Cutting and stacking cell from Schmidt & Heinzmann earns ThinKing Award
Lightweight innovation award emphasizes the system’s successful interplay between hardware and software for flexible and precise preform cutting and stacking.
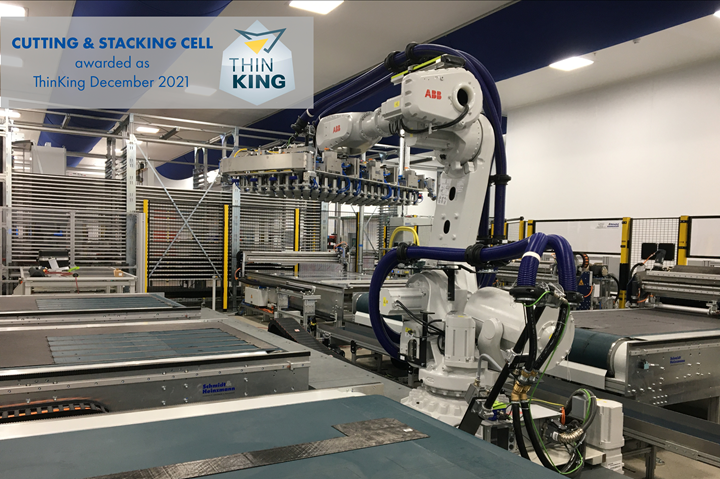
Photo Credit: Schmidt & Heinzmann
It was announced on Dec. 1 that Schmidt & Heinzmann’s (S&H, Bruchsal, Germany) cutting and stacking center has received the ThinKing Award for December from Landesagentur für Leichtbau (State Agency for Lightweight Design). The business and science development company acts as a platform for innovative products and services in the field of lightweight design.
According to S&H, its solution, with the help of coordinated software and hardware, cuts dry fiber fabric and precisely stacks them. If necessary, the system can react flexibly, such as recalculating the program sequence. This combination of flexibility and precision, combined with economic efficiency, is said to enable the production of cost-efficient, lightweight components for a wide variety of industries. it can also be used by a variety of companies.
“We are delighted that we have already received the second award for innovations with the ThinKing Award this year,” says CEO Matthias Feil. In the first half of 2021, the company was among the finalists at the JEC Award with its innovative SMC semi-finished product line “Cube” and also received the Top 100 Innovation award.
The cell itself, consisting of several cutting tables, one robot with a gripper module and a scales and conveyor belt, cuts textiles from glass, carbon or natural fibers and stacks them into precise stacks. Afterwards the stack is transferred to the next process step for further processing — usually a press for resin transfer molding (RTM).
“These process steps are still carried out manually in many companies,” explains Dr. Bücheler, director, process engineering “Our system does this in a cycle-optimized manner and, thanks to its generic approach, can even produce different stacks at the same time.”
Intelligent nesting creates the optimum cutting plan for the cuts to be produced, S&H says, for efficient use of the material, thus reducing material waste. Moreover, when using several materials within a stack, S&H relies on its Multiple Cutter Concept (using a polygon knife, round knife, ultrasonic knife, etc.), meaning there is one cutter for each material, shortening cycle time and increasing process reliability.
One highlight of the cell is the control system. An algorithm determines the optimal sequences for the production process, which can also be designed to optimize cycle time and material use. Cutting, stacking and handling are permanently monitored by the integrated production planner and adjusted according to the defined parameters. The intelligent assistant also keeps an eye on the times for nesting or the remaining supply of fiber fabric.
Ultimately, S&H contends that the manufacturing costs for lightweight components can be significantly reduced by using this cutting and stacking system; compared to semi-automatic production, up to 75% of personnel costs can be saved. In addition, resources are conserved via optimal material, which also reduces materials cost.
Related Content
-
Norco invests in CNC, kit cutting capability expansion
Transition from internal to external demand over the last few years has evolved Norco’s machining and composite kit cutting equipment, and now includes material outsourcing and digital engineering services.
-
Innoptus Solar Team uses Jetcam software to optimize production of solar vehicle
The world title-holding, Belgium racing team is producing its tenth composites-intensive solar car using Jetcam Expert nesting software.
-
Plant tour: Airtech International, Springfield, Tenn., U.S.
Fifty years of supplying materials for composites manufacturing includes custom fabrication and now aims to advance 3D-printed tooling, parts and new resins.