TFP Hydrogen extends coating capability with U.S. line
High-performance, optimized coatings increase system lifetime and efficiency in electrochemical technologies ranging from hydrogen fuel cells and batteries to PEM water electrolyzers.
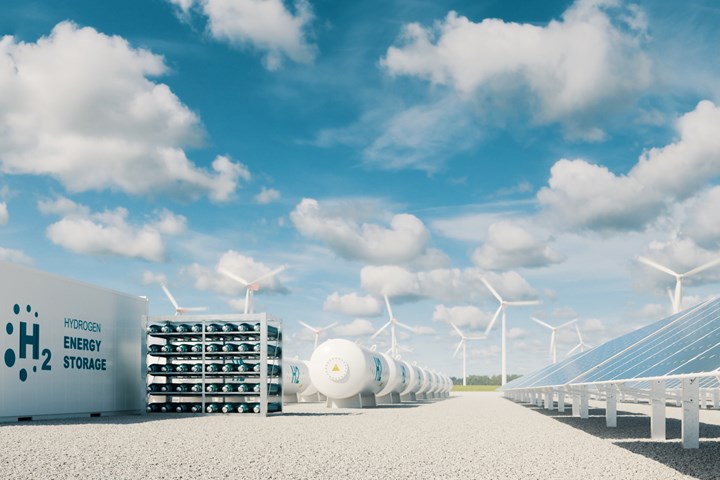
Photo Credit: Getty Images
TFP Hydrogen Products (Burneside, U.K.) — the hydrogen division of Technical Fibre Products, a global manufacturer of wet-laid nonwovens — has announced that the installation of a state-of-the-art coating facility is currently underway at TFP’s North American site in Schenectady, New York. The line is a necessary addition to support the rapid growth in the hydrogen sector, the company says, where its coatings are reported to improve the efficiency and durability of polymer electrolyte membrane (PEM) water electrolysers, thus reducing the cost of green hydrogen production.
“The incorporation of this specialized technology in Schenectady as well as the U.K. is an important step in the growth of TFP Hydrogen,” notes David Hodgson, managing director of TFP Hydrogen Products. “It will provide the necessary capacity increase to respond to the increasing demand for our materials, as well as enabling us to support our North American customers’ requirements locally.”
The new line is based on the specialist coating technology that TFP Hydrogen has developed in the U.K., said to deliver high-performance, optimized coatings for components used in electrochemical processes, such as PEM water electrolysis. Green hydrogen will play a critical part of the global transition to sustainable energy, the company acknowledges, and PEM electrolysers are central to its generation, using the energy from renewable sources such as wind and photovoltaics to produce hydrogen.
In addition to their use in water electrolysis, TFP Hydrogen’s materials are used to increase system lifetime and performance in a variety of other electrochemical technologies. These applications range from hydrogen fuel cells and batteries to advanced wound-care, water purification and even the regeneration of coral reefs.
Related Content
-
Collins Aerospace to lead COCOLIH2T project
Project for thermoplastic composite liquid hydrogen tanks aims for two demonstrators and TRL 4 by 2025.
-
Composites end markets: Batteries and fuel cells (2024)
As the number of battery and fuel cell electric vehicles (EVs) grows, so do the opportunities for composites in battery enclosures and components for fuel cells.
-
On the radar: Cryogenic testing of composites for future hydrogen storage
Netherlands, U.K., France, Germany and the U.S. build up test capability, look at thermoset and thermoplastic composite materials.