Siemens Gamesa powers carbon-free future with green hydrogen
The Brande Hydrogen pilot project aims to produce green hydrogen directly from wind energy with no connection to an electricity grid. First test runs are planned for Dec. 2020 and hydrogen production by Jan. 2021.
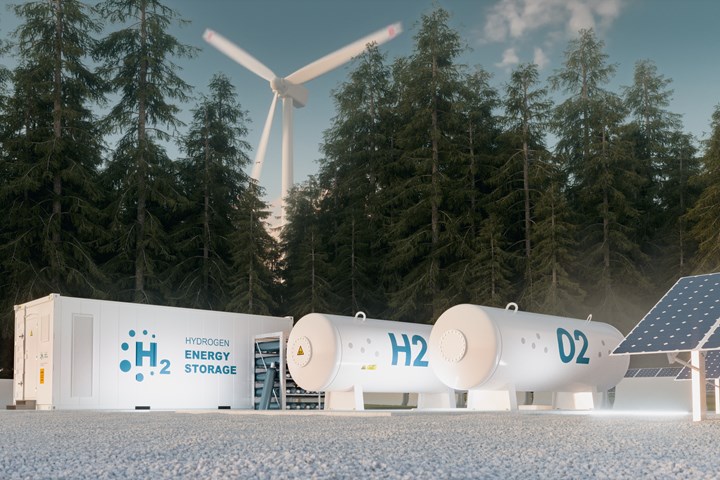
Photo Credit: Getty Images
Siemens Gamesa Renewable Energy (SGRE, Zamudio, Spain) says it is embarking on the path of decarbonizing pollution-heavy sectors including transport and heavy industry, by installing the first system in the world capable of producing green hydrogen — zero-carbon fuel made by electrolysis, using renewable power from wind and solar to split water into hydrogen and oxygen — directly with a wind turbine, with no connection to the grid (i.e. in “island mode”). This represents a strategic step towards delivering large-scale green hydrogen from the mid-2020s onwards.
“Green hydrogen has the potential to be a game changer in the quest to decarbonize the power supply and solve the climate crisis. Our wind turbines are already making a huge contribution to this effort by providing clean electricity to the grid but, with the storage potential of hydrogen, we can start addressing other key industries. This is an exciting project and I’m proud that the ingenuity and commitment of our people is enabling Siemens Gamesa to take the lead. This is the future,” says Andreas Nauen, Siemens Gamesa CEO.
Green hydrogen from renewable sources is a 100% sustainable, storable, transportable and versatile fuel. Siemens Gamesa says it represents a large opportunity for the green transition by driving the transformation of the energy system. For example, green hydrogen can be produced anywhere and used in sectors that are difficult to decarbonize, such as aviation and shipping, as well as heavy industry, such as iron and steel, chemicals and glass. The company believes hydrogen can go a long way to reducing emissions at a national and company level.
Hydrogen is already used to power the industry today, and Siemens Gamesa says it currently accounts for 1.7% of global annual energy consumption. Only 1% of that hydrogen is generated from green energy sources — the bulk is obtained from natural gas and coal, emitting 830 million tons of CO2 per year. According to the company, replacing this current polluting consumption would require 820 gigiwatts (GW) of wind generating capacity, 26% more than the current global installed wind capacity. Long-term forecasts from various industry sources point to hydrogen growing exponentially over the coming decades as transport and heavy industry decarbonize, requiring between 1,000 GW and 4,000 GW of renewable capacity by 2050 to meet demand, which highlights the vast potential for growth in wind power.
Siemens Gamesa says it is at the forefront of solving the technological challenges and delivering solutions that will enable the deployment of carbon-neutral fuels powered by renewables, proving the feasibility of reliable, effective implementation of wind turbines in systems for producing hydrogen from renewable energy.
The company is developing what it contends is the first pilot project in the world, the Brande Hydrogen project, to connect a wind turbine to an electrolyzer with the ability to operate in ‘island mode’, meaning it could drive an electrolysis rig with no link to an electricity grid.
The pilot is now under development close to Siemens Gamesa’s Danish headquarters in Brande, Denmark. It includes a 3 megawatt (MW) Siemens Gamesa wind turbine owned by local partner Uhre Windpower, that will produce clean electricity to power a 400 kilowatt (kW) electrolyzer. This machine splits water into oxygen and hydrogen, so that the hydrogen can be stored and later delivered to customers in the mobility sector. Siemens says the project is close to obtaining final permits; the first test runs are planned for December 2020 and hydrogen production should start by January 2021.
Siemens Gamesa recently signed an agreement with Danish company Everfuel, which will distribute the 100% green hydrogen produced by the facility to refueling stations across Denmark, for example in Copenhagen, where it will be used to fuel taxis. When fully operational, Siemens says the project’s single turbine will produce enough hydrogen to fuel around 50-70 taxis each day. Carbon-free hydrogen, derived from low-cost, competitive wind power, can be stored and transported for use on demand. This facility will provide insights that will be crucial to scaling up the technology to much larger turbines and wind farms both on land and at sea.
Related Content
Collins Aerospace to lead COCOLIH2T project
Project for thermoplastic composite liquid hydrogen tanks aims for two demonstrators and TRL 4 by 2025.
Read MoreComposites end markets: Batteries and fuel cells (2024)
As the number of battery and fuel cell electric vehicles (EVs) grows, so do the opportunities for composites in battery enclosures and components for fuel cells.
Read MoreHonda begins production of 2025 CR-V e:FCEV with Type 4 hydrogen tanks in U.S.
Model includes new technologies produced at Performance Manufacturing Center (PMC) in Marysville, Ohio, which is part of Honda hydrogen business strategy that includes Class 8 trucks.
Read MoreMingYang reveals 18-MW offshore wind turbine model with 140-meter-long blades
The Chinese wind turbine manufacturer surpasses its 16-MW platform, optimizes wind farm construction costs for 1-GW wind farms.
Read MoreRead Next
“Structured air” TPS safeguards composite structures
Powered by an 85% air/15% pure polyimide aerogel, Blueshift’s novel material system protects structures during transient thermal events from -200°C to beyond 2400°C for rockets, battery boxes and more.
Read MorePlant tour: Daher Shap’in TechCenter and composites production plant, Saint-Aignan-de-Grandlieu, France
Co-located R&D and production advance OOA thermosets, thermoplastics, welding, recycling and digital technologies for faster processing and certification of lighter, more sustainable composites.
Read MoreAll-recycled, needle-punched nonwoven CFRP slashes carbon footprint of Formula 2 seat
Dallara and Tenowo collaborate to produce a race-ready Formula 2 seat using recycled carbon fiber, reducing CO2 emissions by 97.5% compared to virgin materials.
Read More