Rize XRIZE composite printer now compatible with Synopsys platform for 3D medical printing
Platform combination enables the creation of affordable, full-color and functional 3D physical replicas from medical imaging for orthopedic, maxillofacial and cardiovascular application fields.
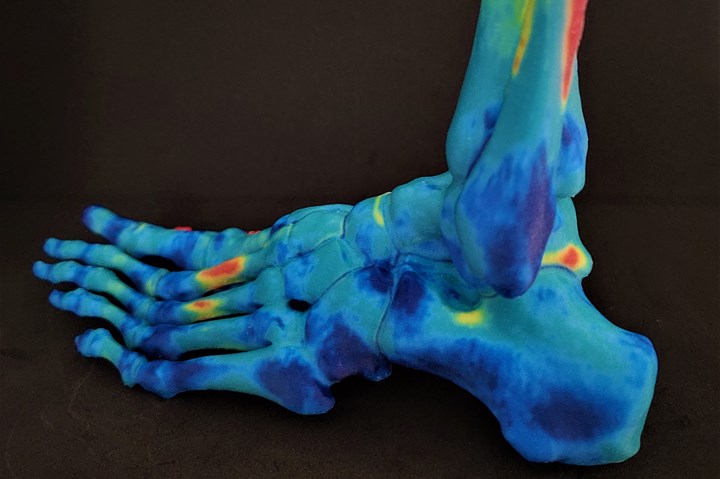
Photo Credit: Rize Inc.
Next-generation additive manufacturing company Rize Inc. (Concord, Mass., U.S.) has announced that its XRIZE full-color industrial desktop composite 3D printing platform is compatible with Synopsys’ (Mountain View, Calif., U.S.) FDA 510(k)-cleared Simpleware software. More specifically, Simpleware software is cleared for creating models from medical imaging that can be exported to compatible printers such as XRIZE to produce physical replicas used for diagnostic purposes in the field of orthopedic, maxillofacial and cardiovascular applications. As part of its clearance process, Synopsys is able to use the XRIZE platform to validate an end-to-end DICOM to 3D print workflow, enabling a 3D point-of-care (POC) solution for end-users.
According to a June 2019 Allied Market Research report, 3D-printed healthcare applications are projected to reach $3.6 billion by 2026. “3D printing is becoming increasingly important in surgery, and the use of 3D-printed models has been shown to increase our understanding of musculoskeletal diseases,” says Professor Alister Hart MD, orthopedic surgeon, Royal National Orthopaedic Hospital, U.K. “We’re excited to work with RIZE’s 3D printing platform along with the Simpleware software solutions for image segmentation. Many aspects of surgical planning can benefit from 3D models — for example, to illustrate the distribution of bone density at various depths in the bone and to assist in positioning and screw placement.”
Complementing the Simpleware, XRIZE will aid creating highly durable anatomical models, surgical guides and implants with minimal effort, with vibrant color highlights on anatomical regions, bone densities and landmarking, according to Rize. Further, the printer’s UL GREENGUARD certification and minimal post-processing reportedly delivers a safety advantage while empowering clinicians and innovators with intelligent workflows that dramatically compress time and costs by 80-90%.
“Our technology has a proven track record for processing 3D images and creating models for a wide variety of applications,” says Terry Ma, VP of engineering at Synopsys. “Adding regulatory clearance for point-of-care 3D printing enables our growth in the point-of-care clinical space, where Simpleware software and our team’s technical expertise will allow for better patient care and a faster workflow for medical professionals.”
Related Content
-
Materials & Processes: Fabrication methods
There are numerous methods for fabricating composite components. Selection of a method for a particular part, therefore, will depend on the materials, the part design and end-use or application. Here's a guide to selection.
-
PEEK vs. PEKK vs. PAEK and continuous compression molding
Suppliers of thermoplastics and carbon fiber chime in regarding PEEK vs. PEKK, and now PAEK, as well as in-situ consolidation — the supply chain for thermoplastic tape composites continues to evolve.
-
Plant tour: Joby Aviation, Marina, Calif., U.S.
As the advanced air mobility market begins to take shape, market leader Joby Aviation works to industrialize composites manufacturing for its first-generation, composites-intensive, all-electric air taxi.