Nordex Group plans to cease rotor blade production at Rostock site in Germany
Strong competition and a shift in demand for larger blades is necessitating optimization of Nordex’s global production and sourcing processes.
Share
Read Next
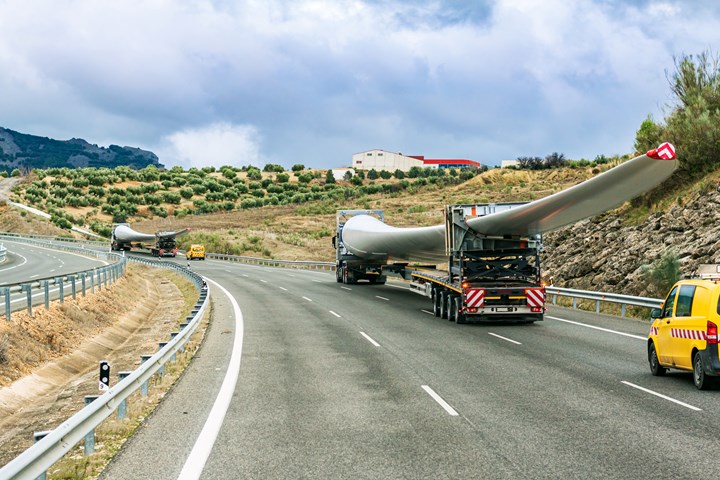
Photo Credit: Getty Images
On Feb. 28 the Nordex Group (Hamburg, Germany) informed staff at the Rostock GVZ rotor blade site in Germany about considering to cease manufacture of rotor blades at that site at the end of June 2022. A reconciliation of interests and a severance scheme are to be negotiated with the works council in the short term in order to make the planned reduction in force socially acceptable. About 600 of a total of 8,600 employees worldwide would be affected at the GVZ. In Germany, the Nordex Group employs about 3,150 people.
The increasingly challenging market environment and strong competition, together with a shift in demand, require Nordex Group’s global production and sourcing processes to be adapted.
Since the introduction of the auction system in most of the energy markets, the industry has been globally characterized by increasing price competition. Those power producers who submit the lowest bids are awarded the contract and then pass on the price pressure to the turbine manufacturers. They, in turn, have to reduce their production costs to remain competitive. The cost of energy production from wind have halved in the last five years, says Nordex Group, and this development has had a negative effect on the manufacturers’ profitability.
Against this backdrop, blade production at Rostock is, despite the cost-saving measures already implemented, not competitive within the Nordex Group’s global production network and world-wide project business. Additionally, the Rostock plant manufactures blades for turbines with a 149-meter maximum diameter. The global trend has been developing towards more efficient turbines with longer rotor blades. Consequently, demand for the blades which can be manufactured at Rostock will continue to decline.
“The wind industry operates in a highly competitive, global market that is mainly cost-driven. Against this background, we must optimize our global production and sourcing processes in order to ensure profitable production and to secure the Nordex Group’s competitiveness,” says José Luis Blanco, Nordex Group CEO. “As a German- and European-based company, we particularly regret that we do not see an alternative to this painful measure. We need an industrial policy that aims for a sustainable and comprehensive way to decarbonize and foster supply chain independency.”
Apart from the rotor blade production, Rostock is also home to a nacelle, hub and drive trains production site (DMR) as well as to Engineering and Service organization staff. These employees are not affected.
Related Content
-
Hexagon Purus opens new U.S. facility to manufacture composite hydrogen tanks
CW attends the opening of Westminster, Maryland, site and shares the company’s history, vision and leading role in H2 storage systems.
-
Composites end markets: Energy (2024)
Composites are used widely in oil/gas, wind and other renewable energy applications. Despite market challenges, growth potential and innovation for composites continue.
-
RTM, dry braided fabric enable faster, cost-effective manufacture for hydrokinetic turbine components
Switching from prepreg to RTM led to significant time and cost savings for the manufacture of fiberglass struts and complex carbon fiber composite foils that power ORPC’s RivGen systems.