Fortify launches photopolymer 3D printing system
The Continuous Kinetic Mixing (CKM) system combines fiber or particle additive reinforcement to photopolymers for electrical applications and more.
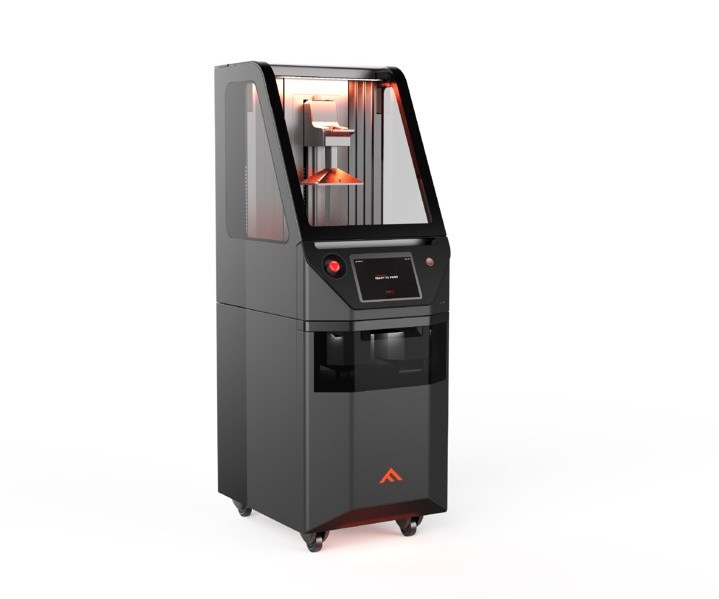
Source | Fortify
3D printing startup Fortify (Boston, Mass., U.S.) announced on March 19 the launch of its Continuous Kinetic Mixing (CKM) system, allowing for new functionality in 3D-printed photopolymers. Fortify says that its new system meets an industry need for advanced material properties in additive manufacturing, and has been developed to address long-standing industry challenges in processing filled resins.
Read more about Fortify’s magnetic 3D printing process here.
Fortify claims to be the first company to implement fiber and particle additive reinforcing techniques in injection molding with 3D-printed photopolymers. According to Fortify, CKM ensures that additives stay uniformly distributed throughout the material while mitigating sedimentation and aggregation.
“Developing Continuous Kinetic Mixing was an integral part of Fortify’s strategy. It will play a critical role in manufacturing functional parts,” says Josh Martin, Fortify CEO and co-founder.
The CKM process incorporates additives to enhance mechanical performance such as strength, stiffness, toughness, wear and heat deflection temperature, as well as thermal and electrical properties. Fortify’s platform aims to combine the scalability, resolution and surface quality of photopolymers with the performance expectations of traditional high-performance polymers.
“Our team takes a comprehensive approach to developing additive solutions,” Martin adds. “In addition to advanced hardware and software systems, Fortify innovates within materials science to process viscous, heavily loaded polymers. This new class of material is well suited for high-performance applications.”
Fortify has recently expanded its portfolio to include metal injection molding. In this application, ceramic fibers are blended with resin to manufacture tooling that can withstand the extreme temperatures and pressures of the molding process.
“For years our customers have been asking us for a better way to prototype parts with our production metal injection molding process. Speed, dimensional accuracy and production intent processes are critical for our customer’s development efforts,” says Chris Aiello, technical sales manager at Alpha Precision Group. “Fortify finally showed us a tooling solution that holds up to our MIM process, and checks all the boxes for our customers requirements.”
Fortify says its products are being applied to the electrical and communications industrys, leveraging the company’s ability to combine strength with tune-able dielectrics in complex shapes.
“Material properties are a key factor driving adoption of Additive Manufacturing,” says Ken Kisner, global head of innovation and 3D printing at Henkel Adhesive Technologies, and founder of Molecule Corp. “Fortify’s on-board mixing technology is an important step toward satisfying this need. This is a very exciting piece of technology that will open up significant applications across industries.”
Fortify has also recently moved into a new Boston headquarters with increased printing and manufacturing capacity, and is planning to ship machines to select customers this summer.
Related Content
-
3D-printed CFRP tools for serial production of composite landing flaps
GKN Aerospace Munich and CEAD develop printed tooling with short and continuous fiber that reduces cost and increases sustainability for composites production.
-
PEEK vs. PEKK vs. PAEK and continuous compression molding
Suppliers of thermoplastics and carbon fiber chime in regarding PEEK vs. PEKK, and now PAEK, as well as in-situ consolidation — the supply chain for thermoplastic tape composites continues to evolve.
-
Jeep all-composite roof receivers achieve steel performance at low mass
Ultrashort carbon fiber/PPA replaces steel on rooftop brackets to hold Jeep soft tops, hardtops.