It has been an exciting year for the composites industry and we have been happy to be a part of it. Easing back into travel after almost two years due to the pandemic, this year the CW team was able to visit and report on several manufacturing facilities and the strides they’re making within the industry.
Through a variety of other editorial content like features and digital articles, CW also explored rapidly growing trends and topics that may very well determine the future of the composites industry, such as hydrogen, advanced air mobility (AAM) and sensors. One of the more popular topics this year among our readers appeared to be electric vehicle (EV) battery enclosures. Take a look at the Top 10 CW articles of 2022 and see what you might have missed!
10. Plant tour: Dowty Propellers, Gloucester, U.K.
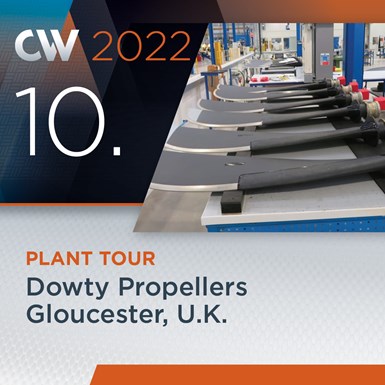
This year, CW had the pleasure of touring Dowty Propellers in Gloucester, U.K., a company that supplies large (e.g., 4-meter-diameter) composite-bladed propellers for commercial and military turboprop aircraft, including the Dash 8-400 regional airliner manufactured by De Havilland Canada (Toronto, Ont., Canada) and the C-130J military transport produced by Lockheed Martin (Bethesda, Md., U.S.).
9. Protocol aims to improve testing of thermal runaway for composite EV battery enclosures
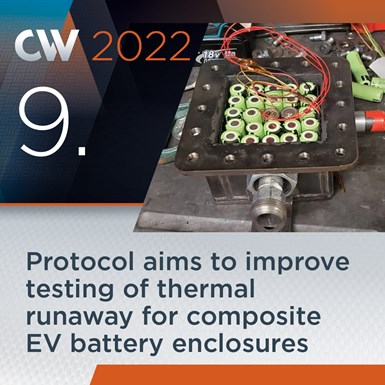
Protective battery enclosures and covers for battery electric vehicles (BEV) represent one of the biggest potential growth areas for composite materials within the automotive market. There are many materials suppliers, composites fabricators and automotive OEMs working in this area, but according to Amanda Nummy, senior polymer materials engineer at Hyundai-Kia America Technical Center (HATCI, Superior Township, Mich., U.S.), the field is still new enough that adequate screening methods for battery enclosure materials do not yet exist.
8. Sensors: Data for next-gen composites manufacturing
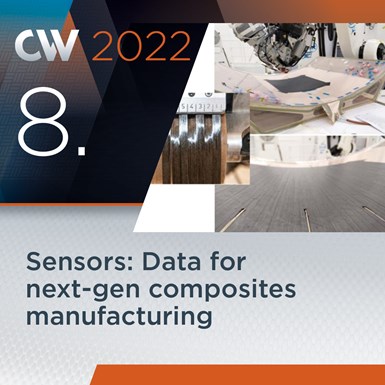
As the global manufacturing industry continues to emerge from the COVID-19 pandemic, it has pivoted to prioritize sustainability, which demands reduction of waste and resource consumption (e.g., energy, water and materials). Thus, manufacturing must become more efficient and intelligent. But this requires information. For composites, where does this data come from?
7. Laser bondline inspection becomes reality
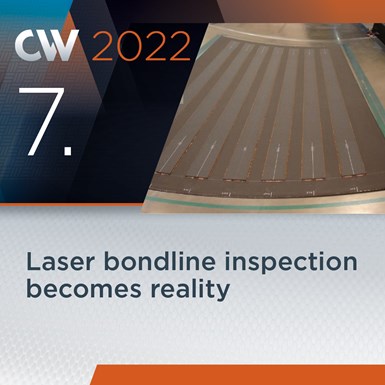
Use of adhesive bonding to assemble composite structures is not new. It’s been widely used in every major end market the composites industry serves, ranging from automotive and marine to wind and defense. In high-performance applications like aerostructures, however, use of unitized, integrated structures has been limited by lack of confidence in the quality of adhesively bonded joints.
6. Multi-material toolbox for cost-effective, scalable EV battery enclosure design
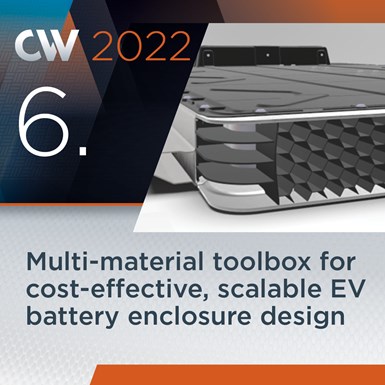
As automakers dive more deeply into the electric vehicle (EV) market, fabricators and Tier suppliers continue to come up with composite solutions for protective battery enclosures. One company taking a multi-material, flexible approach to this design is automotive Tier 1 Katcon (Monterrey, Mexico).
5. Cycling forward with bike frame materials and processes
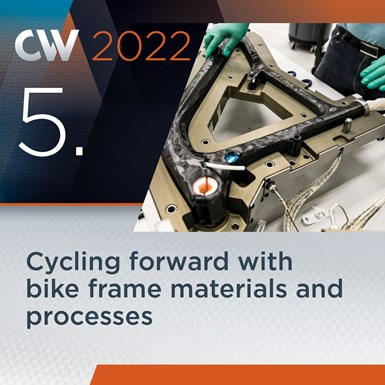
Fine-tuning of conventional materials and processes characterizes today’s carbon fiber-reinforced polymer (CFRP) bicycle frame manufacturing, whether in the large factories of Asia or at reshored facilities in North America and Europe. Thermoplastic resins and automated processes are on the horizon, though likely years away from high-volume production levels.
4. SMC material configurations tailored to automotive battery enclosure design
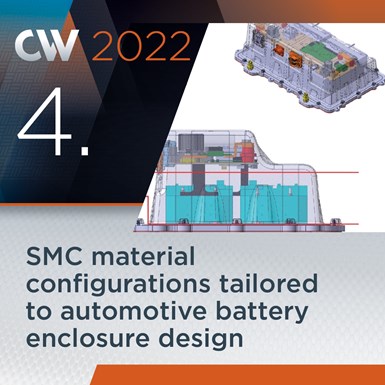
Shifting from internal combustion engines (ICEs) to electric propulsion systems brings benefits like cleaner, greener transportation with less vehicle maintenance, but also numerous challenges. One longstanding issue is finding lighter, more affordable methods to protect battery modules during severe crash events by keeping battery chemistry in place, preventing/containing fires and enabling vehicle occupants to exit and rescue teams to access EVs safely.
3. Price, performance, protection: EV battery enclosures, Part 1
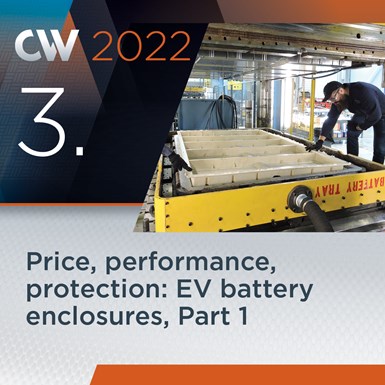
As the automotive industry rapidly electrifies its fleets, interest is growing among OEMs and battery module producers in using composite materials for battery enclosures — covers and trays that hold and protect the frames and battery cells themselves. There are many reasons for this and chief among them is the ability to reduce mass and stack tolerances. Reportedly, empty metallic battery enclosures add 110-160 kilograms to vehicle mass and are now the heaviest component on battery electric vehicles (BEVs) — and that’s before battery packs are loaded. Read here for Part 2.
2. Will the Airbus-CFM H2 flight demonstrator use metal or composite tanks?
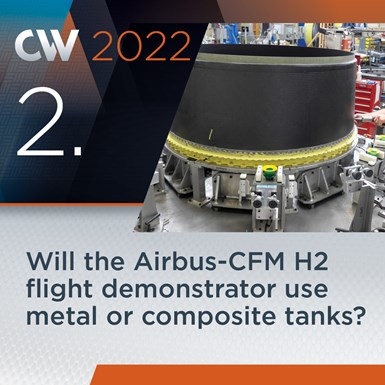
On Feb. 22, 2022, Airbus (Toulouse, France) held a press event to announce its partnership with CFM International (Cincinnati, Ohio, U.S.) to develop and test a hydrogen combustion engine. The program aims to begin flight tests using an Airbus A380 aircraft by 2026, supporting the Airbus ZEROe program goal of a zero emissions (ZEROe) aircraft in service by 2035.
1. Plant tour: Qarbon Aerospace, Milledgeville, Ga. and Red Oak, Texas
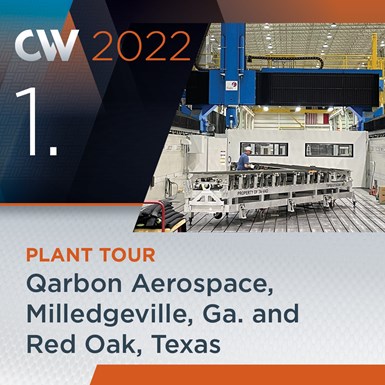
Qarbon Aerospace (Red Oak, Texas, U.S.) is a Tier 1 supplier of composite and metallic aerostructures with 1.6 million square feet of manufacturing space spread across three facilities: 772,000 square feet in its headquarters, 650,000 square feet in Milledgeville, Georgia, and 150,000 square feet in Rayong, Thailand. It is a phoenix, emerging on May 1, 2021, as a stronger private entity, acquired from Triumph Group’s (Berwyn, Pa., U.S.) aerospace structures division by the equity firm Arlington Capital Partners (ACP, Chevy Chase, Md., U.S.).
Related Content
TU Munich develops cuboidal conformable tanks using carbon fiber composites for increased hydrogen storage
Flat tank enabling standard platform for BEV and FCEV uses thermoplastic and thermoset composites, overwrapped skeleton design in pursuit of 25% more H2 storage.
Read MoreSulapac introduces Sulapac Flow 1.7 to replace PLA, ABS and PP in FDM, FGF
Available as filament and granules for extrusion, new wood composite matches properties yet is compostable, eliminates microplastics and reduces carbon footprint.
Read MoreThe lessons behind OceanGate
Carbon fiber composites faced much criticism in the wake of the OceanGate submersible accident. CW’s publisher Jeff Sloan explains that it’s not that simple.
Read MoreThe potential for thermoplastic composite nacelles
Collins Aerospace draws on global team, decades of experience to demonstrate large, curved AFP and welded structures for the next generation of aircraft.
Read MoreRead Next
Mass, cost, durability improvements: EV battery enclosures, Part 2
As interest grows in composite battery covers and trays, composite materials suppliers work to meet current and future needs of automakers, battery module producers.
Read MoreTop 10 CompositesWorld articles of 2021
As this year comes to a close, CompositesWorld is taking some time to reflect on what the year held for those in the composites industry. Take a look at the most popular articles of 2021.
Read MoreVIDEO: High-volume processing for fiberglass components
Cannon Ergos, a company specializing in high-ton presses and equipment for composites fabrication and plastics processing, displayed automotive and industrial components at CAMX 2024.
Read More