Composites opportunities in a growing infrastructure market: CW Trending episode 2
This episode of CW Trending, sponsored by Composites One, takes a look at the opportunities for expanded use of composites in infrastructure applications.
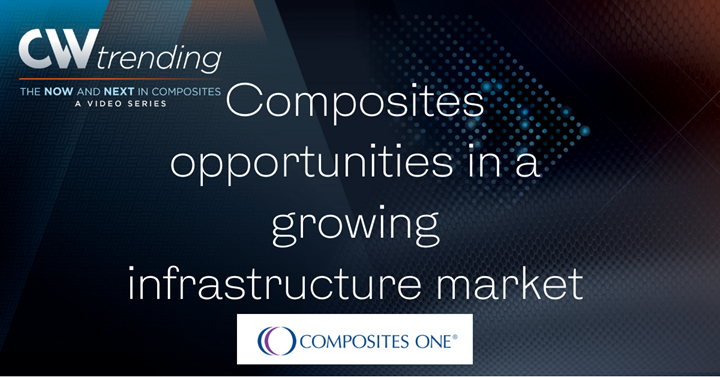
With the potential of increased investment in infrastructure coming from the U.S. government, civil engineers will be facing myriad challenges when it comes to material use in bridges, utility systems, waterways, and much more. Jeff Sloan Editor-in-Chief of CompositesWorld, Joe Fox, President of FX Consulting, and Gareth Williams, strategy director at the National Composites Centre (NCC), discuss where the opportunities are for composites, the hurdles, the advantages composites convey, and how those advantages can be leveraged into real applications.
Transcript
Jeff Sloan
Hello, everyone and welcome to CW Trending. My name is Jeff Sloan, I am editor in chief of Composites World. CW Trending is a new product for CW. This is a video-based program designed to explore the people, ideas, and as the name implies the trends that are shaping the composites industry. In our topic in this episode is composites use in infrastructure or in deference to one of our guests, Gareth Williams, since he is from the UK, it is composites use and infrastructure. We have two presenters today; they are Joe Fox and Gareth Williams. We are going to hear from each of them first. I'll ask them a few questions when they are done, and then we are going to open it up to Q&A from your audience. If anybody in the audience has a question at any point during the presentations, you can type that question under the question tab in in the in the webinar dashboard. The chat function is also available if you want to chat with other attendees. If you do post a question in chat, we will try to grab that and move it over into the Q&A tab so we can pay attention to that. We will try to get through all the questions as many as we can, before we wrap up here. I want to thank you for attending, so let's go ahead and get started. Our first presenter today is Joe Fox. Joe is president of FX Consulting, a consulting firm for the specialty chemicals and materials industry. Joe is a chemist by training and has a bachelor's degree in chemistry from Lehigh University, and a PhD in chemistry from Penn State. He also worked for several years at Ashland, and then eventually what is now in EOS. Our second presenter today is with Gareth Williams, he's an aeronautical engineer who developed world leading research into self-healing carbon fiber composites during his PhD at the University of Bristol. He is currently the strategy director at the National Composite Center in Bristol, in the UK. So, Joe I am going to turn it over to you and let's get started.
Joe Fox
All right, very good. Thank you, Jeff. It is a pleasure to be here, and as my title suggests, in the next 10 or 15 minutes, I'm going to connect FRP composites to two important documents from the American Society of Civil Engineers, our ASC. those documents are their 2021 infrastructure report card, and their future World Vision. I am really going to try and emphasize the trends that are in those two documents. I am going to start with my take home message and finish with my take home message. My take home message is that there is an extremely good fit between FRP composites, and our nation's infrastructure needs both today and in the future. I strongly believe that to be the case, and I hope you will too when I am done with my presentation. This slide lists some of the key attributes of FRP composites for infrastructure applications. They are lightweight, easy to install, corrosion resistant, extremely durable, and resilient. Now all of these are important for infrastructure and construction applications, but as a member of ASC III, I know that resiliency right now is a particularly hot topic. A little bit about the 2021 infrastructure report card. This is a document that ASC II releases every four years, they put a lot of effort into this report card, and it gets a lot of visibility and a lot of attention on Capitol Hill. The 2021 version was released in early March, and you can see the scores here. Needless to say, this is not the kind of report card that you want your kids to come home with. There are only two B grades, there are four C grades, and the rest of the grades are either D, D minus or D plus the overall grade improved slightly from a D plus to a C minus in 2021, but still very disappointing. ASC divides infrastructure into the 17 categories that you see here. I am not going to have time to talk about all of them, but I am going to talk about seven of them. There are many opportunities for improvement and let us start with bridges. They get a see FRP has been used to construct more than 500 bridges in North America. The most notable examples come from the states of Florida and Maine. I am going to highlight the state of Michigan on the next slide and there has also been considerable bridge activity in Canada. As you can see from the pictures, there are long span bridges, short span bridges, bridges over rivers, and there are bridges over highways. Some of these bridges use elements that are made completely out of FRP rebar. Others use FRP rebar to reinforce concrete or both. FRP has also been used to strengthen and repair bridges. In this case FRP wraps like the one shown here are used to strengthen and repair the bridge. This is usually done with carbon fiber reinforced polymer wraps because CFRP is stiffer and glass fiber. Originally, this technology was used in California to provide resiliency against earthquakes. Remember, the resiliency is important, but it is used in other places. For example, this is a picture of the Rouge River Bridge which is Michigan's largest bridge and M dot has used these CFRP wraps to strengthen more than 200 columns on that bridge. There are many other examples of FRP strengthening and sometimes this type of repair is referred to as bonded FRP or externally bonded FRP. And actually AASHTO. The American Association of State Highway and Transportation Officials has issued this manual on the use of bonded FRP systems for repair. FRP can also be used for pedestrian bridges and walkways that and the key attributes here are lightweight and durability. And here are some examples from Ohio and from Lake Tahoe. FRP can also be used to add pedestrian walkways to an existing bridge. Here is an example of a cantilever walkway that has been added to an existing bridge in Niagara New York. So, what you've got here FRP was selected, because it enables you to add the walkway to the bridge without adding a lot of extra weight. And what you've got here is lightweight addition to an existing structure. And I want you to hold that thought that trend that concept because I'm going to come back to it a little bit later when I talk about Future World Vision. Let's move on to water infrastructure. I think we're all familiar with the impact of aging infrastructure on our water supply. The ASC report card says that nearly 6 billion gallons of treated drinking water are lost per day due to leaky pipes, 6 billion gallons. That's nearly 15% of the US drinking water supply. And I think we're all familiar with what happened in Flint, Michigan. water from the Flint River was used instead of water from the Detroit water system. The water from the Flint River was more corrosive, and it leads to lead from the pipes into the water into the drinking water. When you go to Capitol Hill and talk to the legislators there, believe me, no one no one wants to have a Flint, Michigan happens in their state or their congressional district. And then there are watermain bursts due to old pipes. The report card says that there are more than 250,000 per year. When they occur, they can lead to significant damage and when they occur in major metropolitan cities, they can lead to major disruption. So, let's talk about some opportunities for improvement with FRP related to water we'll start with drinking water and wastewater they get a C minus and a D plus respectively. So FRP has been used to four pipes for drinking water. The important attributes here are corrosion resistant and durability. FRP pipes do not contain any lead and to be used with potable water they need to pass a test called NSF 61. FRP can also be used to repair leaky pipes. There is a technology known as cured in place pipe or CIPP. It is a trenchless repair technology where basically you insert a sock into the ground, fill it with resin allow the resin to cure and you form an impervious shell inside the existing pipe. This can also be done by taking preformed liners underneath the ground. FRP can also be used for wastewater infrastructure. This is a cartoon of a typical wastewater plant and there are many different places where FRP can be used in this plant. It can be used in the pipes; it can be used in the covers and the scrubbers and the ductwork and the baffles near the settling ponds. It can be used in the storage tanks use the whole the aggressive chemicals used to treat the water things like bleach, hydrochloric acid and sodium hydroxide. And it can be used in the stairways, the gratings, the handrails and the walkways throughout the facility. In all of these applications, you're taking advantage of the excellent corrosion resistance of FRP. Let's stay on the water theme and talk about dams, inland waterways and levees, they all get d grades in the report card. And here are some pictures that show how FRP can be used in inland waterways. It's used in locks in wicked Gates is used to protect bridges. And these FRP piles are used to support these navigation AIDS. In all of these applications, you're taking advantage of the excellent resistance of FRP to water. And we'll finish up with ports they get a B minus in the report card. FRP has been used in all kinds of waterfront and coastal applications. FRP piles have been used in these piers in this seawall in these dolphins at this ferry landing. And here is another example of a Fender in this case protecting a pier from impact damage. So, to come back to my take home message, I hope I've shown you very quickly that there is an extremely good fit, extremely good fit between FRP composites and our nation's infrastructure needs. Right now, I didn't have time to talk about all 17 categories, I talked about seven, two of those categories had c grades, four of those categories had D grades, so there is definitely room for improvement. And FRP can help get these grades up right now. So next, let's talk about the future. Now I want to connect FRP composites to the other document from ASCE. And that is their future World Vision. And that is exactly what it says it is ASCE vision of what cities of the future will look like. And you can get a lot of information and some very useful videos at this website here. And we're in a session called CW trending, and Future World Vision is all about megatrends and how they are going to impact cities of the future. So, there are five different scenarios, I'm going to talk briefly about two of them. The first is floating cities, which ASC predicts that we might begin to see the first floating cities around 2040. A little bit of history here. In October of 2019, I attended the ASCE annual meeting in Miami. I attended as a nonmember, but I quickly decided to join ASCE. What convinced me to join was the floating cities virtual reality exhibit floating cities as a part of Future World Vision. And here are two pictures from the conference. This is not me. But this is one of the attendees with the virtual reality goggles on, what you did was put the goggles on and go out to a floating city. And you could look all around and see the infrastructure above the city, the buildings above the city or above the water. And then you could look below the water and see the substructure of the city. This was by far, by far, the best virtual reality experience I have ever had. And if you ever have a chance to experience this, you should. It is truly amazing, extremely well done. And it got me really excited because I saw a very good fit between FRP and this vision of the future. So, a little bit about FRP. And, and trying to show you the tie between FRP and floating cities. So, I'm going to do that showing some pictures from ASCE videos and articles and also some real-world examples. First of all, you're talking about a floating city here. So, the most important thing is that it needs to be able to float. And so FRP is a perfect fit, because you want everything above the surface of the water to be lightweight. The buildings and the bridges. FRP is 1/5 the weight of steel, it is 30% lighter than concrete. So, if you want this thing to float, you want lightweight elements. And that is what FRP provides. If you look below the surface of the water, remember we're talking about coastal cities here like Miami and Singapore. They're going to be in corrosion or corrosive seawater, what you're going to want is corrosion resistant construction below the water and that is another place where FRP excels corrosion resistance, and then you're going to want resilient structures around the city. structures like sea walls and structures that can prevent damage from hurricanes and storm surge and sea level rise. And I've already shown you how FRP is used in things like sea walls and peers. So, if you look at these pictures, and you see what FRP is capable of, there's a very good fit between FRP and floating cities. Now, some of you might say, Yeah, but when are we going to see floating cities ASCE predicts that it'll be out in 2040. But there are other scenarios. But I want to talk about the other scenario, which is mega cities and smart cities, which is much more immediate and much closer to the present. So again, I'm going to be using pictures from ASCE articles, and real world examples to show the fit here. Remember, I talked about the lightweight addition of a pedestrian walkway to an existing bridge, lightweight addition to an existing structure, that's going to be a very important trend when it comes to mega cities. Because here's a picture where you're seeing some unmanned or manned vehicles, urban Air Mobility in mega cities, and you're going to need places for those vehicles to land. And FRP would be an excellent choice for the addition of lightweight heli ports to existing buildings. It may also be possible to add additional living and working space to existing buildings by adding these lightweight composite modules to the exterior of an existing building. Future world vision also talks about drone delivery, and prefabricated structures. And here's a picture of that came from an ASC article, which shows a drone delivering a girder to a job site. And when I saw that picture, I instantly thought of an FRP girder that has been developed and tested at the University of Maine and commercialized by an industrial partner. And that FRP girder is 70% lighter than a steel girder, which would make it much easier for this drone to deliver it to the job site. ASCE also predicts greater use of prefabricated structures. And here's something that's already happening with FRP. This is a composite foundation for a residential home. And it is assembled by bringing these prefabricated panels to the job site and assembling the basement in a fraction of the time that it takes to make a traditional poured concrete basement. And then lastly, FRP could have a very good fit in smart cities, where 5g will be important for communication. For 5g communication, you're going in mega cities, you're going to need many more antennas. And you're going to need materials that are transparent to RF radiation, high frequency short wavelength radiation, and FRP composites are transparent to RF radiation. So, they may be able to find widespread use in a mega city, and enable better communication between buildings, and within a building. And as an illustration of that this is an FRP light pole that is already in place in Europe. And it does not only serve as a light pole, it also serves as an antenna, because it is RF transparent. And this one here even has a charging station for small drones at the top. So lightweight, prefabricated, easy to install RF transparent. Again, there appears to be a very good fit between FRP. And this vision of mega cities and smart cities of the future. And really, when you think about it, that future is right now. So, I'm going to finish up where I started, that there is an extremely good fit between FRP composites and our nation's infrastructure needs both today, and in the future. You can use FRP to convert those C's and D’s into A's and B's today, and I've shown you how it fits with scenarios like mega cities and floating cities of the future. Many of the trends that I've talked about in my presentation Bode very well for the future of FRP. That concludes my presentation, and I look forward to the Q&A.
Jeff Sloan
All right, great. Thanks, Joe. We're going to turn it over now to Gareth Williams. And, Gareth, I'm going to let you take it away.
Gareth Williams
Yeah, thanks, Joe. Thanks, Joe, for a great presentation. Well, thanks everyone, for attending today. And it's a privilege to be able to present to everyone. So, Joe has given an excellent presentation and overview on the kind of huge range of opportunities for composites in infrastructure and construction. So, my focus either at the National composite center, we have a broad view. And our responsibility is to drive the use of composites into all sectors, all industrial sectors, and driving the latest technology, the design and manufacturing technologies to introduce and support those. So, we have a good really good view of the challenges across multiple sectors. So, what I'm going to focus on here is, if the case is so compelling for composites in construction and infrastructure, what's actually stopping the adoption of that technology in its widespread use? So again, more generally, why composites in construction? You know, why? Why do we actually want to look at that? So, there's kind of four primary drivers at the top that we focus on. So, one is around longer life, and low maintenance infrastructure. And Joe pointed to a number of those applications, particularly where we are exposed to more corrosive environments. And where you actually want to have infrastructure that you have more potentially, and conceivably more predictability around its degradation mechanisms. And you know, they like to put a longer usable life out of that asset. The other ones more efficient homes and buildings, with a potentially a reduced carbon impact. So, some of the thermal properties of composites can be really advantageous in the use of home buildings and can be really favorable from an embodied energy perspective, and the others low impact construction methods and materials. So, the generally the installation footprint of composite structures and some of the alternate methods that you can use to, you know, maybe as far reaching as the drones that Joe pointed to can become an option for composites, whereas with the kind of incumbent technologies in the sector, that's not necessarily possible. And the other is kind of a self-reinforcing opportunity here for modular offsite construction. And so that's another way of productizing, the use of composites in, in construction, which helps drive down the cost, which, as you'll see later, or reinforces that this can be a challenge with the adoption of composites. But they're just the I guess, more generically, there's the opportunity for reduced installation. So actually, completing some other kind of one part or one part lifts the installation time, under the reduce disruption to operations around a construction facility, particularly when you look at roadway infrastructure and things like that installing bridges, the disruption to that infrastructure can be minimized because it can be a much reduced installation footprint, the ability to combine form and function that really goes hand in hand with the opportunity for architectural impacts. So, you're not necessarily looking at a structural component, and then have your interesting features reinforced with cladding and other I guess nonstructural materials. With composites, you can actually combine both because they're manufacturing properties, which is really interesting to see some of the visions that architects have actually being able to come to reality when you select composites as a as a material choice. And also, that reinforcement that composites are not just for niche applications in small kind of minimal load bearing applications. They're used as examples worldwide of where composites have been used for performance at scale. So, what's stopping us to use it? As I say the value proposition is so compelling with composites? Why are they not just adopted, and many of you will recognize some of these challenges. So, the first four have identified is around knowledge. So, there's potentially limited knowledge within the sector. And those engineers that are civil engineers gone through civil engineering training. And having that limited access to knowledge to be able to identify concepts as a viable opportunity, and also that the tenders the procurement processes in the sector can sometimes be prohibitive. Not necessarily intentionally, but people writing the tenders might not have the knowledge base to be able to open up maybe a performance criteria, where competence can be a not an opportunity, an option for the solution. standards. That may not be the relevant standards that people can design to for different applications of composites, skills and workforce, widespread skills and training not necessarily prevalent. It doesn't necessarily feature heavily in the curriculum for civil engineering and some of the associated Skills for construction infrastructure and the supply chains as a, an aggregation of all of that the supply chains are not generally equipped to support the introduction of these innovative technologies. And also the incentives aren't necessarily there for those supply chains to innovate in response to the available tenders. The other four cost. So typically, and this is a kind of a self-defeating issue, the high, low uptake of composites generally makes the introduction of a concept product less competitive from a cost perspective. But, as you'd see more uptake of composites use, you can start to commoditize the production, particularly manufacturing techniques, such as protrusion come into play in construction, and can be a good way of commoditizing, that production and the introduction of those materials. RHS sections in composites for example, and sustainability. So, I guess historically composites do have an end-of-life challenge. That's more of an acceptable challenge, you feel, for example, doubling the operational life of an asset. But there's an opportunity there to start to develop circular economy approaches, and with the NCC, we're pushing right at the forefront of sustainability issues and try to address that challenge, so that it doesn't become a barrier or continue to be a barrier to entry in multiple markets for the use of composites, the market, how the construction and infrastructure market is created, to the benefits owners really aligned with the risk owners. So, in terms of supply chain development, introduction of new and innovative technology, if the risks it's somewhere, or the benefits of using that new technology somewhere else, then you know, you've got to break down in the system. So, we need to make sure that the benefits and the risk owners are incentivized in the right way to encourage innovation and alternative solutions, and data. So, people may have the knowledge, they may have access to the standards, but they don't have the relevant data, for example, foreign toxicity, performance in accordance with the standards and codes relevant for that sector, then there will still be reluctant to an inability to access those materials. Otherwise, you will need to go back to square one and produce that data those datasets are on a case-by-case basis, which can be time and costly. So, I'm going to draw out three focus points. To conclude the presentation. The first one is around sustainability. And as I said, the national composite center, we're working with our membership base across multiple sectors, to really take what's historically a linear lifecycle for composites and make it more circular. So, at the end of life, we have more options to either repair, reuse, recycle or return that material back to war. So, recover the route in particular, the really useful parts, the high value parts, which is the fiber, and also do something very useful with the polymer chemistry that forms the matrix. But what we see is the potential for a really interesting waterfall cascade, where you typically take a high performance, low volume material, you recycle it, and generally you degrade the performance of that material that fiber somewhat in the recycling process. But the opportunity to then reenter another stage in another industry, another part of the value chain as a really useful products in create that supply and demand. And ultimately ending up in your what you would typically recognize compared to some of the high-performance aerospace structures or low performance, high volume application, and then you've got a really good model there to a circular model for continued reuse of those kinds of materials.
The other one is a market; I think this is really important. And you see this across multiple sectors where the value proposition for changing into a new material, companies might like the principle and the benefits that Joe's outlined and great examples of where they've been used. But if the supply chain is not really constructed in the right way, whether the standards are actually, sorry that the tenders, the procurement processes don't incentivize or land the right risks and benefits with the right owners, then it it's self-defeating. So, there's no incentive to change. And the benefits that we talked about in terms of composites, the asset owners are very interested in those. But the, I guess the installation, part of the supply chain, maybe carries the risk of taking on that new technology. And so, we have to make sure that the supply chain if we want to encourage that chain change that we look at new ways to incentivize the right behavior and incentivize innovation. And looking at the way in particular, that that doesn't become restricted or prohibited by closed specifications and tenders, where you know, metal solutions or the incumbent material is the only viable solution because it's closed down by the tendering process. And lastly, you know, the industry is not dealing with these challenges in isolation, one of the things that we've received because we serve every sector, and we're introducing growth in introducing composites in great sectors where they're not used to using composite technology like construction and infrastructure, like energy, we actually work across the board. And we can recognize the challenges that multiple sectors face. And so, a collaborative approach to addressing some of these challenges can reduce the burden on other industries that are maybe not as mature in their adoption of those technologies can help can learn from other information and knowledge that's generated in parallel sectors. So that's what we try and foster. But at the top level, is the challenge of creating zero carbon, generating zero waste, and creating zero harm in our projects. And across multiple sectors, serviceability energy construction, infrastructure, medical health care, food and agriculture, some of the recognized industrial sectors, then if we look at the barriers to entry that have outlined, the only one that doesn't, obviously, isn't a carbon copy, potentially across those sectors is the market construct. And that's very different depending on each market. But some of the similar challenges, how do you construct a market to incentivize the behaviors, the adoption of new technology that you want to stimulate? But when you look at the knowledge, standards, skills, and workforce supply chain cost sustainability data, there's aggregated demand for those. And so, a cross sectorial approach to some of these are knowledge sharing between key sectors that have overcome some of these challenges, and have used composites widespread, widespread adoption, and ahead of overcome that challenge of addressing those barriers to entry. We're well positioned, you know, collectively as a complex community to help to bridge that. And so, no sector really is what I'd say an island in solving these challenges. And there's always someone that has maybe not addressed the same challenge. But we can cross pollinate technology, we can cross pollinate knowledge and learning. And that's really what we should be doing to help accelerate TRL scales for technology and new sectors. And that's the end of my presentation. Thank you very much for listening to me.
Jeff Sloan
Alright, great. Thanks, Gareth. And we'll bring Joe back in. I appreciate both of you for those presentations. So, before we get to attendee questions, which we have a few have already. I have a question. One question. Well, two questions for each of you. So, I'm going to ask you first Joe and, Gareth, I'd like to answer the same question. And attendees, if you have questions, go ahead and start putting them in as well. We'll, we'll get to those here in a second. My first question is, Joe Gareth referenced the fact that the first cost for composites are relatively high. There's also sustainability story to tell, and that maybe offsets the cost. I'm wondering what each of you sees happening in the infrastructure community right now is, is that first cost argument still holding meaning? Is that still the primary concern? Or is the sustainability argument starting to win over and prove the viability of composites?
Joe Fox
So, I'll try to answer this first. With respect to first costs, I think it's fair to say that in most instances, using FRP, for example, in place of steel or concrete, you are going to have a higher first cost. But I've been given a webinar to various ASCE chapters. And one of the things that I highlight is a lifecycle cost analysis for the halls River Bridge in Florida. It's been conducted by the Florida Department of Transportation in the University of Miami. And they clearly show that if you factor in the lifecycle costs where you factor in the lower maintenance costs, the lower repair costs, the lower replacement costs of FRP. That over the life cycle, FRP is a winner. There are also some examples, particularly from advanced infrastructure technologies, which is has been very active in putting bridges throughout New England, mostly in the state of Maine, that they have shown that the first cost of installing some of these bridges with FRP is lower than the traditional concrete solutions. And so when you look at lifecycle cost, I'm also involved with ACMA’s efforts to get legislation on Capitol Hill that spurred the use of composites. And a lot of that legislation is really asking the State Departments of transportation to focus not just on first costs, but on lifecycle costs. Because ultimately, you're going to spend more money if you have to do a lot of maintenance, repair and replacement.
Jeff Sloan
Gareth, what do you see?
Gareth Williams
Yeah, I've reinforced that, I think, generally, when you have a compelling challenge or driver, where composites have a really compelling case, like you've got an extremely corrosive environment, or you're, you know, restricted in terms of your lifting capacity or something like that, then first costs can be overcome by you know, it, it might, it becomes a lot more compelling when you have that ultimate driver work on some of the benefits of composites override the cost. But unreinforced Yeah, what Joe said, were the words that we get people to look at is the whole life cost. So, it yes, sometimes the upfront costs, until it, you know, gets commoditized, or there's widespread adoption of composites in construction and infrastructure, you need to look at the whole life costs. And that's not unique to construction infrastructure, same energy and other industries have already overcome that challenge and do consider the whole life costs. But that's where I come back to the market, construct and construct an infrastructure. Because if you if the if the organization making the decision on the procurement exercise, doesn't care about the whole life cost, because they won't, they won't have the asset, they won't maintain the asset, they won't solve the downstream problems, then they still won't be incentivized, even from a whole life cost perspective, because they're part of the share is the upfront cost and carrying that risk. So, I think that needs to be overcome. But one of the other things on the other side is, is the opportunity to do the right thing. And what we're hearing from a number of companies that were working in construction and infrastructure is the real interest in using recycled materials from composites. So, for example, we've got a key initiative called suspend that we've launched, which is working with the wind industry to solve the challenge around recycling for wind turbine blades. And what we're doing in that program, really interesting is trying to create that supply and demand side of the market so that we have companies in construction and infrastructure that are really motivated to use recycled materials, because they want to do the right thing. And they want to provide an outlet for those solutions, with the cost with the suppliers, if you like that have a problem in their in their recycling challenge. So, if you can connect the two, you create a good market for recycling. And it also opens up a good additional use for composites in construction infrastructure, because of the reduced co2 footprint and the good story that comes with, you know, using recycled materials that would otherwise you know, potentially not have an application.
Joe Fox
Jeff, I wanted to just add a little bit more about sustainability. But I focus mostly on lifecycle costs and they're not completely disconnected. But in terms of sustainability. When you use FRP. In place of traditional materials of construction, there can be energy savings, and transportation savings. So, you've got lightweight materials. So, it costs less to get the materials to the job site. You need less equipment at the job site in terms of cranes and heavy equipment. All that translates into labor savings and energy savings. When it comes to emissions. One of the biggest creators of carbon dioxide is the production of cement. So, whenever you replace concrete with FRP, you are lowering emissions. Whenever you use FRP rebar to replace steel rebar to replace concrete and make it last longer. You are lowering emissions. So FRP has a very good sustainability story to tell.
Jeff Sloan
Okay. Alright, so next question. I'll start with you, Gareth. Good. Joe just mentioned rebar. You know, recently in Miami, we had a collapse, a tragic collapse of an apartment building. And I don't want to ask any questions about that. But this is an example potentially, we still don't know fully because of that collapse. But if in fact, there was a problem with the concrete and or the rebar. It points to maybe a bigger issue of building construction over the last 50 to 60 years, at least in the US and perhaps around the world. And I'm wondering if there are lessons here what this might and tell us about the future of materials use. And again, I'm not looking for answers about what happened in Miami, but maybe just give me your thoughts about what that tells us about. composites company Let's use in infrastructure and in future buildings and structures. I'll start with you, Gareth.
Gareth Williams
Yeah, I think the first thing to say is, you know, it's really sad, and no one no wants to hear about loss of life to be associated with a collapse of an engineering structure. And that's, that's sad. And my heart goes out to anyone that was, you know, affected by that. I think on the engineering side of it, it always amazes me in any environment, and particularly, if you can come away from that, and look at the salt water environment, you know, why you would ever want to put steel, close to a salt water environment, particularly in the splash zone, when you know, you're completely reliant on, you know, a protective coating, etc, to prevent, you know, rapid corrosion of that structure. And industries can accept that degradation and those risks associated with that technology, but as a, as a competing technology and composites where you don't have any of those issues associated with corrosion. And there's a real reluctance. So, it's, I hate to use the phrase, but it's almost the better, the better the devil, you know. So, there's a lot of historic information, generally, some of those corrosive behaviors are predictable and understood, but every now and then it you know, it catches people out. Because, you know, the engineering environments complex, you can't allow for everything, there are assumptions made, you know, there are load factors applied to things. So it is a challenge, but I think, you know, real critical events like that, you know, that you can work for and against the change of new materials, and one side, it can make people really risk averse, and say, Well, you know, I'm going to go back to what I know, and reinforce with what I know, I don't want to add another complexity and additional risks. But then it can also drive, you know, I guess, the right people to be looking at and going by, that's got to be a better way of doing this. And whether that's looking at existing infrastructure and saying, what do we need to put in to address these challenges? That when they understand, you know, what's actually happening? What are the early signs, what are the technologies we've got available, and that kind of retrofit repair for composites are really, really, you know, conformable, when really, you know, from a thing that you can kind of mold with your hands that can, you know, beat the strength of steel, it's amazing, you know, to fit in the kind of spaces that you might need to fit for retrofit applications, which so there's a particular niche market there, in terms of, I guess, new construction techniques, we'll come back to some of the barriers to entry, we still need to address the understanding of standard certification requirements for composites in those applications, and we need access to data that will weigh with pushing, it is more around the, moving into industry 4.0. So digital technologies, so moving into the digital design space, digital certification, and they're looking rather than saying, you know, we haven't got 50 years of operational experience under these conditions, we can validate traditional methods, what are predictable performance is and then use things like structural health monitoring, and other techniques that composites can bring in terms of their monthly functionality to actually monitor them, and pair that back with a, you know, potentially a live digital twin. So, you are constantly up to date with what assumptions that we made? And what's the real-life data? How is that panning out compared to what we expected. But there's a, you know, there's quite a way to go to get that. But that that's kind of the vision of the future, for what composites can help bring into that sector as well.
Jeff Sloan
Alright, any thoughts Joe?
Joe Fox
So, I'm not a forensic engineer. And it certainly is going to be a challenge for those folks to figure out why that building collapse why that tragedy occurred. But I will say one thing, it happened in Florida. And when I was talking about bridges, I mentioned that Florida is one of the most active states for using FRP and FRP. rebar. And the reason they do is because they are surrounded by the ocean, and they have a very corrosive environment. So, the state of Florida has been a leader in the use of FRP, rebar, and FRP elements of bridges, exactly because of corrosion resistance. And when you look at the pictures of some of the pictures I've seen of that building, before it collapsed, you see corroded rebar, and spalled concrete.
Jeff Sloan
Okay. Well, let's get to some of the questions from our audience. And we have quite a few. So, let's try to get through as many as we can. Maybe we'll start with you, Joe here. Which FRP composite applications within infrastructure do you see as having the best growth potential over the next five to 10 years and what might drive that growth?
Joe Fox
So, I think that the whole resiliency push, okay, and, and that and the climate change and the sea level rise, I think you’re going to see greater use of things like sea walls, and FRP utility poles that are able to withstand things like hurricanes and storm surge, and tornadoes, and forest fires. I think that's going to be an area where you're going to see a lot of growth. I think, based on the last question that I think you're also going to see a lot of growth of FRP rebar, I think it will be in the States, where you're, you're dealing with an ocean close by a corrosive situation. But even in northern states, where you're using deicing chemicals to get rid of ice and snow, you're going to see more and more use of FRP rebar. And then I think that RF transparency is going to lead to opportunities related to communication.
Jeff Sloan
Gareth, what opportunities do you see?
Gareth Williams
Yeah, I mean, echoing what Joe said, I think coming back to I think, was one of the first questions you asked, I think you're still going to have the early step applications that adopters of the technologies where there's a very compelling value proposition. And business case for the use in corrosive environments, in environments where you need lightweight performance, whether that's in the construction phase or in the operational phase, I think bridges are a very good application for you know, even from the fact you can, you can potentially manufacture more site and drop them in place, you know, in a one part lift, which causes much less disruption to traffic flow or rail activity in those applications. I think the need to get it, I think rebar is a good commodity, a commodity application, where you know, can you just make, you can make heaps of rebar out of composites, and see widespread use and adoption, I think the other thing is the need to move into those kinds of commoditized sections. And there are companies around the world, for example, doing, you know, pultruded sections, really high-performance sections, whether they be thermostat or thermoplastic. That can be replaced, like for like, steel girders, you know, the steel sections that are kind of the foundation structures of any, you know, large building, the only barrier, as I see is really the knowledge of the industry or the comfort with the industry to lean on composite technology to replace technologies that are so well known and well understood, it's very different, because you know, you can't go and weld things together in the same way, there are different joining techniques. So again, you've got the challenge with the current supply chain could not necessarily, you know, accept the switch with their current skill set. So, you have to address that. But I think if you address that, or if you make the joining techniques, some of the challenges that the supply chain would have and make it as easy as possible for the supply chain to take those technologies. I think there's much less resistance than to use commoditize sections for structural I haven't, you know, the main stays yet structural sections of buildings on potentially there's no limit. Because it's a start, as you start seeing the adoption of the technology and the widespread use, it drives the cost down and therefore people get and you get more original data, that you kind of, you've got to break that seal, if you like in terms of the adoption.
Jeff Sloan
Alright. Gareth I'll put this next one to you with so much emphasis on plastics currently source and fossil fuels. How do the greenhouse gas emissions from making FRP factor into the sustainability story?
Gareth Williams
Yeah, and I think I think Joe pointed to the co2 footprint, I think there are various studies out there showing that in a on a like for like basis, where you put FRP structures in either replacement for steel or concrete, you win from a co2 emissions perspective, petroleum derived products that you know, currently, you know, do go into the polymer systems and carbon fiber as people understand, but there are technologies that you know, being in the market available in terms of more naturally derived resin systems, in terms of other fibers or even lower co2 footprint fibers. So, you know, you kind of got a double step there for the industry to start influencing the drivers or what they want to see from the performance the material from either a co2 or a cost perspective, you have to get the industry, you know, using the material and driving the market to push those technologies in the direction they want to see. So, you know, we're involved in that from a sustainability perspective LCA is lifecycle costs and co2 comes into that as well.
Jeff Sloan
Okay. Joe, next question for you. This is from Marion, Marin Elliot, is the ASCE manual and repairs available on their website? How do you determine best practice? For what materials to use for repair? And maybe more broadly, do you have suggestions on how to get involved with companies, organizations that are testing potential infrastructure solutions? So maybe there's a lot of questions there. But if somebody wants to get more involved in more and more, what's the best path forward?
Joe Fox
Right. So, I'll start there, because I am a member of IACMI, which is the Institute for Advanced composites manufacturing innovation. It is a manufacturing USA Institute has over 100 Industrial members more than a dozen universities to federal laboratories. And it's very much involved with testing of composites and development of new products. So, IACMI www.iacme.org. With respect to the manual, the manual that I referred to is actually an AASHTO manual. I believe it is available on their website. I don't think it's free. And then, what was the third question, Jeff, there was a third one.
Jeff Sloan
Yeah, best practice
Joe Fox
Okay. So, um, I was looking at some of the other questions, as Gareth was answering and someone asked, why do things take so long? Why is the pace so glacial the development of codes and getting everyone to agree on standards and specifications can be a glacial process, there is one LRFD for a load resistance factor design for pultruded structures that ASC and ACM the American composite Manufacturers Association have been working on for more than a decade, there was a pre standard issued in 2010. The standard itself is supposed to come out this year, I think one of the things that needs to happen is faster approval, faster of agreement on these new codes. Because design engineers want to have standards and specifications. And there are already a lot out there. ACMA has a very good listing of the standards and specifications that are available on their website, including ones from the American Concrete Institute. And so, I would encourage going to the ACMA a website to learn about a lot of the standards and specifications that already exist.
Jeff Sloan
Gareth, I'm going to throw this one to you. See what you can answer this however you like, but you mentioned end of life. So, this is from Michael Connelly end of life is always a challenge for composites producing recyclable or depolymerizable resin system is typically counter to the durability benefit those composite systems typically bring. Can you share examples of resin systems today that are both durable in use but can be easily reduced to monomers for secondary use? Fairly technical question, but there's an end-of-life component there that, you know, is a challenge for sure. I'm just wanting to get your thoughts on that.
Joe Fox
Gareth, if you need help with that one, I can help with that one.
Gareth Williams
Yeah, I will definitely reach across to Joe.
Joe Fox
That’s the chemist in me.
Gareth Williams
Yeah, I've left some of those details behind in my career
Joe Fox
So let me let me just jump in and say that, you know, end of life is a challenge, as was phrased in the question, you know, you've got materials that are built to last for decades, and then you want them to come apart quickly at the end. Okay. Big dichotomy. Okay. But there's a lot of work going right now on recycling of composites and end of life of many many different solutions are being pursued. And both with thermoset composites and with thermoplastic composites, and one specific thermal plastic, which is I think, interesting is the Elium resin from Arkema. it is a mfactrelate based polymer that forms a thermoplastic can be used in rebar can be used in other applications for composites and it is recyclable. thermoplastics are in general, easier to recycle than thermo sets. And so, Elium from Arkema is one that I would highlight
Joe Fox
I think I just reinforced that, some of the technologies used to break down because you start with a product, you generally try not to degrade during Operation form. So, you have to introduce some other stimulus in the environment to then break that down. And generally, that will be heat in the form of direct heat, or some of the technologies, we're working with the superheated steam, for example, where you do start to break down the polymer matrix, and then you can recover the fiber, the fiber is generally the bit you're looking for. And because that's the big value add, however, the resin is another value proposition in there, because you don't want to end up with something else, you've just got to dispose of. So, breaking those down into its chemical constituents that read reenter the value chain as a new chemical is something we're definitely looking at. Because there's, you know that companies will want to do the right thing to a certain extent. But what we're trying to create is a is a market for recycling. So, you have a customer that will want the degraded polymer, or the recycled polymer and its constituent chemicals, whatever that might be, depending on the process. There's a company that we're doing some great work with not directly involved in this project. They're in our software project called Vestas and may or may not see in some of the articles in the programs called seetec. But they've developed some technology with some of the Danish universities to, to break down a thermoplastic. polymer sorry, thermoset polymer, and being able to break it down into its constituents to then make it into something reusable afterwards. So, I would say it's not been a massive driver for the last, you know, 30-50 years of composites, to be honest. So, I think, you know, one of the challenges now is to accelerate that activity, because it's very high on the agenda for everyone using composites. And you know, people are asking the questions, what the who are not using composites is, you know, am I going to end up with a sustainability challenge? If I start with composites and the messages, your three-life sustainability is going to be markedly improved with composites. And we will address we're working now to address the end of life. But when you're talking civil infrastructure projects, you know, hopefully, we're talking, you know, 50-100 years plus of usable life, you know, if you if you can use the composites in those correct applications. So, I think that's a real benefit from even from a sustainability perspective, because you don't have to, you have to repeat the infrastructure manufacturing installation twice, for example, you know, long life on those assets.
Jeff Sloan
And I want to echo what Joe just said about the argument material, the Elium, it's part of a larger family of materials, what we call reprocessed, reprocessed, visible epoxies, are we processable thermo sets that is their materials that cure and crosslink as a thermal set, that they can then be reprocessed, in softened and reformed like a thermoplastic. There are several companies out there that making polymers like that right now. And you can go to the CW website and just search reprocessable epoxies or repressible, thermosets. You'll find out more on that. Alright, we're near the top of the hour. So we've got one more question. And I want to at least recognize the question, I think we're going to have to answer this question offline. But if either of you has examples, to address this question, I think it'd be helpful. So, the basic question is, who are some of the key manufacturers in these infrastructure of these infrastructure applications or markets, so I'm going to throw one out just to get started, there's a company in Ohio, in the US called composites advantage. Well known for making bridge and marine structures from composites do a really good job. We've done a couple stories of him. So, I'm going to start with that one. But if either of you has examples of companies that you know, are active in this market, that might be a good resource for people. So, Joe, do you have any?
Joe Fox
Sure. So, you mentioned composite advantage. And that is one I would mention, and they are actually part of what's called the creative composites group. And so, within that group, there are other companies that also provide infrastructure products. So creative pultrusion as part of the creative composites group, and they make some of the pilings that I showed, if, if Jeff, if there's a way that you can distribute the presentations, you may have noticed I went very fast, you may have noticed that in many of the photographs, I actually acknowledged the company that provided that part. Right. And so, and then one other one that I'll just touch upon in terms of FRP, rebar, Owens Corning, there are many smaller rebar manufacturers, but Owens Corning is a producer of FRP rebar.
Jeff Sloan
Okay, thanks, Gareth. Any thoughts?
Gareth Williams
Yeah, I mean that there are a huge number of companies. And I probably I won't, I don't want to do a disservice to any companies by not mentioning them to be honest. But there's a couple of left afield from locations that you wouldn't necessarily expect to explore. So premier composites in Dubai, for example, that there are some astounding structures that that that company done, including, you know, Apple roof, made of CFRP in in Cupertino. Another really interesting one of, you know, have managed to put projects in, they've got manufacturing footprint in the US is a company that I knew from my time in Australia called Wagner's composites, and they do pultruded sections, and they, some of the bridges, actually, J that you might have referenced, have been some of the bridges that they've been contracted to do. And I think this is a really interesting piece, you know, because of the lightweight nature of composites, a company in Australia can win a tender for a bridge in the States, on you know, in a competitive pricing market, because of the benefits that you know, competent, bring that company, they can put it into a container, they can ship it out and reduce installation costs on site. So, I think the, the opportunity for composites and the benefits that brings, you know, companies that are willing to think outside the box on it, I think he's
Jeff Sloan
great. Right? Well, Gareth, and Joe, we are at the top of the hour, we do have a few questions we didn't get to. So, what we're going to do is aggregate all the questions also elicit answers from Gareth and Joe put those all into a document and send those out to all of our attendees. I'll also provide links to your presentations, assuming you are both comfortable sharing those. And then a few into the chat contact information for Joe and Gareth, their email addresses. So, if you have questions that you want to direct specifically at either Gareth or Joe, you should feel free to do that. But this is great information. I appreciate both of you for coming today and for presenting. And I appreciate our attendees as well for tuning in and providing such good questions. So, Gareth and Joe, thanks again for participating in CW Trending.
Gareth Williams
Thank you.
Joe Fox
Thank you, Jeff. Everyone. Thanks, Gary.
Jeff Sloan
Thanks. Alright, and that brings us to the end. Thanks, everybody for tuning in. And join us again next month and keep an eye on your email for the next announcement for CW Trending and have a good day everybody. Bye
Gareth Williams
bye.
Related Content
Hexagon Purus opens new U.S. facility to manufacture composite hydrogen tanks
CW attends the opening of Westminster, Maryland, site and shares the company’s history, vision and leading role in H2 storage systems.
Read MoreInfinite Composites: Type V tanks for space, hydrogen, automotive and more
After a decade of proving its linerless, weight-saving composite tanks with NASA and more than 30 aerospace companies, this CryoSphere pioneer is scaling for growth in commercial space and sustainable transportation on Earth.
Read MoreCollins Aerospace to lead COCOLIH2T project
Project for thermoplastic composite liquid hydrogen tanks aims for two demonstrators and TRL 4 by 2025.
Read MoreMingYang reveals 18-MW offshore wind turbine model with 140-meter-long blades
The Chinese wind turbine manufacturer surpasses its 16-MW platform, optimizes wind farm construction costs for 1-GW wind farms.
Read MoreRead Next
“Structured air” TPS safeguards composite structures
Powered by an 85% air/15% pure polyimide aerogel, Blueshift’s novel material system protects structures during transient thermal events from -200°C to beyond 2400°C for rockets, battery boxes and more.
Read MoreAll-recycled, needle-punched nonwoven CFRP slashes carbon footprint of Formula 2 seat
Dallara and Tenowo collaborate to produce a race-ready Formula 2 seat using recycled carbon fiber, reducing CO2 emissions by 97.5% compared to virgin materials.
Read MoreDeveloping bonded composite repair for ships, offshore units
Bureau Veritas and industry partners issue guidelines and pave the way for certification via StrengthBond Offshore project.
Read More