More on Spanish composites: Solution providers
My pre-JEC Europe 2016 trip through Spain yielded much fodder for future editorial content, and proved to me that the country’s composites sector is brimming with innovation.
Share

This weathered steel sculpture by Carlos Ciriza stands at the entrance to the MTorres facility at Torres de Elorz, Spain, and embodies industrial innovation and strength, says the company.
My pre-JEC Europe 2016 trip through Spain yielded much fodder for future editorial content, and proved to me that the country’s composites sector is brimming with innovation. I spent three days on a whirlwind tour of Tier 2 carbon composites fabricator Carbures (here’s a link to my previous blog that I wrote during that trip: http://www.compositesworld.com/blog/post/spanish-composites-growth-trajectory). The full article, which describes the three different plants that I visited, will be published in the upcoming July 2016 issue of CW magazine.
And, as I mentioned in that blog, I also visited industrial process automation supplier MTorres (Torres de Elorz, Spain) near Pamplona. That was also an eye-opener for me. The range of automated equipment solutions they design and produce, to manufacture both composites and metals in aerosopace, wind energy and paper converting, is impressive. And, the company is involved in some big, and very interesting, new projects, that we can’t report on, yet. I am completing an article about a Spanish aerospace demonstration project being carried out at the FIDAMC research center near Illescas, which involves manufacture of a thermoplastic wing skin via automated fiber placement, slated for test flight in 2020. MTorres is a project partner and the equipment supplier; that article will also be published in the July 2016 issue as a Work in Progress.
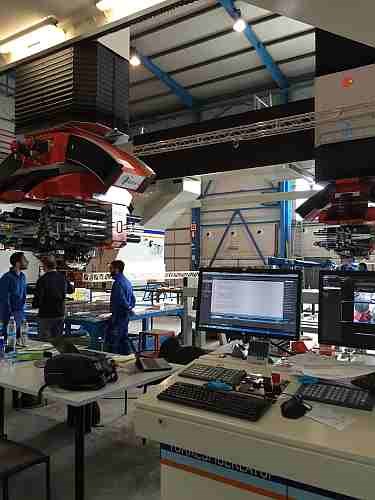
Workers at MTorres are involved with assembly of an automated fiber placement (AFP) head.
As it turns out, MTorres is not far from the Basque country, and as I passed through that area on my way to France, through San Sebastian, I was very close to the center of Spanish machine tool activity and the Mondragon Corporation (Mondragón-Guipuzcoa, Spain). Located within the Basque region, Mondragon Corp. is the tenth largest industrial group in Spain, and has more than 70,000 employees worldwide. Uniquely, it is comprised of 260 “bodies” or separate companies, some of which are well-known machine producers, that are bound together in a cooperative management system, dedicated to fair remuneration and participatory management. At least two Mondragon Group entities in that region are involved in composites. The first, DANOBAT GROUP (Elgoibar, Spain) is one that CW has been tracking for several years, because of its development of an automated machine head that lays down dry, woven or multiaxial fabrics, at widths up to 2m, very rapidly (up to 110m/minute), for subsequent infusion processes. I caught up to DANOBAT’s Asier Huertas, director of the composites division, at the JEC Europe event (here’s a link to the JEC report: http://www.compositesworld.com/articles/jec-world-2016-the-full-report; DANOBAT’s story is about one-third of the way down). I plan to keep an eye on DANOBAT’s automated system, targeted to the aeronautic sector, as its business develops.
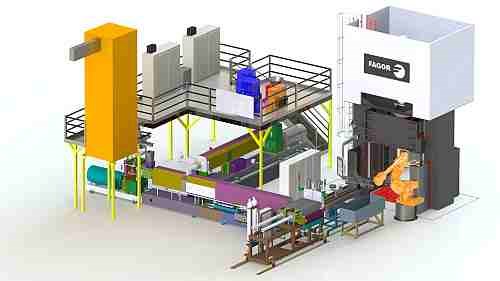
FAGOR ARRASATE's Direct Long Fiber Thermoplastic processing line
The second Mondragon composites entity, FAGOR ARRASATE (Mondragón, Spain), contacted me after the trip, to say I should have stopped at their facility during my time in Spain. FAGOR ARRASATE is one of the founding members of the Mondragon Corp., with six facilities worldwide. It designs and manufactures mechanical and hydraulic presses, as well as complete automated turnkey manufacturing solutions for both metalworking and composites. Composite equipment has been produced since 1985, by a predecessor company ONAPRES, which was absorbed by Fagor Arrasate. With a focus on the automotive sector since 2010, the company has produced sheet molding compound (SMC) presses and production lines, with advanced process control systems that reduce energy consumption, and allow in-mold coating capability, says Estibalitz Arregi, composites business unit manager. It also offers presses and systems for processing glass mat thermoplastics (GMT) and lightweight reinforced thermoplastics; these lines are equipped with needle-gripping pick and place robots optimized for quick loading and unloading, with customizable options. Direct Long-Fiber Thermoplastic (DLFT) lines are also available, fully automated, with customized extruder depending on the customer’s needs.
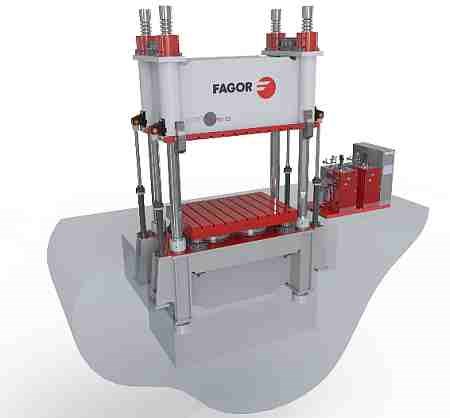
Fagor Arrasate's latest HCL press for high-speed molding of composites.
FAGOR ARRASATE’s latest composite system is an “HCL” press system, for several processes, including resin transfer molding (RTM), high-pressure RTM (HP-RTM), wet compression molding and handling of “organosheet” or thermoplastic prepreg materials. Arregi points out that the HCL system was developed for composite automotive parts, and features high closing speed, fast pressure build up time, integrated parallelism control, and more. “As we’ve done in our metal-stamping business, we develop turn-key solutions and automation for composite lines in order to get higher productivity and reduced cost of the final part, which is a key factor for increasing the use of these materials,” says Arregi. Customers include automotive Tier 1s that manufacture truck parts, agricultural vehicle parts and automotive semi-structural parts. The company's composite equipment Web site is here: http://www.fagorarrasate.com/product/90/26/composites-forming-lines.aspx. We’re keeping an eye on this company as well.
Related Content
STUNNING project completes lower half of MFFD
Clean Sky project has delivered the 8 × 4 meter welded aerostructure component, aided by advanced thermoplastic composite technologies and smart robotics.
Read MorePlant tour: Airbus, Illescas, Spain
Airbus’ Illescas facility, featuring highly automated composites processes for the A350 lower wing cover and one-piece Section 19 fuselage barrels, works toward production ramp-ups and next-generation aircraft.
Read MoreCombining multifunctional thermoplastic composites, additive manufacturing for next-gen airframe structures
The DOMMINIO project combines AFP with 3D printed gyroid cores, embedded SHM sensors and smart materials for induction-driven disassembly of parts at end of life.
Read MoreAirbus video highlights RACER compound helicopter first flight
Launched as part of a Clean Sky 2 program, a compound design — rotor, split fixed-wing, propulsive propellers — uses composites to cut fuel consumption and emissions by 20%.
Read MoreRead Next
Developing bonded composite repair for ships, offshore units
Bureau Veritas and industry partners issue guidelines and pave the way for certification via StrengthBond Offshore project.
Read MoreAll-recycled, needle-punched nonwoven CFRP slashes carbon footprint of Formula 2 seat
Dallara and Tenowo collaborate to produce a race-ready Formula 2 seat using recycled carbon fiber, reducing CO2 emissions by 97.5% compared to virgin materials.
Read MorePlant tour: Daher Shap’in TechCenter and composites production plant, Saint-Aignan-de-Grandlieu, France
Co-located R&D and production advance OOA thermosets, thermoplastics, welding, recycling and digital technologies for faster processing and certification of lighter, more sustainable composites.
Read More