Eaton Aerospace qualifies new VITA system, increases satellite payload capacity
Aerospace industry-first valve in tank assembly (VITA) propulsion feed system integrates valves inside a composite propellant tank, increasing payload capacity and reducing considerable rework efforts.
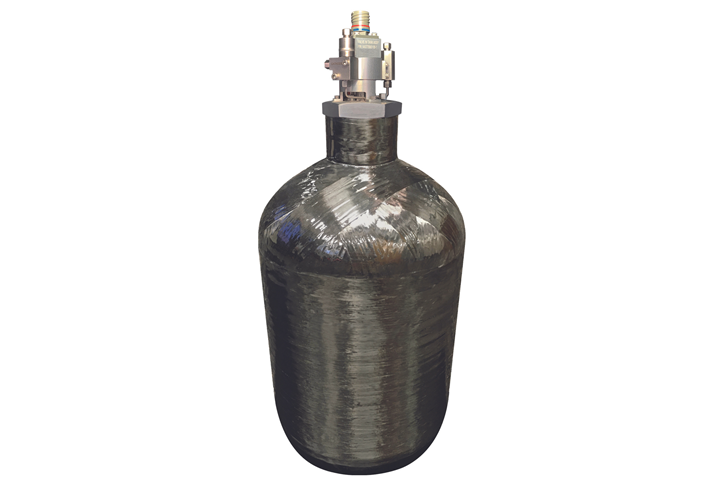
Valve in tank assembly (VITA). Photo Credit: Eaton Aerospace
Power management company Eaton Aerospace (Cleveland, Ohio, U.S.) announced on Aug. 23 that its successfully completed qualification testing for what is claims is the aerospace industry’s first valve in tank assembly (VITA) propulsion feed system. As a satellite electric propulsion solution that integrates valves inside the composite propellant tank, the VITA eliminates the need for a traditional feed system envelope, creating room for more payload. Eaton Aerospace is officially launching the VITA system at Space Symposium this week.
“Our VITA can help transform the satellite industry,” says Craig Ryan, integrated product team director, Space Systems, Eaton’s Aerospace Group. “The efficient design of the VITA feed system requires less space on the satellite bus, plus it saves integrators significant procurement, assembly, testing, troubleshooting and rework effort.”
According to the company, VITA will play a critical role in helping propel satellites to final orbit and in station-keeping to maintain orbital position. By enabling additional payload flexibility and control over which type of fuel can be included on a satellite mission, the VITA design supports the growing satellite industry, especially in the highly competitive area of small satellite providers.
“We have the infrastructure to quickly meet high demand volume and are currently taking orders,” says Ryan. “We look forward to supporting the success of a wide range of leaders and emerging innovators in the rapidly growing satellite market.”
The design of Eaton’s VITA eliminates the feed system envelope by integrating proportional flow valve technology into a housing that is then integrated into the neck of a lightweight composite propellant tank which uses an aluminum liner with carbon fiber overwrap. The initial configuration of the VITA solution has two redundant shut-off valves to support one thruster for increased reliability. The drop-in VITA design approach supports modular satellite configurations, making architectural changes easier. Qualified in testing with xenon, this system has demonstrated to be fully compatible with krypton as well. The valve and tank assembly can be pre-filled with propellant and shipped ready to install.
Related Content
-
Aurora reveals latest SPRINT X-Plane design concept
An Aurora and Boeing team advances its high-speed, vertical lift concept to the preliminary design phase, which features three lift fans, a more refined composite exterior and an uncrewed cockpit.
-
Nine factors to consider when designing composites cure tooling
Gary Bond discusses the common pitfalls and compromises when designing good cure tooling and their holistic significance for a robust composite production process.
-
Composite sidewall cover expands options for fire-safe rail components
R&D project by CG Rail explores use of carbon fiber-reinforced thermoplastics and recycled manufacturing scrap to meet fire safety, weight and volume targets.