Siemens Gamesa, Siemens Energy partner for offshore green hydrogen production acceleration
Five-year project is the first major step to develop an industrial-scale system capable of harvesting green hydrogen from offshore wind.
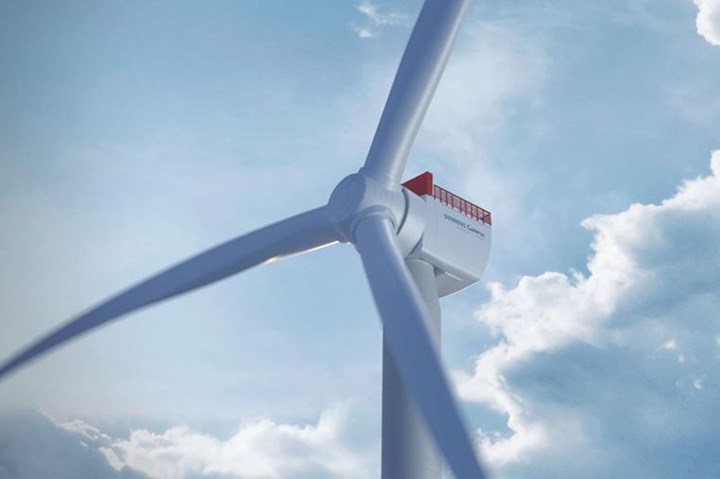
SGRE’s SG 14-222 DD turbine, which retains a 222-meter rotor and 108-meter-long B108 blades, based on IntegralBlade technology. Photo Credit: SGRE
Siemens Gamesa Renewable Energy (SGRE, Zamudio, Spain) and Siemens Energy AG (Munich, Germany) have announced that the companies are combining ongoing wind-to-hydrogen developments to address decarbonizing the economy (see “Siemens Gamesa powers carbon-free future with green hydrogen”).
The innovative solution will fully integrate an electrolyzer — a system that uses electricity to break water into hydrogen and oxygen in a process called electrolysis — into an offshore wind turbine as a single synchronized system to directly produce green hydrogen. The companies intend to provide a full-scale offshore demonstration of the solution by 2025/2026. Further, German Federal Ministry of Education and Research announced that the developments can be implemented as part of the ideas competition “Hydrogen Republic of Germany.”
“Our more than 30 years of experience and leadership in the offshore wind industry, coupled with Siemens Energy’s expertise in electrolyzers, brings together brilliant minds and cutting-edge technologies to address the climate crisis,” says Andreas Nauen, Siemens Gamesa CEO. “Our wind turbines play a big role in the decarbonization of the global energy system, and the potential of wind to hydrogen means that we can do this for hard-to-abate industries, too. It makes me proud that our people are a part of shaping a greener future.”
Over a timeframe of five years, Siemens Gamesa plans to invest EUR €80 million and Siemens Energy is targeting to invest EUR €40 million in the developments. Siemens Gamesa says it will adapt development of its SG 14-222 DD offshore wind turbine to integrate an electrolysis system seamlessly into the turbine’s operations. By leveraging Siemens Gamesa’s knowledge and decades of experience with offshore wind, electric losses will reportedly be reduced to a minimum, while a modular approach ensures a reliable and efficient operational setup for a scalable offshore wind-to-hydrogen solution. Siemens Energy plans to develop a new electrolysis product to not only meet the needs of the harsh maritime offshore environment and to be in perfect sync with the wind turbine, but also to create a new competitive benchmark for green hydrogen.
According to Siemens Gamesa, the solution will ultimately lower the cost of hydrogen by being able to run off-the-grid, opening up more and better wind sites. The companies’ developments will also serve as a testbed for making large-scale, cost-efficient hydrogen production a reality.
Further, the developments are part of the H2Mare initiative, which, under the consortium lead of Siemens Energy, is a modular project consisting of multiple sub-projects to which more than 30 partners from industry, institutes and academia are contributing. Siemens Energy and Siemens Gamesa will contribute to the H2Mare initiative with each company’s own developments in separate modular building blocks.
Related Content
Honda begins production of 2025 CR-V e:FCEV with Type 4 hydrogen tanks in U.S.
Model includes new technologies produced at Performance Manufacturing Center (PMC) in Marysville, Ohio, which is part of Honda hydrogen business strategy that includes Class 8 trucks.
Read MoreCollins Aerospace to lead COCOLIH2T project
Project for thermoplastic composite liquid hydrogen tanks aims for two demonstrators and TRL 4 by 2025.
Read MoreComposites end markets: Energy (2024)
Composites are used widely in oil/gas, wind and other renewable energy applications. Despite market challenges, growth potential and innovation for composites continue.
Read MoreAchieving composites innovation through collaboration
Stephen Heinz, vice president of R&I for Syensqo delivered an inspirational keynote at SAMPE 2024, highlighting the significant role of composite materials in emerging technologies and encouraging broader collaboration within the manufacturing community.
Read MoreRead Next
All-recycled, needle-punched nonwoven CFRP slashes carbon footprint of Formula 2 seat
Dallara and Tenowo collaborate to produce a race-ready Formula 2 seat using recycled carbon fiber, reducing CO2 emissions by 97.5% compared to virgin materials.
Read MoreVIDEO: High-volume processing for fiberglass components
Cannon Ergos, a company specializing in high-ton presses and equipment for composites fabrication and plastics processing, displayed automotive and industrial components at CAMX 2024.
Read MoreDeveloping bonded composite repair for ships, offshore units
Bureau Veritas and industry partners issue guidelines and pave the way for certification via StrengthBond Offshore project.
Read More