Stratasys collaborates with Lockheed to qualify composite materials for space, aviation end-use parts
Report made public by Metropolitan State University of Denver delivers qualification data for Antero 840CN03 for additively manufactured end-use parts requiring high thermal and chemical resistance, and ESD properties.
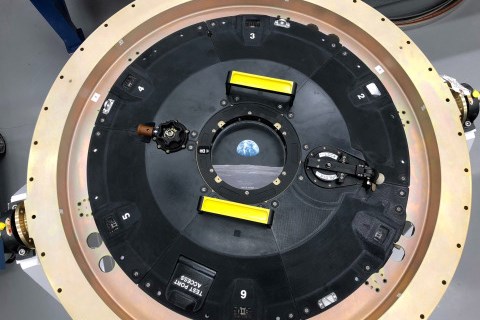
Hatch cover for the Orion spacecraft by Lockheed Martin printed in Antero840CN03. Photo Credit: Stratasys, Lockheed Martin
Polymer 3D printing solutions provider Stratasys Ltd. (Eden Prairie, Minn., U.S. and Rehovot, Israel), announced on March 29 that is has joined forces with Lockheed Martin (Bethesda, Md., U.S.) to provide baseline material qualification data for Antero 840CN03 filament material which enables the material to be used for additively manufactured (AM) aerospace parts, such as those on the Orion Spacecraft, on Stratasys production-grade 3D printers. Stratasys and Lockheed Martin have released this data through a collaboration with Metropolitan State University of Denver (MSU Denver, Colo., U.S.).
“We are continually looking for ways to drive innovation for flight-qualified materials and additive manufacturing is key to that endeavor,” Cris Robertson, associate manager of advanced manufacturing at Lockheed Martin Space, says. “Through our collaboration with Stratasys and MSU Denver, we have collected the data necessary to qualify Antero 840CN03 for flight parts and we are now able to expand our use of the material beyond our initial applications on the Orion vehicle.”
Designed for space-ready performance, Antero 840CN03 is a blended and functionalized polyetherketoneketone (PEKK)-based high-performance, electrostatic dissipative (ESD) thermoplastic composite material. It was developed specifically for production-grade Stratasys FDM 3D printers that meets ESD performance and NASA (Washington, D.C., U.S.) outgassing requirements, while also exceeding the flame, smoke and toxicity (FST) characteristics required for aviation applications.
During this first phase of qualification, a baseline set of data was collected by printing more than 280 test coupons in Antero 840CN03 on Stratasys Fortus F900 3D printers at Lockheed Martin in Littleton, Colo., and Stratasys Direct Manufacturing in Belton, Texas. Coupons were tested for tensile strength properties, a key mechanical property for design. Data collected confirmed the high performance of the Antero material as well as the consistent mechanical properties which have been previously shown in academic studies. Future phases of testing will expand to additional relevant properties, giving design engineers additional data to work with in applying Antero to other part types and environments.
Further material testing will take place in future phases providing for full characterization of this material.
“These types of research and development collaborations with leading companies like Stratasys and Lockheed Martin enable our students to be well prepared to help their future aerospace employers with adopting the latest technology in the industry,” Mark Yoss, director of the Advanced Manufacturing Sciences Institute at MSU Denver, notes. “By publishing this material qualification data, we can help move the aerospace industry forward by establishing more standards in additive manufacturing.”
MSU Denver is educating and training the manufacturing workforce of the future using additive and subtractive manufacturing that can reduce costs and increase application capabilities.
Stratasys and Lockheed Martin have previously worked together to collect and release material characteristics data. Most recently in 2018, as members of America Makes, the companies released allowable data for SABIC (Riyadh, Saudi Arabia) Ultem 9085 resin printed on a Stratasys Fortus 900mc 3D printer. By continuing to publicly release material qualification data, the companies hope to enable further adoption of AM in aerospace applications and use-cases.
Through this collaboration with MSU Denver, full access to the data report is available to the public online. Further material testing will take place in future phases providing for full characterization of this material.
The Stratasys and Lockheed Martin teams will also both be present at this year’s Space Symposium in Colorado Springs, Colo., U.S.
Related Content
Thermoplastic composites welding advances for more sustainable airframes
Multiple demonstrators help various welding technologies approach TRL 6 in the quest for lighter weight, lower cost.
Read MoreManufacturing the MFFD thermoplastic composite fuselage
Demonstrator’s upper, lower shells and assembly prove materials and new processes for lighter, cheaper and more sustainable high-rate future aircraft.
Read MoreJeep all-composite roof receivers achieve steel performance at low mass
Ultrashort carbon fiber/PPA replaces steel on rooftop brackets to hold Jeep soft tops, hardtops.
Read MoreCFRTP upper stage propellant tank
PROCOMP uses in-situ consolidation AFP and ultrasonic welding to demonstrate lightweight, novel tank design.
Read MoreRead Next
Stratasys produces 500 3D-printed parts for the Lotus Type 62-2 coachbuilt sports car
Numerous 3D-printed composite mounting brackets, exterior components and a solid firewall sandwich core bring 1960s-style supercar automaking into the 21st century.
Read MoreCW’s 2024 Top Shops survey offers new approach to benchmarking
Respondents that complete the survey by April 30, 2024, have the chance to be recognized as an honoree.
Read MoreFrom the CW Archives: The tale of the thermoplastic cryotank
In 2006, guest columnist Bob Hartunian related the story of his efforts two decades prior, while at McDonnell Douglas, to develop a thermoplastic composite crytank for hydrogen storage. He learned a lot of lessons.
Read More