ÉireComposites to develop Ireland's first carbon fiber satellite optical instrument
Development and manufacture of three composite stray light baffles for the ESA’s ALTIUS satellite will assist in climate change research.
Share
Read Next
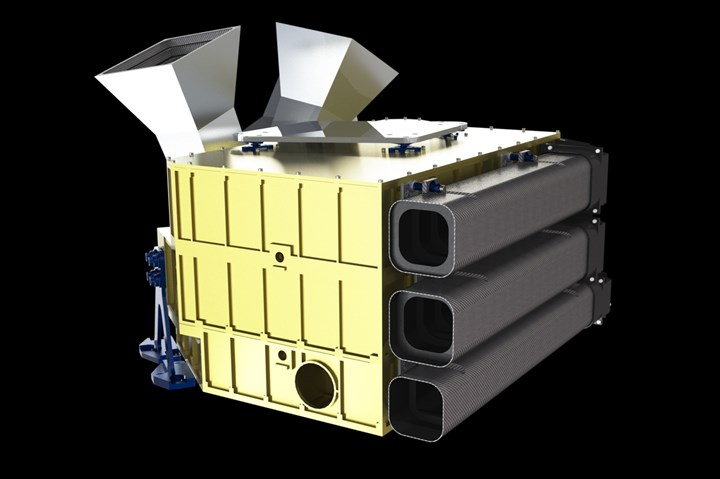
Front of the ALTIUS satellite. All photo credit: ÉireComposites
ÉireComposites (Galway, Ireland), an innovative design, manufacturing and testing company announced on March 1 an agreement with the Belgian defense and space company, OIP Sensor Systems (Oudenaarde, Belgium) to design and produce three carbon fiber stray light baffles, which will form part of the European Space Agency’s (ESA) ALTIUS satellite. According to ÉireComposites, the baffles will be the first external part and largest functioning piece of equipment manufactured in Ireland and launched into space.
With an expected launch by the end of 2023 from French Guiana, an overseas department of France on the northeast coast of South America, the ALTIUS satellite mission will deliver profiles of the Earth’s stratospheric ozone, as well as profiles of other atmospheric trace gases. This will provide scientific understanding on how the rise in greenhouse gases affects the atmosphere, and place a large role in how we view climate change.
The stray light baffles themselves, which will be attached to the side of the satellite, will prevent out-of-field stray light from reaching the lenses of the satellite’s optical instruments; a system with periscope mirrors will be used to align the light. ÉireComposites notes that stray light baffles rely upon highly controlled and precise manufacturing and finishing.
“The ALTIUS satellite will signal a major milestone for Irish participation in space exploration, as the three stray light baffles will become the first optical instruments manufactured in Ireland and the largest satellite parts manufactured in this country,” says Tomás Flanagan, ÉireComposites CEO. “I am delighted that OIP wants to work with ÉireComposites on this project. This is a massive achievement for the company and I hope this will be the first of many parts we manufacture for space exploration missions.”
He adds: “The ALTIUS mission will play a substantial role in how we look at climate change and the impact it has on Earth. The mission will allow for long-term monitoring and scientific study of the protective ozone layer which covers Earth and inform decisions around climate change. I am excited that we will be part of this research and I would like to take the opportunity to commend the team here in Inverin that have contributed to our success in obtaining this contract.”
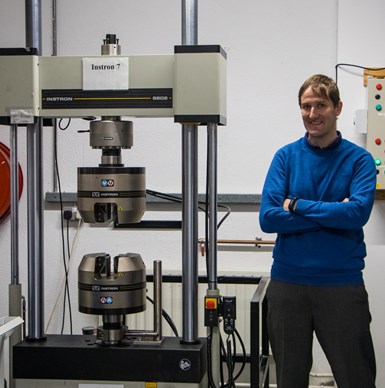
Tomás Flanagan, CEO of ÉireComposites.
The work ÉireComposites is undertaking is funded by the ESA with support from Enterprise Ireland, responsible for supporting Irish businesses. The company says winning this work was possible because of its history and close collaboration with the ESA, carrying out research and development in materials and processes, a focus ÉireComposites has maintained over the last decade. Notable projects include the development of a novel grid-stiffened lattice demonstrator for a launch vehicle in conjunction with ATG Innovation (Galway, Ireland), an engineering services company to the European Space sector.
According to Tom Kelly, manager of the Innovation and Competitiveness Division at Enterprise Ireland, this contract demonstrates the capacity of Irish technology companies to compete in the challenging space market, and the ongoing investment in the European Space Agency.
“ALTIUS is an important, challenging and very interesting project, allowing our company to contribute to actual studies related to climate change,” concludes Freddy Versluys, CEO of OIP. “The objective is to provide means to monitor the Earth’s atmosphere. OIP, being the industrial prime contractor for the payload, is responsible for the design, integration, alignment and testing of the ALTIUS instrument. We gladly announce that ÉireComposites was carefully selected as our new associate to handle the carbon fiber baffles part, in order to assist us in the further progress of the project. We trust to establish a solid working cooperation with fruitful, positive results. Good luck to our new partner!”
Related Content
Plant tour: Teijin Carbon America Inc., Greenwood, S.C., U.S.
In 2018, Teijin broke ground on a facility that is reportedly the largest capacity carbon fiber line currently in existence. The line has been fully functional for nearly two years and has plenty of room for expansion.
Read MoreCryo-compressed hydrogen, the best solution for storage and refueling stations?
Cryomotive’s CRYOGAS solution claims the highest storage density, lowest refueling cost and widest operating range without H2 losses while using one-fifth the carbon fiber required in compressed gas tanks.
Read MoreSulapac introduces Sulapac Flow 1.7 to replace PLA, ABS and PP in FDM, FGF
Available as filament and granules for extrusion, new wood composite matches properties yet is compostable, eliminates microplastics and reduces carbon footprint.
Read MorePlant tour: Joby Aviation, Marina, Calif., U.S.
As the advanced air mobility market begins to take shape, market leader Joby Aviation works to industrialize composites manufacturing for its first-generation, composites-intensive, all-electric air taxi.
Read MoreRead Next
Composites design helps nano-sized lunar rover hit big milestones
Developed by Carnegie Mellon University, the ultralight, composites-intensive Iris nano-rover will make its lunar debut later this year.
Read MoreAnalySwift and University of Central Florida work with NASA to develop thin-ply composites
Materials will be characterized and performance modeled for wide array of aircraft and space applications.
Read MorePlant tour: Daher Shap’in TechCenter and composites production plant, Saint-Aignan-de-Grandlieu, France
Co-located R&D and production advance OOA thermosets, thermoplastics, welding, recycling and digital technologies for faster processing and certification of lighter, more sustainable composites.
Read More