Composites support Pilatus PC-24 payload capacity, flight range
More than 700 modifications were achieved under the Payload Range Increase Program to deliver increased range, payload and interior comforts.
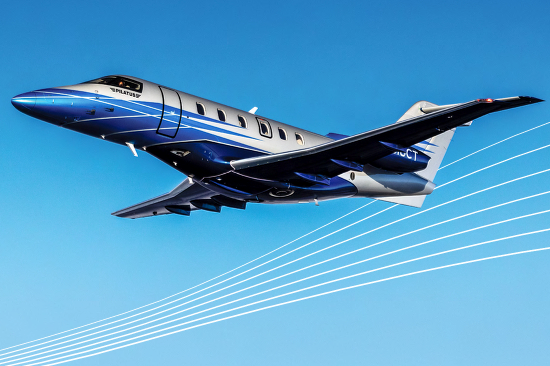
Source | Pilatus Aircraft
Under the Payload Range Increase Program, Pilatus Aircraft Ltd. (Stans, Switzerland) announces that it has developed a version of its PC-24 jet that offers more range and a higher payload while retaining the aircraft’s aerodynamic characteristics and flight handling, in addition to a range of new interior options for customers.
According to the company, the PC-24 contains weight-optimized ground-spoilers and main landing gear doors, as well as new composite ducts and fairings in the rear fuselage. It delivers a payload increase of 272 kilograms (600 pounds). Its maximum range with six passengers on board has also been increased by 370 kilometers to 3,704 kilometers (2,000 nautical miles). With full fuel and single-pilot operation, the maximum payload is 596 kilograms (1,315 pounds). On shorter routes, the jet provides a maximum payload of 1,406 kilograms (3,100 pounds).
Pilatus engineers carried out an extensive campaign of flight tests to expand the entire envelope for the higher design weights. At sea level and maximum takeoff weight, the takeoff distance required is just 941 meters (3,090 feet). “We did what the project name says — ‘Payload Range Increase Program,’ or ‘PRIP’ for short — and focused on increasing the payload capacity and range,” Tobias Waeber, project leader, explains. “At the same time, we wanted to retain the PC-24’s aerodynamic characteristics and flight handling, so that meant no major changes to the external shape. Instead, we concentrated on weight, aiming to increase maximum takeoff weight while also reducing the empty weight. Improvements to the wing and fuselage structure seemed to be the most effective way of increasing the PC-24’s payload and range.” Waeber notes that it will now be possible to transport more luggage and passengers on shorter routes, and on longer routes the crew may be able to avoid a refueling stop.
Nevertheless, like every major project, the PC-24 upgrade was confronted with challenges. “We had to rethink and admit to ourselves that a few modifications simply wouldn’t be enough to achieve our goals,” Waeber says. “We struggled to shave off every gram wherever we could. It was only at the end, when we were able to verify the sum of over 700 modifications to the structure alone, that we realized we had actually exceeded our initial targets.”
Performance became a notable upgrade. As Waeber explains, “on short routes, the PC-24 significantly exceeds the maximum payload of its closest competitors by over 15%, and maximum range with four passengers is slightly better as well. Astonishingly, the PC-24 achieves this with a significantly larger cabin and smaller fuel tanks. And we remain the only aircraft in this class able to operate at so many airfields.”
Besides technical improvements, the interior has been redesigned as well. The noise level in the cabin has been reduced through various optimizations,, such as the ventilation system and engine intake. The cabin interior and welcome center now offer greater flexibility, ergonomics and freedom of movement. There is also additional storage space and a large work surface. The PC-24 also includes a new inflight entertainment system and a large side-facing divan seating arrangement option.
All PC-24s from serial number 501 onward will also feature a new function enabling the provision of predictive maintenance services. Immediately after landing, aircraft data will be forwarded to Pilatus for analysis and, if required, a predictive maintenance recommendation can be made to the operator.
Related Content
Welding is not bonding
Discussion of the issues in our understanding of thermoplastic composite welded structures and certification of the latest materials and welding technologies for future airframes.
Read MoreCryo-compressed hydrogen, the best solution for storage and refueling stations?
Cryomotive’s CRYOGAS solution claims the highest storage density, lowest refueling cost and widest operating range without H2 losses while using one-fifth the carbon fiber required in compressed gas tanks.
Read MoreNext-generation airship design enabled by modern composites
LTA Research’s proof-of-concept Pathfinder 1 modernizes a fully rigid airship design with a largely carbon fiber composite frame. R&D has already begun on higher volume, more automated manufacturing for the future.
Read MorePlant tour: Joby Aviation, Marina, Calif., U.S.
As the advanced air mobility market begins to take shape, market leader Joby Aviation works to industrialize composites manufacturing for its first-generation, composites-intensive, all-electric air taxi.
Read MoreRead Next
FAA investigates fresh concerns over 787 aircraft production
A Boeing engineer has claimed that the Dreamliner’s composite fuselage assembly process is flawed, raising questions about the aircraft’s structural integrity.
Read MoreStrata Manufacturing delivers first Pilatus PC-24 flap track fairings shipset
This delivery marks the initial success of an expanded agreement between Strata and Pilatus announced in May 2019.
Read MoreGulfstream G700 composite business jet earns FAA certification
All-new aircraft is now type certified with even more performance enhancements, paving the way for customer deliveries.
Read More