HexPly M901 prepreg accelerates product development cycles
Hexcel’s HexPly M901 prepreg system reportedly reduces production time of composite leaf springs.
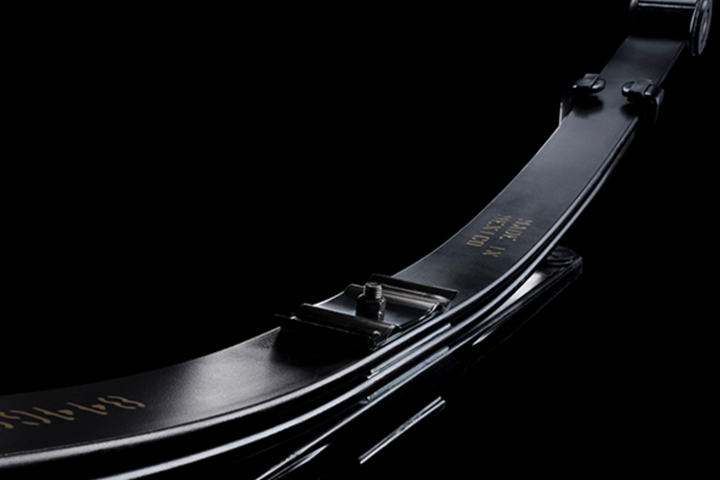
Photo Credit: Rassini
Rassini (Mexico City, Mexico), a technology leader in composite vehicle suspension systems, has selected Hexcel’s (Stamford, Conn., U.S.) HexPly M901 prepreg system to speed up prototype and new product development cycles. Using this system, Rassini hopes to reduce overall time to market and enable cost-effective production.
As a specialist in the mass production of composite helper leaf springs for OEMs, Rassini continuously develops new suspension component designs. Due to cost and timing, however, these new products cannot easily be prototyped using conventional high-pressure resin transfer molding (HP-RTM) technology.
With more than 15 years of experience in delivering glass fiber prepregs for the serial production of composite leaf springs, Hexcel developed its high-performance HexPly M901 prepreg system specifically for this type of application.
HexPly M901 is a high Tg epoxy resin prepreg system specifically developed for structural components that will be exposed to harsh thermal and environmental conditions. With short cure cycles of 10 minutes and below, HexPly M901 reportedly delivers a combination of benefits for suspension component applications. It produces green (i.e., handling) strength of the composite part for demolding and unidirectional (UD) glass fiber aerial weights up to 1,600 grams per square meter.
Further, HexPly M901 is claimed to offer significant advantages for lower volume serial production of composite mono leaf springs. HexPly M901’s mechanical performance is approximately 15% higher than standard prepregs, with enhanced fatigue properties and a Tg of up to 200˚C following post cure.
Related Content
-
ASCEND program update: Designing next-gen, high-rate auto and aerospace composites
GKN Aerospace, McLaren Automotive and U.K.-based partners share goals and progress aiming at high-rate, Industry 4.0-enabled, sustainable materials and processes.
-
SMC composites progress BinC solar electric vehicles
In an interview with one of Aptera’s co-founders, CW sheds light on the inspiration behind the crowd-funded solar electric vehicle, its body in carbon (BinC) and how composite materials are playing a role in its design.
-
Thermoplastic composites: Cracking the horizontal body panel nut
Versatile sandwich panel technology solves decades-long exterior automotive challenge.