General Atomics Aeronautical developing tool-less thermoplastics composites process
Aerospace manufacturer General Atomics Aeronautical Systems Inc. is developing a novel process for the fabrication of thermoplastic composite structures that obviates the need for traditional molds or tooling.
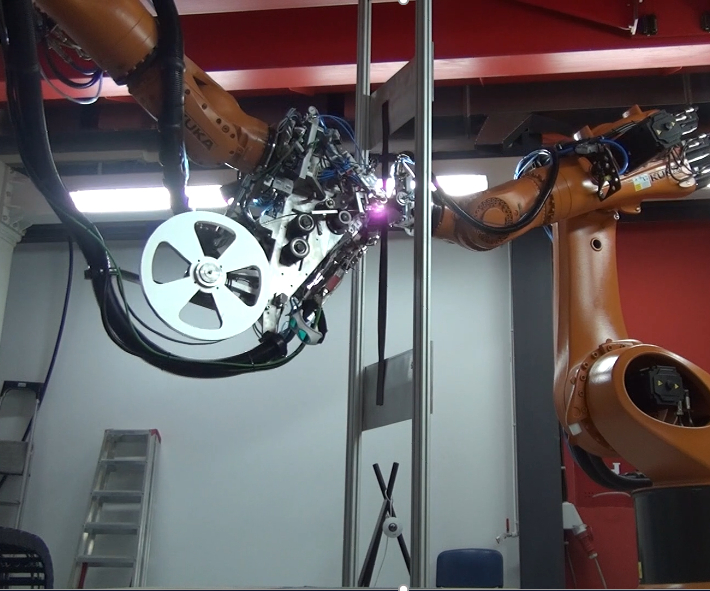
General Atomics' tool-less thermoplastic composites process employs two robots. One (left) applies the carbon fiber/thermoplastic tape. The other (right) provides a movable tooling surface against which the tape is applied.
Aerospace manufacturer General Atomics Aeronautical Systems Inc. (GA-ASI, San Diego, CA, US) is developing a novel process for the fabrication of thermoplastic composite structures that obviates the need for traditional molds or tooling. The system is expected to have application in the aerospace, space, marine and wind energy end markets.
Although it has not been formally named, the tool-less process uses two 6-axis robots working cooperatively to place thermoplastic tape into open space within a metallic or similar frame that provides the boundaries of the structure being fabricated (see photo). Composite Automation LLC (Cape Coral, FL, US), using Mikrosam (Prilep, Macedonia) equipment, worked with GE-ASI to develop the automation.
One robot consists of a standard unidirectional tape placement system that provides laser heating to perform in-situ consolidation of the thermoplastic material. The second “support” robot works directly opposite the automated tape layer (ATL) and consists of a flat metallic surface, providing, in effect, a movable tooling surface against which the ATL places its tape. The tape head and the support head thus move together through 3D space, placing material. Each end of each tape placed is anchored to the frame, which can assume a variety of shapes, depending on the application. Further, the tape can be manipulated by the robotics to change direction within the 3D space to build contoured and complex shapes.
John Geriguis, innovations leader/advanced product development at GA-ASI, has been working with Adam Jones, manufacturing engineering manager, and Paul Sherman, design engineer, on this technology for four years. He says development of the process is ongoing, noting that the company is still working to optimize software systems guiding the robotics. He also says the process is highly dependent on a camera-based in-situ inspection system that detects material and other flaws during the placement process; the system, called real-time virtual assembly tooling (RVAT), developed for GA-ASI by Trilion Quality Systems (King of Prussia, PA, US), is designed to compare the as-manufactured structure with the as-designed CAD data, and then implement tape placement adjustments on the fly to maintain compliance with design specifications.
GA-ASI, says Geriguis, has evaluated several thermoplastic resin systems using the process, including polyetheretherketone (PEEK). However, Geriguis reports that the company has had the most success with Toray’s TenCate Advanced Composites’ (Morgan Hill, CA, US) Cetex TC1225 low-melt polyaryletherketone (PAEK) using a Toray carbon fiber reinforcement.
GA-ASI has applied for a US patent of the process, but Geriguis says this is being done primarily to protect the company’s use of the technology. In fact, says Geriguis, “we hope that others might want to partner and help develop this technology and mature it.”
Interest in the process so far, outside of General Atomics Aeronautical, has come from NASA, which, says Geriguis, sees the potential for its use to build structures in a space environment. He also believes the process could be deployed effectively to fabricate aircraft fuselage and wing structures, as well as wind turbine blades and naval vessels.
Related Content
Dustless, mobile solution for on-site wind turbine blade repurposing
Denmark-based Isodan Engineering ApS translated its expertise in mobile, shipping container-based newspaper recycling systems to solve a need for breaking down wind turbine blades on-site for reuse.
Read MorePlant tour: AvCarb, Lowell, Mass., U.S.
Composites are often selected for their structural properties, but at AvCarb, innovation in carbon fiber-based products has driven fuel cell technology advances for decades.
Read MoreJEC World 2023 highlights: Recyclable resins, renewable energy solutions, award-winning automotive
CW technical editor Hannah Mason recaps some of the technology on display at JEC World, including natural, bio-based or recyclable materials solutions, innovative automotive and renewable energy components and more.
Read MoreDrag-based wind turbine design for higher energy capture
Claiming significantly higher power generation capacity than traditional blades, Xenecore aims to scale up its current monocoque, fan-shaped wind blades, made via compression molded carbon fiber/epoxy with I-beam ribs and microsphere structural foam.
Read MoreRead Next
Combining multifunctional thermoplastic composites, additive manufacturing for next-gen airframe structures
The DOMMINIO project combines AFP with 3D printed gyroid cores, embedded SHM sensors and smart materials for induction-driven disassembly of parts at end of life.
Read MoreThe next-generation single-aisle: Implications for the composites industry
While the world continues to wait for new single-aisle program announcements from Airbus and Boeing, it’s clear composites will play a role in their fabrication. But in what ways, and what capacity?
Read More“Structured air” TPS safeguards composite structures
Powered by an 85% air/15% pure polyimide aerogel, Blueshift’s novel material system protects structures during transient thermal events from -200°C to beyond 2400°C for rockets, battery boxes and more.
Read More