EconCore announces partnership for sustainable car concept project
Dubbed Luca, the concept car incorporates EconCore’s recycled PET honeycomb cores, as well as other waste materials including horse hair, coconut fiber, flax and plastic bottles.
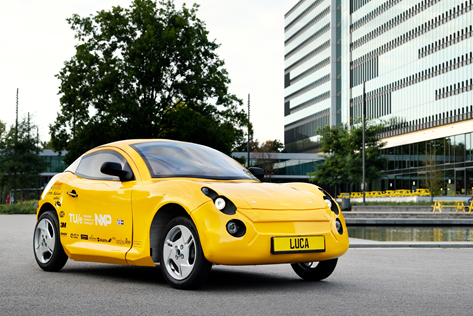
Photo Credit: Bart Van Overbeeke Photografie
Thermoplastic honeycomb core company, EconCore (Leuven, Belgium) recently announced itself as a partner of the Luca project, which aims to build a car made entirely out of recycled materials. The project, developed by the TU/ecomotive team at Eindhoven University of Technology (TU/e; Eindhoven, Netherlands), was launched on Oct. 8, 2020.
The concept car is a lightweight, electric vehicle designed and built by 22 students in 18 months, according to the team. The rationale behind the project is to demonstrate that waste can be a valuable resource, while gaining business, engineering and manufacturing skills and experience.
“We’ve been involved with this project for the last four years now and each year our involvement has increased,” says Wouter Winant, technical manager at EconCore. “We’re delighted to be supporting the TU/ecomotive team as we share similar values in terms of using technology to produce sustainable products and minimize waste. Through innovation, we can create much more sustainable solutions and the Luca car project demonstrates that in such a clever way.”
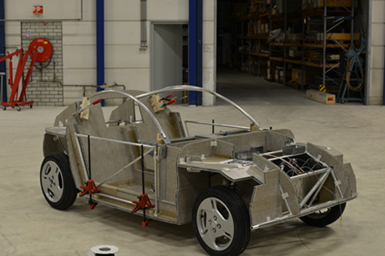
Chassis made using EconCore’s recycled PET honeycomb cores. Photo Credit: TUecomotive
According to the company, it supplied more than 20 square meters of recycled PET honeycomb cores for the car’s design, incorporated into the chassis, seat support structure, parts of the dashboard and the battery housing. After lamination of the composite skins, the strong, lightweight panels were reportedly used in most of the structural parts of the car. In addition to supplying the material, EconCore also provided extensive technical advice and consulting services.
Winant continues: “The team asked for specific data and advice on how to optimally design and use the panels. We carried out tensile tests on the composite materials and three-point bending tests on small panel samples, with different core thicknesses and skin materials. The mechanical data from these tests provided the optimum design of sandwich panel with the right balance between sustainability, weight, strength and stiffness.”
One of the challenges the TU/ecomotive team had, EconCore says, was gluing the recycled PET core to a composite sheet consisting of flax fibers and a recycled polyolefin matrix contributed by other partners. These two materials do not work well together when using adhesive.
EconCore says its technical advice overcame this problem. A polyester non-woven fleece was used to cover the surface area of the honeycomb core. This is compatible with the adhesive and composite skin layers. A thin PET barrier film was used to ensure the adhesive glue did not flow through the fleece into the honeycomb cells, keeping the panel lightweight. All the materials were made of recycled PET, maintaining the aim of using recycled materials in a circular economy.
“What’s apparent to us, now the project is complete, is how the Luca car demonstrates just how versatile the recycled PET honeycomb core panels are, with the potential range of applications it can be used for,” concludes Winant. “Not just in automotive terms but in other industrial and consumer applications where strength, rigidity and light-weight are such important characteristics. The potential is huge.”
According to the the TU/ecomotive news release, the Luca has two electric motors, a range of 220 kilometers and a top speed of 90 kilometers per hour. In addition to recycled PET honeycomb cores, other waste materials include horse hair, coconut fiber, flax and plastic bottles.
Related Content
Materials & Processes: Fibers for composites
The structural properties of composite materials are derived primarily from the fiber reinforcement. Fiber types, their manufacture, their uses and the end-market applications in which they find most use are described.
Read MoreMaterials & Processes: Fabrication methods
There are numerous methods for fabricating composite components. Selection of a method for a particular part, therefore, will depend on the materials, the part design and end-use or application. Here's a guide to selection.
Read MoreASCEND program update: Designing next-gen, high-rate auto and aerospace composites
GKN Aerospace, McLaren Automotive and U.K.-based partners share goals and progress aiming at high-rate, Industry 4.0-enabled, sustainable materials and processes.
Read MoreNovel dry tape for liquid molded composites
MTorres seeks to enable next-gen aircraft and open new markets for composites with low-cost, high-permeability tapes and versatile, high-speed production lines.
Read MoreRead Next
EconCore, Toray and Bostik collaborate on FST-qualified thermoplastic honeycomb panels
Developed for mass transportation applications, including aircraft interiors, the material improves upon the cost, sustainability and versatility of conventional sandwich layup.
Read MoreCW’s 2024 Top Shops survey offers new approach to benchmarking
Respondents that complete the survey by April 30, 2024, have the chance to be recognized as an honoree.
Read MoreFrom the CW Archives: The tale of the thermoplastic cryotank
In 2006, guest columnist Bob Hartunian related the story of his efforts two decades prior, while at McDonnell Douglas, to develop a thermoplastic composite crytank for hydrogen storage. He learned a lot of lessons.
Read More