Acell roofing and panel systems: A revolution in construction
Acell’s patented molding technology combines sheet molding compound (SMC) skins and a core of frangible yet fire-resistant phenolic foam.
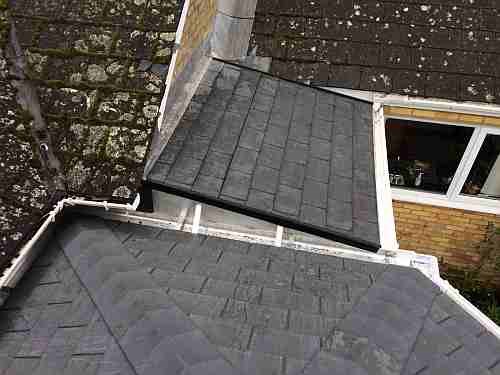
ACELL Industries Ltd. provides technology for architectural composites like these roof panels which replicate slate. Panels shown were manufactured and installed by Phil Coppell Group Ltd.
I’ve been keeping track of architectural applications of composites, and one company in particular: ACELL Industries Ltd. (Dublin, Ireland), the maker of composite architectural wall and roofing panel solutions. I’ve written a number of articles about this company, and have compiled here excerpts from those previous articles to explain the panel technology (here’s a link to one previous article with the details on how the products are made: http://www.compositesworld.com/articles/smc-sandwich-panels-lean-process-opens-doors).
Acell’s patented molding technology combines sheet molding compound (SMC) skins and a core of frangible yet fire-resistant phenolic foam, which was developed by the company nearly 30 years ago. The foam offers insulation value; flame, smoke and toxicity (FST) protection; and acoustic damping properties. A low-pressure compression molding press uses custom aluminum molds that are cast from a fiberglass master model. The model in turn is layed up directly on any selected material, such as brick, wood, slate, and other natural stone types. This makes it possible to replicate virtually any architectural surface in the mold surface, for classical finishes, such as brick, or very contemporary designs, says the company’s executive director Michael Frieh. Color is duplicated through the use of in-mold coatings, natural sand or even printed fabrics.
“The SMC skins essentially lock, mechanically and chemically, with the foam during the mold cycle,” Frieh explains, claiming that “delamination of the skins is impossible.” The low molding pressure permits the use of thin cast aluminum plates with the required surface details, which cost a fraction of typical steel or machined-aluminum SMC molds. The result is an accessible process, with a wide operational envelope at a nominal capital cost. Products include insulated building siding panels or roofing panels, that match any texture or color, including one that replicated Devon stone (here’s a link to that successful ACELL project: http://www.compositesworld.com/news/acell-architectural-project-completed).
ACELL has found success in Europe, and particularly in the United Kingdom, where more than 7 million poorly insulated or even uninsulated homes and buildings built before 1919 exist. A 2015 report from the UK Assn for the Conservation of Energy reports that the UK has very high building space heating costs, and, on the European Union’s “A to G” rating system of energy efficiency (where A is the best, or lowest energy use), the UK rates “D” or below. This is in spite of gas and electricity prices that typically are lower than in many of the 15 other European countries surveyed. Renovation to add energy efficiency, however, must be done in accordance with UK planning and building regulations that curtail any changes to a building’s original appearance if it is located within an area of “natural beauty” or a “conservation area,” says Jim Flanagan, group managing director of Phil Coppell Group Ltd. (PCL, Radcliffe, Manchester, UK), a well-known building contractor and supplier of roofing, windows and doors and extensions. Frieh adds, “The products currently available on the market for covering and insulating a façade are usually plastic siding, wood cladding or simple ‘renderings’ made up of many layers that cover the added insulation, which can be painted, but leave no option for a house originally made of bricks to keep its historical identity. And, these labor-intensive methods are delayed by any cold or wet weather.”
PCL is an ACELL partner that has invested in the ACELL process, with a manufacturing line in its factory: “We can make bespoke modular roofing products for each customer that match that home’s appearance, with excellent insulation value, that can be installed in a fraction of the time of traditional materials. We see major, major benefits with this technology.” Flanagan describes several recent projects for replacement of conservatory roofs (here’s a link that shows several styles of conservatories: http://www.philcoppell.co.uk/conservatory-styles/) using molded ACELL roofing panels. The SMC/foam molded panels are made in sections ranging from 0.8m2 to 1.8m2 in size, that replicate exactly the desired material, such as Welsh slate, clay or Roman terra cotta, for example. PCL then adds a carrier structure, usually aluminum-based, to support the panel, and fasteners to attach the panel to the roof structure. Panel insulation value can be increased if needed by adding more foam.
PCL customers with installed ACELL conservatory roofs give positive reviews on the overall appearance, plus the installers themselves are very happy with the huge savings in time and labor during installation. Says Flanagan, “ACELL molded roof panels, made to look like Welsh slate for example, speed up on-site installation and efficiency tremendously, and can be completed in all weathers.” He notes that ACELL panels can be used in low roof pitch situations, where traditional slates or clay tiles can’t be used, which gives PCL an advantage.
PCL plans on introducing, on January 3, an insulated wall panel system, or SIP (structural insulated panel), for factory-built modular homes, which Flanagan calls “a massive growth market.” Residential housing in the UK is in short supply, and Flanagan estimates that modular homes built with the SIP system, which PCL can build with the ACELL panel, will grow by 300,000 in 2017 alone. PCL and ACELL are working closely together to increase manufacturing capacity for the multi-million £ project.
Concludes Flanagan, “We’re taking a commercial approach to this composite technology for building products. We believe it can totally revolutionize building and construction, and we don’t say that lightly. This is an extremely exciting time for us.” CW will keep an eye on this developing story, particularly as ACELL moves forward with expansion into new, non-European markets.
Related Content
Composite resins price change report
CW’s running summary of resin price change announcements from major material suppliers that serve the composites manufacturing industry.
Read MoreMFFD thermoplastic floor beams — OOA consolidation for next-gen TPC aerostructures
GKN Fokker and Mikrosam develop AFP for the Multifunctional Fuselage Demonstrator’s floor beams and OOA consolidation of 6-meter spars for TPC rudders, elevators and tails.
Read MorePlant tour: Albany Engineered Composites, Rochester, N.H., U.S.
Efficient, high-quality, well-controlled composites manufacturing at volume is the mantra for this 3D weaving specialist.
Read MoreGKN Aerospace, Joby Aviation sign aerostructures agreement
GKN Aerospace will manufacture thermoplastic composite flight control surfaces for Joby’s all-electric, four-passenger, composites-intensive ride-sharing aircraft.
Read MoreRead Next
“Structured air” TPS safeguards composite structures
Powered by an 85% air/15% pure polyimide aerogel, Blueshift’s novel material system protects structures during transient thermal events from -200°C to beyond 2400°C for rockets, battery boxes and more.
Read MoreAll-recycled, needle-punched nonwoven CFRP slashes carbon footprint of Formula 2 seat
Dallara and Tenowo collaborate to produce a race-ready Formula 2 seat using recycled carbon fiber, reducing CO2 emissions by 97.5% compared to virgin materials.
Read MoreVIDEO: High-volume processing for fiberglass components
Cannon Ergos, a company specializing in high-ton presses and equipment for composites fabrication and plastics processing, displayed automotive and industrial components at CAMX 2024.
Read More