Another win on a carbon composite SUP - Update
CW’s June 2017 Focus on Design story was about the design and creation of a custom carbon composite racing SUP or stand-up paddleboard (that led to a similar production SUP for consumers) for paddle athlete Travis Grant. Grant just won this year’s Molokai to Oahu race, on a new carbon fiber SUP, and set a world record.
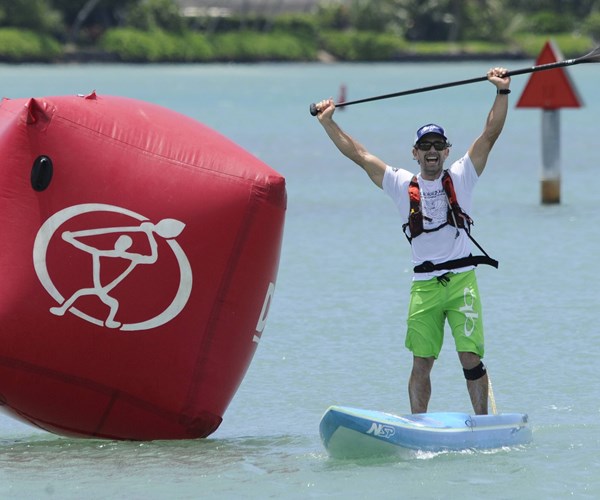
Travis Grant crosses the finish line of the 2017 M2O race in Hawaii on an all-carbon composite SUP board from NSP and Cobra International. Photo from the Honolulu Star Advertiser, photographer Bruce Asato.
I hope you all had a chance to read my June 2017 Focus on Design story about the design and creation of a custom carbon composite racing SUP or stand-up paddleboard (that led to a similar production SUP for consumers) for paddle athlete Travis Grant, winner of the 2015 (and earlier 2013) Molokai 2 Oahu Ocean Race across the Ka’iwi Channel, a distance of 52 km. Because the focus of that story was on the composite board and how it came to be, I never got the chance to interview Grant, although I scoured media reports and his Facebook page, where he talked about that win.
Grant recently contacted me, and told me that he is the winner of the 2017 edition of M2O race, held on July 30, again on a Cobra International Co. Ltd. (Chonburi, Thailand) – manufactured, NSP (Singapore)-designed Molokai custom SUP. And, he set a new record time for the event. I reached out to Trent Pedersen, who is a technical consultant to NSP and the Aroona Group, the distributor of NSP boards in Australia and New Zealand, and involved in the realization of Grant’s 2017 board, for some details.
“The latest design Travis used is quite different to the one you featured [in the FOD],” says Pedersen. “As you can see from the CAD screen shot, the main difference is overall the board is thicker, rails are higher, and we recessed the deck a lot, to make a ‘dugout’ style board. The reason was to increase stability, and reduce drag in the rough conditions by not having the water ‘suck’ over onto the deck of the board. The nose area is thicker with a really defined V-shape so the water releases, and at the same time we designed a high cowling to stop water entering the cockpit.” He adds that the board has four drain holes that allow water to drain, designed so that the holes themselves don’t cause drag.
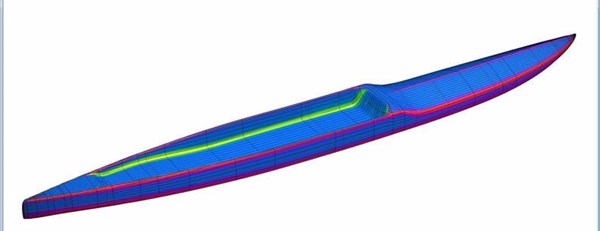
CAD screen shot of the 2017 dugout-style SUP, from NSP
Pedersen adds that because the dugout design has a much more pronounced and recessed standing area, this increased the overall surface area of the board. That meant the old (2015) layup would be too heavy, and not give sufficient strength.
“The thickness of the standing area was reduced by approximately 40% so we had to maintain the structural integrity in this area. The EPS core density stayed at 15.5 kg/m2, but we changed the material layup. For the bottom, the previous board used a combination of ±45° biaxial carbon and fiberglass, which meant 250gsm of fiber. For the new design we opted for 100% carbon and combined a +30/-30 degree biax and a UD carbon. The resulting total reinforcement weight ended up 180 gsm, so it was lighter, 100% carbon, and the orientation of fibers gave more stiffness,” explains Pedersen.
For the deck, the 2015 board was made with a combination of plain weave carbon and glass, with about 260 gsm areal weight. “For the new design we opted for 100% carbon using the same materials as the bottom. The 100% carbon layup allowed us to reduce the density and thickness of the PVC material in the standing area, further reducing weight. We still used some light fiberglass in the PVC sandwich.” Further, the team opted to replace the 20cm wide PVC/fiberglass stringer at the nose area with small-tow carbon fiber T-stringers, one near each rail and one down the center line: “Essentially we cut 2.5 cm deep into the board and laminated a 10cm wide piece of carbon creating a T shape using the carbon fiber, for more stiffness,” explains Pedersen. Board rails had an extra layer of carbon added, for the same double wrap like the earlier board, and glass strips were added in high impact areas on top of the rail.
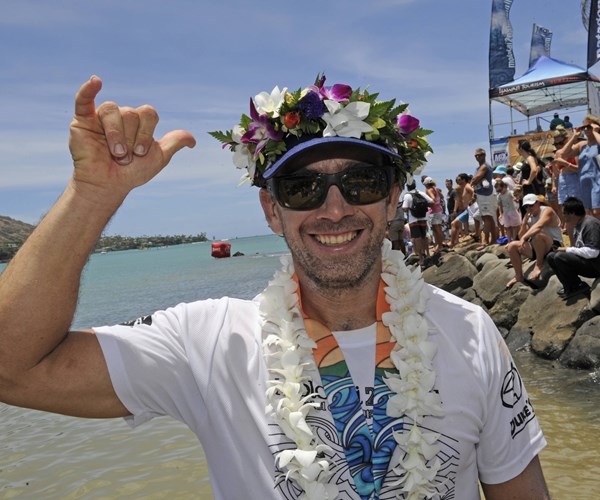
Travis Grant at the finish (photo from the Honolulu Star Advertiser, photographer Bruce Asato).
Grant finished in 3 hours, 59 minutes and 52 seconds, setting a new world record in the men’s unlimited stand-up paddleboard division, and breaking the 4-hour time barrier, in a close contest with 2nd-place finisher Connor Baxter. Grant was quoted on the official race press release as saying “I never thought SUP could not break 4 hours…It was hard. I hope this record stands for longer than a year.”
There are a lot of videos and photos if you’re interested, including this one from NSP: https://www.youtube.com/watch?v=jr2_TbhZ67o&feature=youtu.be. Try this link for a 6-minute short movie celebrating the 20-year history of the race here: https://www.youtube.com/watch?v=knkota3U0Ak&feature=youtu.be . Grant appears at the very end of the video, as he crosses the finish line. The official Web site of the event is here: http://www.molokai2oahu.com/. Start paddling!
Related Content
Mito Materials graphene amplify composite fly fishing rod performance
Functionalized graphene addition to premium-performance Evos and Evos Salt fly rods by St. Croix Fly enables faster recovery, increased torsional rigidity and improved strength-to-weight ratios.
Read MoreTime Bicycles to modernize composite bicycle manufacturing
With the aid of KraussMaffei, Clemson University and SC Fraunhofer USA Alliance, Time anticipates a transition to HP-RTM for more efficient carbon fiber bike frame manufacture, plus a new facility in South Carolina.
Read MorePlant tour: Arris Composites, Berkeley, Calif., U.S.
The creator of Additive Molding is leveraging automation and thermoplastics to provide high-volume, high-quality, sustainable composites manufacturing services.
Read MoreToray rCF from Boeing 787 is incorporated into ultra-light laptops
Torayca-based aerospace components have successfully been repurposed into the Lenovo ThinkPad X1 Carbon Gen 12, highlighting the ongoing application of recycled composites.
Read MoreRead Next
VIDEO: High-volume processing for fiberglass components
Cannon Ergos, a company specializing in high-ton presses and equipment for composites fabrication and plastics processing, displayed automotive and industrial components at CAMX 2024.
Read MorePlant tour: Daher Shap’in TechCenter and composites production plant, Saint-Aignan-de-Grandlieu, France
Co-located R&D and production advance OOA thermosets, thermoplastics, welding, recycling and digital technologies for faster processing and certification of lighter, more sustainable composites.
Read MoreDeveloping bonded composite repair for ships, offshore units
Bureau Veritas and industry partners issue guidelines and pave the way for certification via StrengthBond Offshore project.
Read More