Injection overmolded composites demo comes to conclusion
Researchers at the Thermoplastic Composites Research Center in The Netherlands have proved the viability of injection molding a grid-stiffened composite panel.
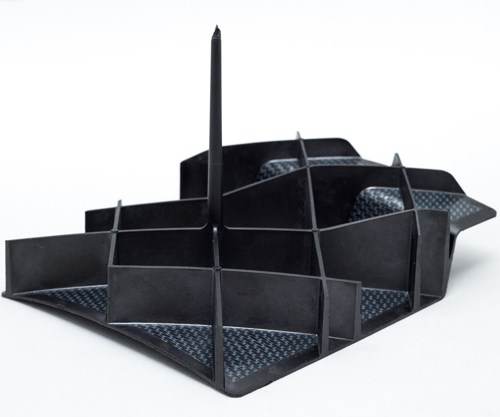
TPRC demonstration part featuring a TenCate Cetex TC1225 carbon fiber/PAEK sheet overmolded with Victrex PEEK90HMF40.
The Thermoplastic Composites Research Center (TPRC, Enschede, The Netherlands) reports that it has successfully closed a two-year collaborative project on the overmolding of thermoplastic composites with the design and manufacture of an advanced demonstrator part. The part was realized as the result of collaboration between TPRC, its members and companies contributing from different areas of expertise: Autodesk, Harper Engineering Co., KraussMaffei, Safran S.A., Samvardhana Motherson Peguform (SMP) and Victrex PLC.
The part features a typical grid-stiffened panel that can be found in larger numbers in aerostructure applications. The stiffness and strength performance combined with extreme dimensional accuracy puts high demands on the manufacturing process.
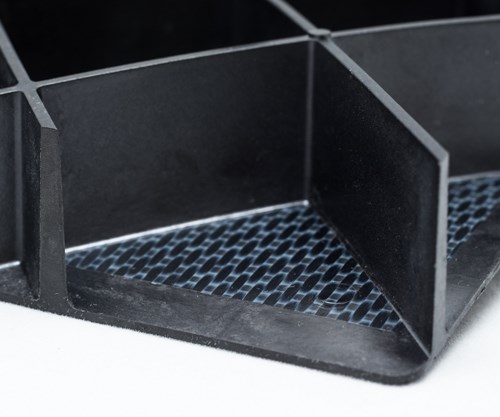
Close-up of the injection overmolded composite part.
The thermoplastic composite insert was press-formed using TenCate Cetex TC1225 engineered carbon fiber/PAEK pre-consolidated sheets and subsequently overmolded with Victrex PEEK90HMF40. The relatively low melting temperature of the composite material enables overmolding with PEEK at moderate insert temperature. The heat of the injected polymer is used to melt the surface of the solid insert upon contact. TPRC says this makes the material combination suitable for a two-step overmolding process.
The overmolding process combines press-forming and injection molding: A continuous fiber-reinforced shell with relatively simple geometry was stiffened with a complex injection molded grid. However, tool design for injection molding is complex, and becomes even more challenging when the process is combined with continuous fiber-reinforced thermoplastics.
TPRC researchers Mark Bouwman, Thijs Donderwinkel and Jeroen Houwers worked on the experimental validation and modelling of the mechanisms underlying the overmolding process. They translated these to numerical models using a thermoforming software package (AniForm) combined with Autodesk Moldflow to predict interface strength and warpage caused by process-induced residual stresses.
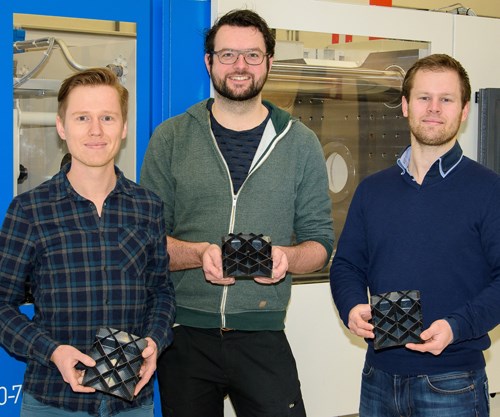
TPRC researchers Thijs Donderwinkel, Jeroen Houwers and Mark Bouwman.
Related Content
-
Daher CARAC TP project advances thermoplastic composites certification approach
New tests, analysis enable databases, models, design guidelines and methodologies, combining materials science with production processes to predict and optimize part performance at temperatures above Tg (≈150-180°C) for wing and engine structures.
-
Queen’s University Belfast presents research in thermoplastic drilling performance optimization
Researchers have published findings from a multi-objective optimization study on carbon fiber-reinforced PEKK drilling in an effort to better understand the material for use in aviation fastenings.
-
Eaton developing carbon-reinforced PEKK to replace aluminum in aircraft air ducts
3D printable material will meet ESD, flammability and other requirements to allow for flexible manufacturing of ducts, without tooling needed today.