Solvay to supply advanced composites, adhesives for space exploration
Ablative material, RTM resins and adhesives will be applied to a range of ESA space programs, including Avio’s Vega family of satellite launch vehicles.
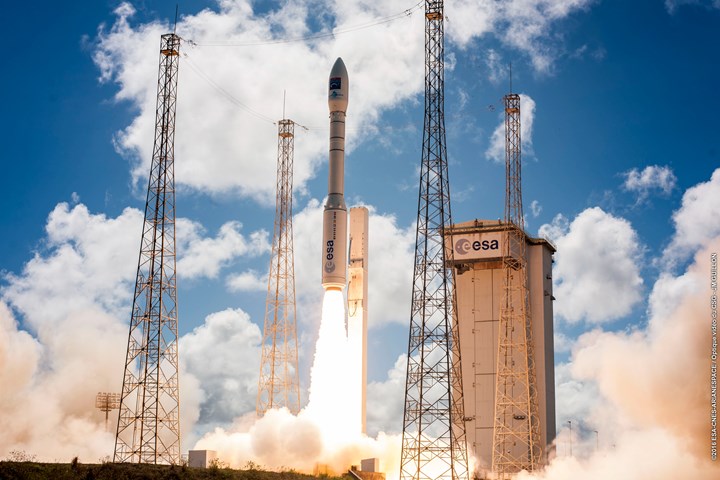
Photo Credit: Solvay, PR016
Solvay (Alpharetta, Ga., U.S.) and space propulsion company Avio SpA (Rome, Italy) have signed a long-term agreement for the supply of composite and adhesive materials to be used across a range of programs including the Vega space programs, the European Space Agency’s (ESA) satellite launch vehicles designed to send payloads into low-Earth orbit (LEO).
Solvay will supply Avio with ablative material, resin transfer molding (RTM) resins and adhesives. Solvay notes that it has a strong legacy in the space market — its products have been used across many space launch programs over the years due to their ability to withstand the extremely high temperatures produced by rocket motor exhaust. Ablative materials are just one example, which have been applied to several space applications from nozzles to exit cones.
Alternately, Avio has more than 50 years of history designing, developing, producing and integrating space launchers to place institutional, governmental and commercial payloads in LEO through its Vega rocket family.
“We are excited to extend our partnership with industry leader Avio and continue to support Vega-critical missions,” says Carmelo Lo Faro, president of Solvay’s Materials Segment. “We are all currently seeing renewed enthusiasm and investment in the global space race and we believe that our advanced materials will be key enablers for space exploration, space tourism and also the launch placement of satellite constellations. We helped put the first man on the moon and will be there for the first woman on Mars.”
Sergio Colabucci, Avio procurement director adds that the long-term agreement secures the supply of strategic products for its Vega family launchers in upcoming years.
Related Content
-
Infinite Composites: Type V tanks for space, hydrogen, automotive and more
After a decade of proving its linerless, weight-saving composite tanks with NASA and more than 30 aerospace companies, this CryoSphere pioneer is scaling for growth in commercial space and sustainable transportation on Earth.
-
Welding is not bonding
Discussion of the issues in our understanding of thermoplastic composite welded structures and certification of the latest materials and welding technologies for future airframes.
-
Cryo-compressed hydrogen, the best solution for storage and refueling stations?
Cryomotive’s CRYOGAS solution claims the highest storage density, lowest refueling cost and widest operating range without H2 losses while using one-fifth the carbon fiber required in compressed gas tanks.