Satair, FACC sign global exclusive distribution agreement
Multi-year agreement covers distribution of Airspace XL bins, entrance area, ceiling panels and all related spares for the entire A320 aircraft family, much of which incorporates composite materials.
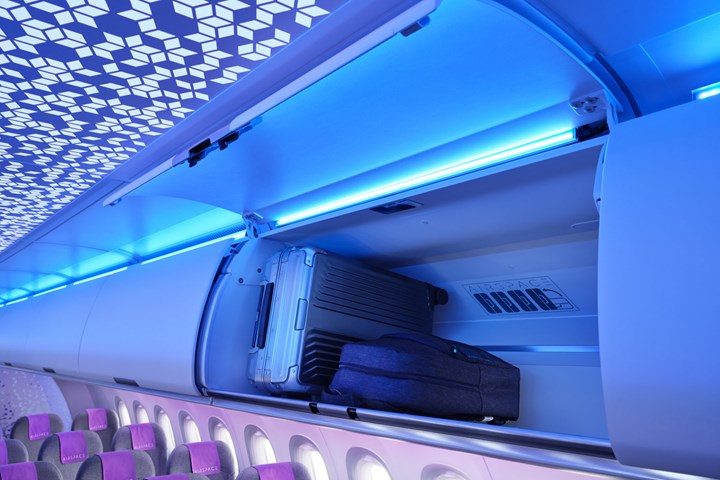
Photo Credit: Airbus
Satair (Copenhagen, Denmark), an Airbus Services company and commercial aerospace aftermarket leader, and FACC AG (Ried im Innkreis, Austria), a manufacturer of advanced aircraft components and systems for the global aerospace industries, have signed the first agreement between the two companies. The multi-year agreement covers the global exclusive distribution of Airspace XL bins (overhead stowage compartments), the entrance area, ceiling panels and all related spares for the entire A320 aircraft family. The entrance area and storage bins incorporate composite materials.
Further, as part of the new agreement, Satair will perform Supplier Support Conditions on FACC’s behalf related to covering the spares-related activities.
“We are pleased to bring the many benefits of low weight and high reliability through FACC’s products to our airline customers worldwide to help give their passengers the luxury of roomier overhead bins and ambient ceiling panels,” says Matt Jessee, head of OEM business development, Satair.
Besides furnishing ceiling panels that illuminate the cabin with ambient LED light, the overhead stowage compartments covered by the agreement provide 40% more space. Specifically, the Airspace XL bins, the largest overhead stowage compartments in the short- and medium-haul class, can reportedly hold up to 60% more luggage — eight pieces of hand luggage instead of the previously five, measuring 61 x 40.6 x 25.4 centimeters.
“By using innovative fiber-reinforced composite materials and new manufacturing technologies, we are able to create products for the aircraft cabin that contribute to consistent weight optimization,” adds Andreas Furthmayr, vice president cabin interiors program, FACC. “We are excited to work with Satair on bringing our innovative solutions to airlines across the world.”
Related Content
-
Plant tour: Spirit AeroSystems, Belfast, Northern Ireland, U.K.
Purpose-built facility employs resin transfer infusion (RTI) and assembly technology to manufacture today’s composite A220 wings, and prepares for future new programs and production ramp-ups.
-
Next-generation airship design enabled by modern composites
LTA Research’s proof-of-concept Pathfinder 1 modernizes a fully rigid airship design with a largely carbon fiber composite frame. R&D has already begun on higher volume, more automated manufacturing for the future.
-
PEEK vs. PEKK vs. PAEK and continuous compression molding
Suppliers of thermoplastics and carbon fiber chime in regarding PEEK vs. PEKK, and now PAEK, as well as in-situ consolidation — the supply chain for thermoplastic tape composites continues to evolve.