Carbon/epoxy Cadillac hood in production
While they typically keep their research efforts close to the vest, automakers and automotive Tier suppliers nevertheless are always in the process of evaluating the multitude of materials available for lightweighting.
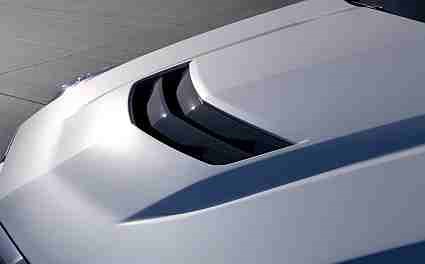
Magna International molds this Cadillac hood with carbon/epoxy prepreg from Barrday Composite Solutions.
While they typically keep their research efforts close to the vest, automakers and automotive Tier suppliers nevertheless are always in the process of evaluating the multitude of materials available for lightweighting, in order to meet fuel economy mandates. One example is automotive Tier 1 giant Magna International Inc. (Aurora, Ontario, Canada), a leading automotive supplier with more than 140,000 employees in 29 countries. The company started a carbon fiber composites program in 2008, says Tom Pilette, global vice president, product and process development at Magna: “We began developing composites for structural parts, as well as Class A body panels, and formed a joint development agreement with Zoltek Corp. [Bridgeton, MO, US] using 50K carbon tow material. We saw the lightweighting trend coming, but knew it was going to be a long process.” That early work led to an opportunity in 2013 to submit a quote to General Motors (Detroit, MI, US) for composite hoods for the 2016 model year Cadillac ATS/CTS V-Series cars, two higher-performance Cadillac models. Approximately 7,000 parts are being produced each year for each model, for a total of 14,000 hoods, although capacity exists for much higher volumes. The hood was a winner of a JEC Innovation Award at the just-concluded JEC Americas event in Atlanta, GA, US, in the Automotive category.
Andrew Swikoski, global product line director for lightweight composites, explains that the Cadillac hood was a good candidate part for lightweighting, given its location above the car’s center of gravity and forward of the axle. The carbon composite provides the stiffness needed to avoid hood “flutter” and has resulted in a mass savings of between 20 and 30 percent compared to aluminum or steel hoods (the range is dependent on the grade of steel or aluminum to which it is compared). The out-of-autoclave compression molding process takes just minutes per part, yet produces a Class A surface. A key achievement of the hood program, he adds, is that parts can be post-processed just like metallic versions, that is, the carbon fiber/epoxy material can withstand Magna’s normal part painting process and associated temperatures, without resorting to off-line, manual painting and “finesse and filler” steps. “Our goal was to have a composite part capable of seamless, in-line finish processing,” adds Pilette.
The hood was designed with a unidirectional carbon fiber inner and outer, with an optional exposed carbon fiber inner, adhesively bonded together. Steel hard points are bonded at hinge and latch locations. The outer panel has a thickness of 1.2 mm, and the inner, 0.8 mm. Working closely with material suppliers Zoltek and Barrday Composite Solutions (Millbury, MA, US) at the Magna-NRC Composites Centre of Excellence — a joint Magna/Canadian research center dedicated to composites located at Magna’s Concord, Canada facility — Magna went through “many iterations” of resin chemistry development, prepreg stack design, tool design and cycle time tweaks to achieve an acceptable finished outer surface, says Pilette. The resulting prepreg resin system, supplied by Barrday, is a customized toughened epoxy combined with Zoltek fiber for a prepreg with a high glass transition temperature (Tg) that can handle the Magna paint line temperatures.
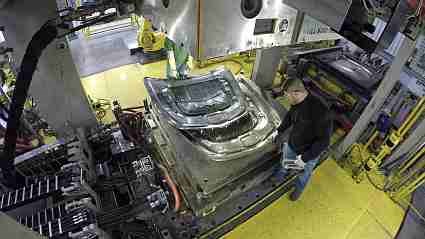
This shear-edge steel compression tool, designed by Magna, molds the Cadillac hood in minutes.
“Typically, a prepreg part charge tends to be a patchwork of multiple plies that takes time to lay up manually,” explains Pilette. The Magna team has perfected an automated work cell that creates a molding charge by robotically laying multiple plies of standard-width, 0.02 mm-thick, Barrday prepreg in a 0°/90° orientation, which are CNC cut into a charge pattern that is robotically transferred to the mold. The patented mold design is a shear-edge steel design, with a “unique” and proprietary combination of tooling features that reportedly manage the movement of the stacked plies during mold close and pressure application. Adds Pilette, “The prepreg starts to cure as soon as it hits the heated tool, so the stack has be placed precisely and stay in place. The tool helps maintain resin consistency, ensures good fiber wetout and part thickness.” He notes that Fibersim software from Siemens PLM Software (Plano, TX, US) was a manufacturability tool that “helped tremendously” in developing the prepreg stack pattern for compression molding.
The Barrday material is manufactured in that company’s Cambridge, Ontario, Canada facility, and molding occurs at Polycon Industries (Guelph, Ontario, Canada, a Magna subsidiary). The process begins with automated layup and ply stacking, charge cutting and mold loading. After tool close and press application, cure time takes about 10 minutes. The robot removes the molded part, shuttles it to a router cell for trimming, then to a bonding cell and a fixture. Bonding of the inner and outer panels is also automated, and the metallic hinge and closure elements, while positioned by hand, are also robotically bonded. Pliogrip two-part urethane adhesive from Ashland Performance Materials (Columbus, OH, US) is used. Bonded parts then go to the Magna paint line, and after painting are shipped to General Motors. “We’re now working on cutting that cure time in half, with adjustments to the epoxy,” asserts Pilette.
Pilette and Swikoski both say that, now that a robust and successful molding process has been developed, Magna’s goal is to expand the use of this newly-developed technology with multiple carbon composite body panels, on more platforms. “We understand these materials, and with our in-house chemists and laboratory, and collaboration with our supply partners, we can offer solutions to meet our customers’ needs,” says Pilette. Watch for more composites parts from this automotive powerhouse.
Related Content
McLaren celebrates 10 years of the McLaren P1 hybrid hypercar
Lightweight carbon fiber construction, Formula 1-inspired aerodynamics and high-performance hybrid powertrain technologies hallmark this hybrid vehicle, serve as a springboard for new race cars.
Read MorePlant tour: Joby Aviation, Marina, Calif., U.S.
As the advanced air mobility market begins to take shape, market leader Joby Aviation works to industrialize composites manufacturing for its first-generation, composites-intensive, all-electric air taxi.
Read MoreNatural fiber composites: Growing to fit sustainability needs
Led by global and industry-wide sustainability goals, commercial interest in flax and hemp fiber-reinforced composites grows into higher-performance, higher-volume applications.
Read MorePEEK vs. PEKK vs. PAEK and continuous compression molding
Suppliers of thermoplastics and carbon fiber chime in regarding PEEK vs. PEKK, and now PAEK, as well as in-situ consolidation — the supply chain for thermoplastic tape composites continues to evolve.
Read MoreRead Next
Developing bonded composite repair for ships, offshore units
Bureau Veritas and industry partners issue guidelines and pave the way for certification via StrengthBond Offshore project.
Read More“Structured air” TPS safeguards composite structures
Powered by an 85% air/15% pure polyimide aerogel, Blueshift’s novel material system protects structures during transient thermal events from -200°C to beyond 2400°C for rockets, battery boxes and more.
Read MoreVIDEO: High-volume processing for fiberglass components
Cannon Ergos, a company specializing in high-ton presses and equipment for composites fabrication and plastics processing, displayed automotive and industrial components at CAMX 2024.
Read More