Aviation Week survey shows airlines want Boeing to develop modern 757 replacement
Need for long-hauler with up to 250 seats and 20% cost reduction could open door for composites. Boeing is already preparing via new digital engineering chief and integrated product team.
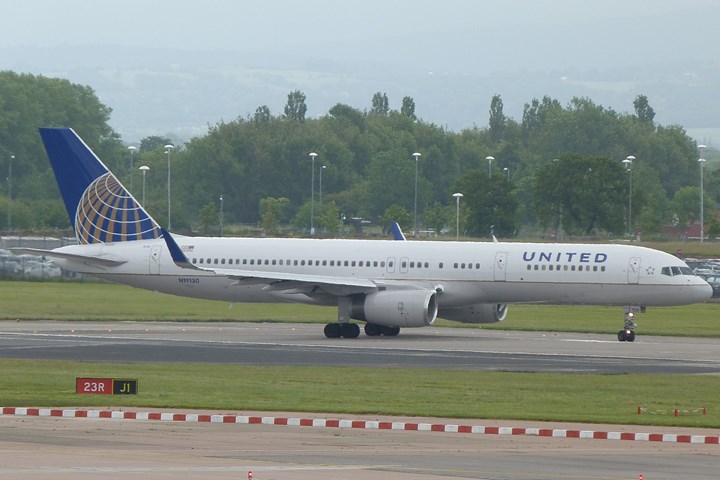
Boeing 757-200. Photo Credit: Craig Sunter, Wikimedia Commons
“Just do it.” This is the answer airlines would give if asked whether Boeing (Chicago, Ill., U.S.) should launch a new narrowbody aircraft, reports Jens Flottau and Guy Norris in a Nov. 12, 2021 Aviation Week article. This answer, they say, is based on a recently published survey conducted by the Aviation Week Network in collaboration with Bank of America Global Research. The poll of more than 900 respondents includes a large number of airlines and lessors. Key findings include:
- Customers see need for up to 250 seats and long-haul capabilities.
- Most respondents would consider a small widebody.
- Boeing should target up to 20% unit-cost reduction.
The article notes that although details have leaked from Boeing’s late-2020 study of the new mid-market airplane (NMA)-derived -5X concept to potentially fill the 757-replacement niche and counter the Airbus A321XLR, Boeing has since retrenched to focus on 787 deliveries and certifying the 777X. It goes on to point out “lower-level preparations for the launch of new products quietly continue in the background while Boeing assesses market timing and opportunities.” These measures, Flottau and Norris report, “range from establishing teams to develop new technology flight decks and other systems to forming an integrated product team [IPT] to pave the way digitally for the design and production of its next commercial aircraft using capabilities and methods largely perfected on a recent set of military programs.” (See “Boeing to build new factory to produce MQ-25 Stingray.”)
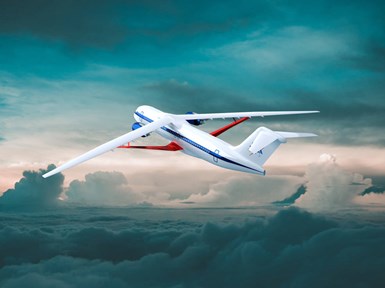
An artist’s concept of the transonic truss-braced wing aircraft configuration to be developed through the Sustainable Flight National Partnership (SFNP). Photo Credit: NASA
The Aviation Week article also reports: “Boeing is polling industry for potential input to support its proposal to NASA for a new single-aisle sustainable flight demonstrator (SFD). A competitive program, which will likely be the largest purpose-built experimental aircraft in the seven-decade X-plane series, the new aircraft will form the core of NASA’s Sustainable Flight National Partnership (SFNP) plan with other agencies, industry and academia.”
Whether Boeing proceeds with a double- or single-aisle is important for composites because the former will almost certainly move toward a composites fuselage, following on from those used in the Boeing 787 and Airbus A350 widebody aircraft. A composites fuselage in a narrowbody, however, is less certain. Composite wings seem more likely regardless of fuselage width. CW has written about this before, in “Wither the commercial aerospace landscape” and “Boeing said to be evaluating new twin-aisle program.” Notably, a March 2021 article in Aviation Week asserted that any new aircraft with more than 150 seats launched this decade — for production through the 2030s and into the 2040s — will likely require a new geared turbofan engine; extensive use of composites, especially for the wings; and/or digital design and supply chain management to reduce cycle times, working capital, labor cost and the current heavy use of over-specialized jigs and tooling.
The latter is already well underway via the IPT described above and, as reported by the Seattle Times in late September, Boeing has appointed a digital engineering chief to lead preparations for both the design of its next new commercial jet and the integrated production system that will build it. “This effort will determine the standards and interfaces by which we are linked together with a digital thread through design, test, certification, build and support,” explained a company memo.
Read more about digital thread and Composites 4.0 manufacturing below:
- SAM-XL develops closed-loop manufacturing for composites
- Speeding RTM with heat-flux sensors
- Composites 4.0: Digital transformation, adaptive production, new paradigms
- Digital thread vs. digital twin
- No business case for reteaching robots
- Composites 4.0: Where to start?
Related Content
Infinite Composites: Type V tanks for space, hydrogen, automotive and more
After a decade of proving its linerless, weight-saving composite tanks with NASA and more than 30 aerospace companies, this CryoSphere pioneer is scaling for growth in commercial space and sustainable transportation on Earth.
Read MoreTPI manufactures all-composite Kenworth SuperTruck 2 cab
Class 8 diesel truck, now with a 20% lighter cab, achieves 136% freight efficiency improvement.
Read MoreSyensqo becomes new Solvay specialty materials company
Syensqo represents what was Solvay Composite Materials, focused on delivering disruptive material technologies and supporting growing customer needs.
Read MorePartners recycle A350 composite production waste into adjustable-length rods for MFFD
Herone, Spiral RTC, Teijin Carbon Europe and Collins Aerospace Almere recycle A350 thermoplastic composite clips/cleats waste into rods for the all-thermoplastic composite Multifunctional Fuselage Demonstrator’s crown.
Read MoreRead Next
“Structured air” TPS safeguards composite structures
Powered by an 85% air/15% pure polyimide aerogel, Blueshift’s novel material system protects structures during transient thermal events from -200°C to beyond 2400°C for rockets, battery boxes and more.
Read MorePlant tour: Daher Shap’in TechCenter and composites production plant, Saint-Aignan-de-Grandlieu, France
Co-located R&D and production advance OOA thermosets, thermoplastics, welding, recycling and digital technologies for faster processing and certification of lighter, more sustainable composites.
Read MoreVIDEO: High-volume processing for fiberglass components
Cannon Ergos, a company specializing in high-ton presses and equipment for composites fabrication and plastics processing, displayed automotive and industrial components at CAMX 2024.
Read More