Daimler AG, Volvo Group to form JV for large-scale production of fuel cells
The companies plan to form a 50/50 joint venture for development and large-scale production of fuel cells for heavy-duty vehicles.

Assembly line for a fuel cell drive unit in Kirchheim-Nabern. The tightness of all the connections is checked once again for good measure. The circulation systems for the hydrogen, the air and the coolant are all checked. Source | Daimler
Daimler Truck AG (Stuttgart, Germany) and the Volvo Group (Gothenburg, Sweden) have signed what they report is a preliminary, non-binding agreement to establish a new joint venture to develop, produce and commercialize fuel cell systems for heavy-duty vehicle applications and other use cases. As part of the joint venture, Daimler will consolidate all its current fuel cell activities in the joint venture. The Volvo Group will acquire 50% in the joint venture for the sum of approximately €0.6 billion on a cash and debt-free basis.
According to the partners, in the context of the current economic downturn, cooperation has become even more necessary in order to meet Europe’s Green Deal objectives within a feasible time-frame. This includes aiming for sustainable transport and a carbon neutral Europe by 2050.
The goal is for both companies to offer heavy-duty vehicles with fuel cells for demanding long-haul applications in series production by the second half of the decade. Other automotive and non-automotive use cases will also be evaluated.
“Transport and logistics keep the world moving, and the need for transport will continue to grow. Truly CO2-neutral transport can be accomplished through electric drive trains with energy coming either from batteries or by converting hydrogen on board into electricity. For trucks to cope with heavy loads and long distances, fuel cells are one important answer and a technology where Daimler has built up significant expertise through its Mercedes-Benz fuel cell unit over the last two decades. This joint initiative with the Volvo Group is a milestone in bringing fuel cell-powered trucks and buses onto our roads,” says Martin Daum, chairman of the Board of Management Daimler Truck AG and member of the Board of Management of Daimler AG.
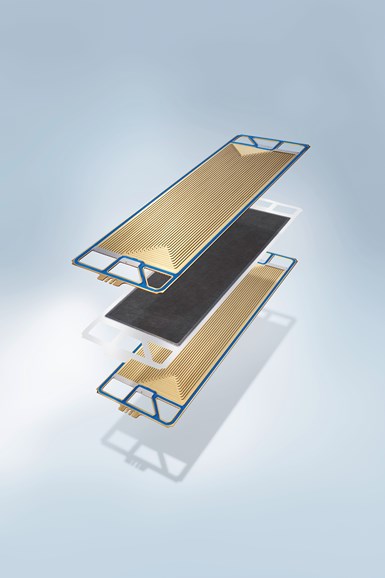
The PEM fuel cell is structured like a sandwich. In the center is a thin plastic film coated on both sides with a thin catalyst layer and a gas permeable electrode made of graphite paper. The membrane is surrounded by two bipolar plates into which gas ducts have been milled. Through these gas ducts flows hydrogen on the one side, and oxygen on the other. Several of these individual fuel cells can be stacked one behind the other to create a fuel cell stack. Source | Daimler
The Volvo Group and Daimler Truck AG will be 50/50 partners in the joint venture, which will operate as an independent and autonomous entity, with Daimler Truck AG and the Volvo Group continuing to be competitors in all other areas of business. Joining forces will decrease development costs for both companies and accelerate the market introduction of fuel cell systems in products used for heavy-duty transport and demanding long-haul applications.
To enable the joint venture, Daimler Trucks is bringing together all group-wide fuel cell activities in a new Daimler Truck fuel cell unit. Part of this bundling of activities is the allocation of the operations of “Mercedes-Benz Fuel Cell GmbH,” which has longstanding experience in the development of fuel cell and hydrogen storage systems for various vehicle applications, to Daimler Truck AG.
The joint venture will include the operations in Nabern/Germany (currently headquarters of the Mercedes-Benz Fuel Cell GmbH) with production facilities in Germany and Canada.
A final agreement is expected by Q3 and closing before year-end 2020. All potential transactions are subject to examination and approval by the responsible competition authorities.
“… Using hydrogen as a carrier of green electricity to power electric trucks in long-haul operations is one important part of the puzzle, and a complement to battery electric vehicles and renewable fuels. Combining the Volvo Group and Daimler’s experience in this area to accelerate the rate of development is good both for our customers and for society as a whole. By forming this joint venture, we are clearly showing that we believe in hydrogen fuel cells for commercial vehicles. But for this vision to become reality, other companies and institutions also need to support and contribute to this development, not least in order to establish the fuel infrastructure needed,” says Martin Lundstedt, Volvo Group president and CEO.
Related Content
Cryo-compressed hydrogen, the best solution for storage and refueling stations?
Cryomotive’s CRYOGAS solution claims the highest storage density, lowest refueling cost and widest operating range without H2 losses while using one-fifth the carbon fiber required in compressed gas tanks.
Read MoreCo-molding SMC with braided glass fiber demonstrates truck bed potential
Prepreg co-molding compound by IDI Composites International and A&P Technology enables new geometries and levels of strength and resiliency for automotive, mobility.
Read MoreCarbon fiber, bionic design achieve peak performance in race-ready production vehicle
Porsche worked with Action Composites to design and manufacture an innovative carbon fiber safety cage option to lightweight one of its series race vehicles, built in a one-shot compression molding process.
Read MoreInfinite Composites: Type V tanks for space, hydrogen, automotive and more
After a decade of proving its linerless, weight-saving composite tanks with NASA and more than 30 aerospace companies, this CryoSphere pioneer is scaling for growth in commercial space and sustainable transportation on Earth.
Read MoreRead Next
All-recycled, needle-punched nonwoven CFRP slashes carbon footprint of Formula 2 seat
Dallara and Tenowo collaborate to produce a race-ready Formula 2 seat using recycled carbon fiber, reducing CO2 emissions by 97.5% compared to virgin materials.
Read More“Structured air” TPS safeguards composite structures
Powered by an 85% air/15% pure polyimide aerogel, Blueshift’s novel material system protects structures during transient thermal events from -200°C to beyond 2400°C for rockets, battery boxes and more.
Read MorePlant tour: Daher Shap’in TechCenter and composites production plant, Saint-Aignan-de-Grandlieu, France
Co-located R&D and production advance OOA thermosets, thermoplastics, welding, recycling and digital technologies for faster processing and certification of lighter, more sustainable composites.
Read More