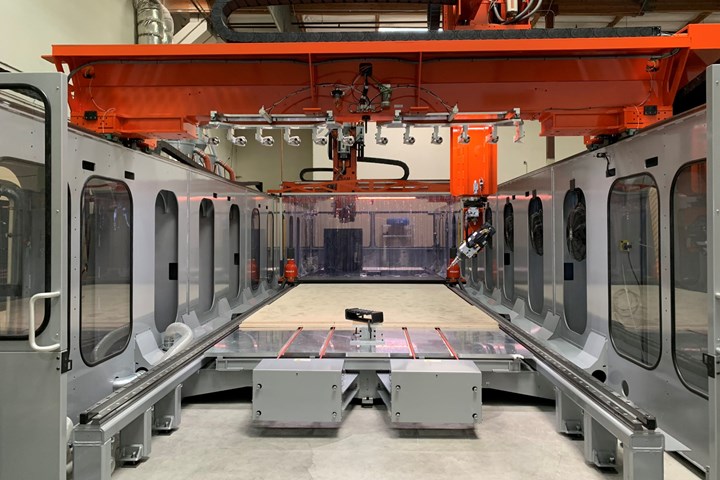
Photo Credit: Ascent Aerospace
About 10 years ago, I was talking to someone about additive manufacturing (AM), which at the time was in the early stages of its ascendancy. AM was the topic of much mainstream and trade press coverage, heralded as a paradigm-shifting technology poised to reshape manufacturing. My interlocutor, a veteran of the composites industry, assumed a somewhat defensive position about AM — particularly AM with fiber reinforcement — pointing out with some disdain that “composites manufacturing was additive manufacturing before additive manufacturing was additive manufacturing!”
This is, of course, a true statement, but it obscures some of the challenges posed by composite materials and composites manufacturing that AM doesn’t have the luxury to ignore. Those composites challenges are well known and revolve around the fact that the great variety of resins, fibers, tooling materials and processing types creates a highly complex materials and process environment that is difficult to design for and difficult to simulate. It also makes process control tricky, tends to generate waste and engenders much hand work and fat design margins, as a hedge against the uncertainty of it all.
Continuous fiber AM is the closest thing to composites manufacturing standardization.
We, as an industry, have talked about these challenges for many, many years, pointing to materials standardization, more robust design tools, improved process control and automation as the technologies that might impose some order on the disorder that (sometimes) is composites manufacturing.
Meanwhile, as the AM industry has matured, system suppliers that offer continuous fiber-reinforced materials and process options proliferated, covering a range of deposition options, size formats, resin types, cure options and much more. For a glimpse of this, see Senior Editor Ginger Gardiner’s story about the continuous fiber AM landscape.
If you are one of these continuous fiber AM suppliers, however, you must adhere to the AM technology push-button model, which demands that a design go in one end and a finished part come out the other. In between, with little or no user input, the machine and its slicer software makes thousands, if not millions, of decisions about where and how to deposit resin and fibers to meet the mechanical requirements of the application. There is no room for hand work to overcome process flaws, and there is little room for fat design margins to combat uncertainty. These suppliers, and the software embedded in their machines, must perform all of the complex calculating, modeling, simulating and processing that the composites industry has spent the last 50 years developing, and they must do it quickly, flawlessly and seamlessly.
In this way, continuous fiber AM has become the closest thing yet to the elusive and theoretical “composites machine” that the composites industry has notionally envisioned for so long. And it’s the closest thing yet to composites manufacturing standardization. It might be the technology that, finally, helps catapult composites fabrication into the mainstream of manufacturing materials and processes.
Related Content
-
Carbon fiber, bionic design achieve peak performance in race-ready production vehicle
Porsche worked with Action Composites to design and manufacture an innovative carbon fiber safety cage option to lightweight one of its series race vehicles, built in a one-shot compression molding process.
-
Large-format 3D printing enables toolless, rapid production for AUVs
Dive Technologies started by 3D printing prototypes of its composite autonomous underwater vehicles, but AM became the solution for customizable, toolless production.
-
Jeep all-composite roof receivers achieve steel performance at low mass
Ultrashort carbon fiber/PPA replaces steel on rooftop brackets to hold Jeep soft tops, hardtops.