ATL Composites parts enable Roger Hill-designed powercat
New 16-meter composite displacement hull powercat uses DuFLEX composite panels from ATL Composites.

Source | ATL Composites
A new 16-meter composite displacement hull powercat designed by legendary designer, Roger Hill, being built at Lifestyle Yachts (Pipiroa, New Zealand) uses DuFLEX composite panels from ATL Composites (Molendinar, Queensland, Australia). The panels comprise rigid end-grain balsa, and structural linear or cross-linked foam cores laminated with a high-performance epoxy resin and reinforced with multiaxial E-glass.
The custom-built yacht Omahu is the vision of joint-owners, two Kiwi couples keen to experience long-range cruising around the South Pacific, exploring New Caledonia, Fiji, Tonga and Australia.
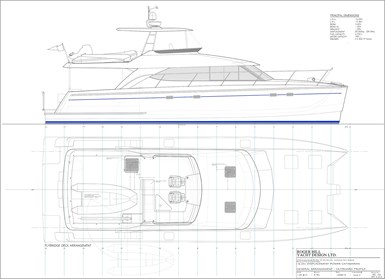
Source | Roger Hill Yacht Design Ltd.
“The hull shape is a development of our very efficient displacement form, but the styling is unique compared to other similar-sized powercats we have done before,” Hill explains. “It is not a ‘cut and shut’ exercise using an existing similar sized design.”
One of the owners had previously built a Roger Hill-designed 14.15-meter sailing cat, around 15 years ago, customized to his requirements at that time. The choice of building materials, methodology and designer informed his choice for the current project.
The Omahu is designed for comfort with space for two couples to live aboard along with storage required for long trips to remote destinations. The vessel is powered by twin Yanmar 6LY400 400hp engines and is calculated to achieve a top speed of 26 knots.
“This particular design does not have as much beam (5.6 meters) as I might normally have on a displacement power cat of this length, but this was related to the width of the marina berth,” says Hill. “The upside of that slightly narrower beam, less transverse stability will be an improved motion; not such a quick roll period in a beam sea.”
A shallow draft of just over 1 meter will allow Omahu to explore remote inlets and anchorages where other yachts may not be able to access.

Source | ATL Composites
Hill based the design of Omahu on construction using DuFLEX Composite panels from ATL Composites based on their strength, durability, light-weight and precision.
Hill recalls,
“ATL and I go back a long way. The first DuFLEX kit we did was over 18 years ago, and we have done many since then in both power and sail. One of Omahu’s owners had already built a sailing cat using the DuFLEX panel system so he was very happy to build the power cat using the same materials and method of construction.
“Another consideration was the builder, who didn’t have a lot of experience building a full-foam cored catamaran, so he has been very appreciative of the pre-made panels and CNC router set of parts.
“The DuFLEX Building System offers builders a very high-quality panel and very precise accuracy, and for the client, an assurance of structural integrity.”
Omahu will have a dark blue hull which dictated the choice of foam core to be used in the hull and transom areas. A combination of Divinycell HP80 and HP100 foam cores, type approved by DNV-GL Maritime, were chosen for the DuFLEX Strip Planks used in these areas to provide elevated temperature and mechanical performance.

DuFLEX Composite Panels were also used for Omahu’s bulkheads. Source | ATL Composites
Engineered to survey standards by ATL Composites Engineering team, other DuFLEX Composite Panels components in Omahu include wing-deck, soles, girders, webs, bulkheads, longitudinal and interiors all supplied in CNC-routed kit form with various core types and densities to suit the design loads in the vessel.
Related Content
Mel Composites infusion strategy enables Sasga Yachts fiberglass hull designs
Mel’s ongoing partnership culminates in the development of the Menorquín 42 and Menorquín 54 motor yachts, as well as extension of Sasga’s capacity for 68-foot-length boats.
Read MoreChantiers de l’Atlantique reveals 66-meter, all-composite SolidSail mast
A technological feat, the large carbon fiber mast prototype targets the Silenseas sailing liner and sailing cargo ships for up to 40% reduction in CO2 emissions.
Read MoreEvolving natural fiber technology to meet industry sustainability needs
From flax fiber composite boats to RV exterior panels to a circularity model with partnerships in various end markets, Greenboats strives toward its biomaterials and sustainable composites vision in an ever-changing market.
Read MoreAlliance for European Flax-Linen and Hemp reports increasing flax fiber adoption in marine
The natural fiber is increasing traction across several marine applications, including in projects by Greenboats, Northern Light Composites, the Beneteau Group and others.
Read MoreRead Next
VIDEO: High-volume processing for fiberglass components
Cannon Ergos, a company specializing in high-ton presses and equipment for composites fabrication and plastics processing, displayed automotive and industrial components at CAMX 2024.
Read MoreAll-recycled, needle-punched nonwoven CFRP slashes carbon footprint of Formula 2 seat
Dallara and Tenowo collaborate to produce a race-ready Formula 2 seat using recycled carbon fiber, reducing CO2 emissions by 97.5% compared to virgin materials.
Read MoreDeveloping bonded composite repair for ships, offshore units
Bureau Veritas and industry partners issue guidelines and pave the way for certification via StrengthBond Offshore project.
Read More