Bio-based epoxy, recycled materials increase sustainability of all-terrain snowboards
Aiming for a smaller environmental footprint while maintaining high performance, Salomon’s Highpath snowboard line incorporates bio-based epoxy, glass and basalt fiber stringers and recycled materials.
Share
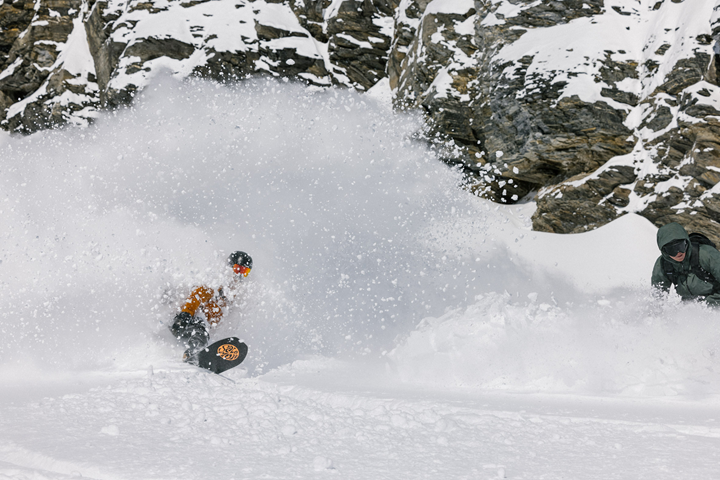
Sporting goods manufacturer Salomon is aiming for more sustainability in its products, and recently evaluated the materials used in its composites-intensive snowboards. Its recent all-terrain Highpath snowboard replaces traditional epoxy with bio-based epoxy and partially recycled materials as a step in this direction. Photo Credit, all images: Salomon
For the 2022-2023 winter sports season, outdoor sports equipment manufacturer Salomon (Annecy, France) set out to design its most sustainable snowboard yet — without sacrificing performance or quality.
The company’s snowboards are manufactured via a wet layup process, including layers of wood core, woven fabric, plastic core and decorative top sheets all combined with a liquid epoxy, followed by press molding for consolidation and cure.
In designing its Highpath all-terrain snowboard line, Salomon evaluated all of the materials used in its boards, looking for opportunities to replace existing materials with recycled or bio-based alternatives while maintaining the board’s performance. For Highpath, this ultimately included introducing 50% recycled polyethylene to the plastic base layer, and 20% recycled aluminum to the board’s outer edges. Other layers include an FSC-certified wood core, biaxial glass and basalt fabric “stringers” that are laid up across the board’s length from tip to tail for added power, a bamboo veneer and a bio-based top sheet made from castor beans.
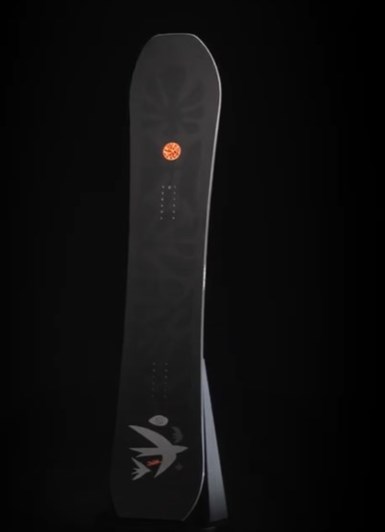
The Highpath is made with a mix of materials, including glass and basalt fiber stringers along the length of the board to increase strength.
For the epoxy that holds everything together, Salomon turned to high-performance epoxy supplier Sicomin (Châteauneuf les Martigues, France). The companies had worked together for more than two years prior to the Highpath snowboard line, with Sicomin supplying small amounts of its bio-based epoxy test materials to Salomon’s R&D lab. Salomon began using Sicomin’s GreenPoxy 28 in some of its production boards in 2022.
What makes GreenPoxy sustainable? According to Sicomin, the main “building block” in an epoxy is epichlorohydrin, used to make epoxy precursor bisphenol A. Instead of typical petrochemical-based sources, GreenPoxy is made from bio-based glycerol obtained as a waste byproduct from oleochemical production. The company claims its strategy is to use the most abundant bio-based raw materials available, guaranteeing industrial volumes while also being as sustainable as possible.
For the Highpath boards, Salomon wanted a drop-in resin replacement that could be proven to match a conventional epoxy’s performance. Sicomin thus carried out extensive testing to ensure that the GreenPoxy 28 resin met the company’s requirements, including, and perhaps most critically, ensuring strong adhesion of all of the multi-material elements of the board. To perform this testing, Sicomin invested in the same climbing drum peel test machine Salomon uses in its own test laboratory, and carried out numerous tests on all Highpath materials to demonstrate that its bio-sourced resin did not cause any drop in mechanical performance compared to a conventional epoxy.
“Our bio-based epoxy resins enable the production of high-performance, environmentally friendly snowboards that resonate with today’s eco-conscious consumers,” says Matthieu Chaloin, export sales technician at Sicomin. “This collaboration is a testament to our ongoing commitment to sustainable innovation and our shared vision for a more sustainable future.”
“Sicomin’s GreenPoxy resins have helped us create our most sustainable all-terrain board without compromising on quality or rideability,” adds Thierry Marion, product manager at Salomon.
Launched to customers in late 2022, the Highpath snowboard line is rated in the “stiff” category among Salomon’s board offerings, and recommended for intermediate and advanced users. It is available in a range of sizes. Because of its mix of bio-based and recycled materials, Highpath is said to be the most sustainable board the company has ever built.
Marion concludes, “The Highpath is a culmination of our efforts to design a high-performance, all-mountain snowboard that paves the way for a more sustainable ride.”
Related Content
Designing an infused, two-piece composite baseball bat
With its Icon BBCOR bat, Rawlings leveraged its experience in braided fabrics and RTM to create an optimized, higher-performance two-piece design.
Read MorePull-wound carbon fiber poles enable lightweight, compact, rigid emergency stretcher
Based on military feedback, Epsilon Composite developed an optimized, foldable stretcher that combines telescopic pull-wound carbon fiber tubes.
Read MoreMulti-material, self-sensing, 3D-printed scoliosis braces
Startup Fited and Brightlands Materials Center have developed a lighter weight, thinner CFRP corrective brace, including pressure sensors made from continuous carbon fibers.
Read MoreUrban furniture project demonstrates green potential for composite 3D printing and recycled materials
Large-format AM specialist Caracol and partners designed custom, 3D-printed outdoor furniture with glass fiber-reinforced recycled polypropylene, and conducted an LCA to evaluate and improve the process.
Read MoreRead Next
Ultra-lightweight skis demonstrate potential of graphene-reinforced composites
With a graphene additive, Folsom Custom Skis evolved and optimized the material makeup of its carbon fiber composite touring skis for higher performance at a lighter weight.
Read MorePlant tour: Daher Shap’in TechCenter and composites production plant, Saint-Aignan-de-Grandlieu, France
Co-located R&D and production advance OOA thermosets, thermoplastics, welding, recycling and digital technologies for faster processing and certification of lighter, more sustainable composites.
Read More“Structured air” TPS safeguards composite structures
Powered by an 85% air/15% pure polyimide aerogel, Blueshift’s novel material system protects structures during transient thermal events from -200°C to beyond 2400°C for rockets, battery boxes and more.
Read More