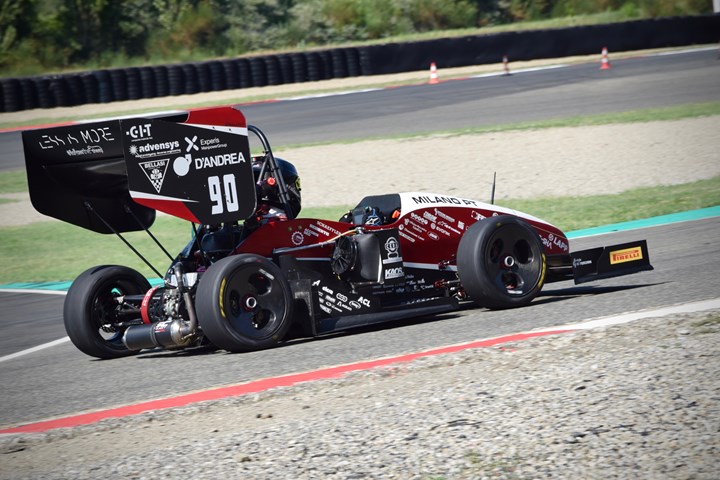
Photo Credit: Exel Composites
To help develop automotive engineers of the future, the Formula Society of Automotive Engineers (Formula SAE) is a global student competition that pits a variety of university teams against each other to develop small, Formula-style race cars. These teams are increasingly finding composites to be the ideal solution for pushing their vehicles’ performance to the next level.
For example, for its 2019 competition vehicle, the student-led racing department of the university Politecnico di Milano (Milan, Italy), called Dynamis PRC, was looking for a new material to improve the performance of its car’s steering column and suspensions. In 2018, the team’s car placed in the top 10 of the competitions it entered, but Dynamis wanted to find a way to score even higher the next year.
Andrea Vezzoli, technical director at Dynamis, explains that the team had specific goals: “There were two main objectives we wanted to achieve for that year’s model, named the DP11. The first was reduce the weight of the car and the second was to improve the suspension because we felt that in the previous year, this is what had held us back.”
Singling out the steering column as the main area for weight reduction, Dynamis began searching for new materials. Making weight improvements was critical because every other team would also be finessing their cars, many of which had received support from major car manufacturers.
When researching new materials, Dynamis connected with Politecnico di Milano alumnus Francesco Ierullo, who is currently head of sales for South and West Europe and IMEA at composites fabricator Exel Composites (Vantaa, Finland), who agreed to help the team.
Beyond 2020, Dynamis is working toward its next goal: electric vehicles.
“[Exel Composites is] always looking for ways to get composites into the hands of students, because they are the engineers of the future and the more experience they have with composites now, the better equipped they will be when they work in the field,” says Ierullo. “More and more fields of industry are using composites, but direct student exposure to the material remains low. Whatever we can do to help is always crucially important to us.”
After reviewing the focus areas with the racing team, Exel Composites suggested several options of carbon fiber tubes for the vehicle’s steering column.
According to Ernesto Ricciardi, head of the suspension and drivetrain department at Dynamis, the team built a database of potential materials and used an algorithm to indicate which material would be best for each vehicle component. “Once we input the properties of Exel’s products into the database, the algorithm told us to use it every time without fail. It was on another level compared to everything else we had tried before,” he notes.
The team ended up selecting several lengths and sizes of Exel’s carbon fiber/epoxy tubes, ranging in diameter from 105 to 299 millimeters, for applications on the driver interface, vehicle suspension and aerodynamic structures. Exel manufactures the tubes via a pullwinding process.
“We were impressed by the performance of the material,” adds Ricciardi. The carbon fiber tubes ended up reducing weight on the steering column by 800 grams, which helped shave two seconds off the vehicle’s lap time, while also increasing the rigidity of the vehicle’s suspension. In addition, the car’s steering column was required to to resist three times the peak load, which for the original design was 100 newton meters. Switching from metal to a stronger carbon fiber part enabled the team to push the peak load to 140 newton meters.
One reservation that Dynamis had when transitioning from metal to composites was the challenge that come with learning a new material. For example, team worried about potential delamination issues when using a waterjet to cut the material, and knew that the car’s frame would need to be modified to account for the need to adhesively bond the composite parts to the frame rather than welding them as they did with metal parts. Exel worked with the team to recommend the best options for connecting and cutting the composite materials.
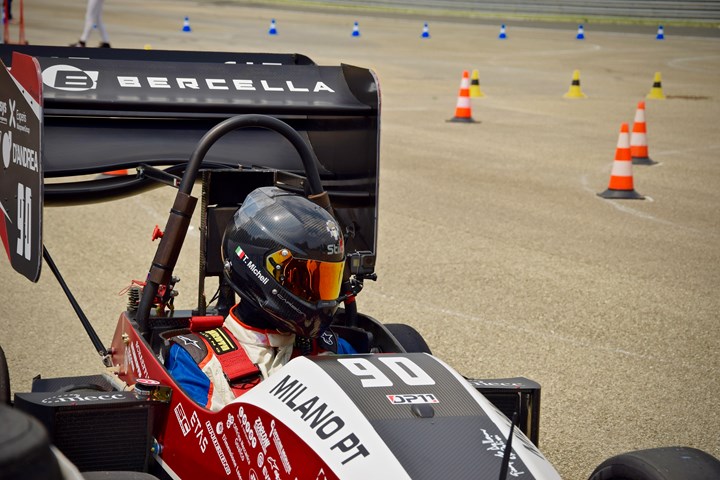
Photo Credit: Exel Composites
With the new carbon fiber structures installed, Dynamis took the vehicle to four competitions in 2019. At Formula SAE competitions, teams compete in a variety of events that measure qualities of each car. Stopping time, acceleration and agility are evaluated, and teams are awarded points for each focus area. The team that scores the most points wins the competition.
The team won overall at its first and third competitions that year, in the Netherlands and Italy. The fourth competition, held in Germany, was the toughest, Vezzoli says. With some of the world's largest car manufacturers located in Germany, he says, “many of the Germany teams are directly linked with their local car manufacturers, so we knew the car would have to perform well to help us hit our targets.” Despite the challenge, Dynamis placed third, making the season one of its most successful to date.
The 2020 Formula SAE events did not occur as planned due to the coronavirus pandemic, but Dynamis says it is looking ahead and working toward its next goal: electric vehicles. “One of our long-term plans was to begin competing in the electric car version of Formula SAE. This was one of the reasons behind our strategic weight shedding focus for the 2019 season,” explains Vezzoli.
Ricciardi adds that for the next vehicle iteration, the team plans to use more of Exel’s composite products, incorporating glass fiber composites into the vehicle’s aerodynamic wings for additional lightweighting.
Related Content
Materials & Processes: Fabrication methods
There are numerous methods for fabricating composite components. Selection of a method for a particular part, therefore, will depend on the materials, the part design and end-use or application. Here's a guide to selection.
Read MoreASCEND program update: Designing next-gen, high-rate auto and aerospace composites
GKN Aerospace, McLaren Automotive and U.K.-based partners share goals and progress aiming at high-rate, Industry 4.0-enabled, sustainable materials and processes.
Read MorePlant tour: Joby Aviation, Marina, Calif., U.S.
As the advanced air mobility market begins to take shape, market leader Joby Aviation works to industrialize composites manufacturing for its first-generation, composites-intensive, all-electric air taxi.
Read MoreMcLaren celebrates 10 years of the McLaren P1 hybrid hypercar
Lightweight carbon fiber construction, Formula 1-inspired aerodynamics and high-performance hybrid powertrain technologies hallmark this hybrid vehicle, serve as a springboard for new race cars.
Read MoreRead Next
3D printing, composite materials enable motorsports design flexibility
A collegiate Formula SAE racing team used Windform carbon fiber-filled composite materials and laser sintering technology to streamline part design.
Read MoreThe untapped potential in Formula 1 composite manufacture
Formula 1’s midfield teams are struggling to bridge the gap to their better resourced frontrunning counterparts. Could Industry 4.0 composites manufacturing automation level the playing field?
Read MoreRacing to build tomorrow’s automotive composites workforce
Recent graduates share experiences gained from collegiate automotive design, engineering and motorsport competition Formula SAE.
Read More