaper and more sustainable high-rate future aircraft.
Read MoreJEC World 2023 highlights: Innovative prepregs, bio-resins, automation, business development
CW’s Jeff Sloan checks in with JEC innovations from Solvay, A&P, Nikkiso, Voith, Hexcel, KraussMaffei, FILL, Web Industries, Sicomin, Bakelite Synthetics, Westlake Epoxy and Reliance Industries.
Read MoreJEC World 2023 highlights: Recycling, biocomposites, smaller equipment and expanding brands
CW senior technical editor Ginger Gardiner addresses some of this year’s hot topics, ranging from novel biocomposites and recycling technology solutions from myriad startups to upgraded, but equally sustainable, equipment from well-established companies.
WatchPEEK vs. PEKK vs. PAEK and continuous compression molding
Suppliers of thermoplastics and carbon fiber chime in regarding PEEK vs. PEKK, and now PAEK, as well as in-situ consolidation — the supply chain for thermoplastic tape composites continues to evolve.
Read More