Teijin's high-speed composites manufacturing process: Still a mystery
Since Teijin's 60-second carbon fiber molding process was announced in 2011, we've heard little about it. It would be great for the industry if it could bear fruit soon.
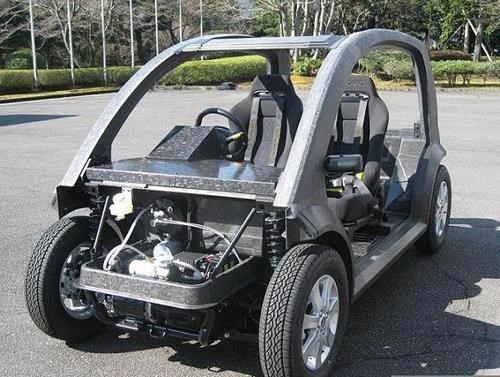
Teijin introduced this passenger cell concept in 2011 to demonstrate the capabilities of its 60-second carbon fiber/thermoplastics manufacturing process. Since then, we've seen and heard little about the process.
In March 2011, carbon fiber manufacturer Teijin (Tokyo, Japan) generated a lot of composites industry buzz when it announced that it had developed a 60-second process for the manufacture of carbon fiber/thermoplastic composite automotive structures. The company reported that the process uses press forming and was based on three intermediate material forms: Unidirectional carbon fiber, isotropic carbon fiber and long fiber thermoplastic pellet.
Then, in December 2011, Teijin announced that it and General Motors (GM) had created a joint venture to work on this high-speed molding process together. Soon after, in early 2012, Teijin opened the doors of the Teijin Composites Application Center (TCAC) in Auburn Hills, Mich., USA, where GM/Teijin joint-venture/co-development work would be done.
Both companies played their cards close to the vest regarding details of the process and its application. In what would prove to be a voluminous discourse on this topic, GM officials told CompositesWorld at the time that the goal was development of a production part: "A timeline for this development process has not been set, GM said, but acknowledged that integration of carbon fiber composites in a production vehicle would require 'from ground up' design and enigneering to optimize material use and minimize weight."
Since then, there has been virtually no information revealed about the Teijin/GM process, and queries by CompositesWorld have gone unanswered. We have, on occasion, run into composites professionals who have been in the TCAC and have seen the process, but are bound by a non-disclosure agreement (NDA). We did, however, enjoy one fact-filled exposition from one person who had knowledge of the process: "The 60-second cycle time is legitimate. Sorry, that's all I can tell you . . ."
Then, about a year ago Teijin reported that this high-speed process had been named Sereebo (Save the Earth, Revolutionary & Evolutionary Carbon) and was being used by Nikon to make structural parts for a digital SLR camera.
Finally, fast-forward to last week (Sept. 16), when a new press release was issued by Teijin. It said, in essence, "We're still working on this process, it's called Sereebo, it's been used by Nikon and our joint venture with General Motors continues." It is, effectively, a press release that says very little. Or, it might say much.
Secrecy and protection of proprietary information is not uncommon in the composites industry. In fact, the composites industry is infamous for its buttoned lips and NDAs — almost every composites fabricator has, or thinks he/she has, a secret sauce of some sort that provides competitive advantage. Teijin and GM certainly deserve much credit for having kept the lid on this process for as long as they have.
The issuing of a say-nothing press release like the one Teijin sent last week might be a way of reminding the market that an important technology is still in the works and is still none of your business. And this might have been prompted by BMW's openess regarding the carbon fiber process it developed for the manufacture of its i3 and i8 cars, which have entered the market to much fanfare over the last year.
What we hope, however, is that Teijin and GM's silence is not indicative of problems with the Sereebo process. The combination of thermoplastics, carbon fiber and compression molding is promising for automotive and getting much attention from a variety of material and equipment suppliers. The composites industry would benefit greatly from a high-speed, thermoplastics-based manufacturing process that uses technology (press molding) that has familiarity in the automotive industry already.
It would be an encouragement to the composites and automotive industries alike if the next Teijin press release announced that Sereebo was being used to mold production parts for a near-future GM car or truck.
Related Content
Natural fiber composites: Growing to fit sustainability needs
Led by global and industry-wide sustainability goals, commercial interest in flax and hemp fiber-reinforced composites grows into higher-performance, higher-volume applications.
Read MoreTU Munich develops cuboidal conformable tanks using carbon fiber composites for increased hydrogen storage
Flat tank enabling standard platform for BEV and FCEV uses thermoplastic and thermoset composites, overwrapped skeleton design in pursuit of 25% more H2 storage.
Read MorePlant tour: Teijin Carbon America Inc., Greenwood, S.C., U.S.
In 2018, Teijin broke ground on a facility that is reportedly the largest capacity carbon fiber line currently in existence. The line has been fully functional for nearly two years and has plenty of room for expansion.
Read MoreBio-based acrylonitrile for carbon fiber manufacture
The quest for a sustainable source of acrylonitrile for carbon fiber manufacture has made the leap from the lab to the market.
Read MoreRead Next
Plant tour: Daher Shap’in TechCenter and composites production plant, Saint-Aignan-de-Grandlieu, France
Co-located R&D and production advance OOA thermosets, thermoplastics, welding, recycling and digital technologies for faster processing and certification of lighter, more sustainable composites.
Read More“Structured air” TPS safeguards composite structures
Powered by an 85% air/15% pure polyimide aerogel, Blueshift’s novel material system protects structures during transient thermal events from -200°C to beyond 2400°C for rockets, battery boxes and more.
Read MoreVIDEO: High-volume processing for fiberglass components
Cannon Ergos, a company specializing in high-ton presses and equipment for composites fabrication and plastics processing, displayed automotive and industrial components at CAMX 2024.
Read More