Stratolaunch completes second TA-0 captive carry flight
The ongoing flight test program continues on target towards separation test and the first hypersonic flight of TA-1 within the first half of 2023.
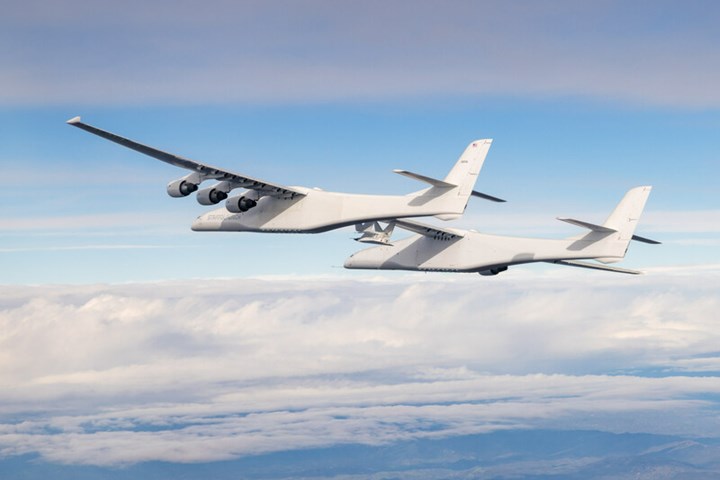
Photo Credit: Gauntlet Aerospace/Christian Turner
Reported by Airframer.com, Stratolaunch (Mojave, Calif., U.S.) successfully completed its second captive carry flight (CW reported on the first in November 2022) with the Talon-A separation test vehicle, TA-0. This marks the ninth flight for the company’s all-composite, twin fuselage, low Earth orbit (LEO)-capable launch platform, Roc.
Airframer.com notes that the flight “set a new duration record lasting a total of six hours and reached a maximum altitude of 22,500 feet.” Primary test objectives included flying outside of the local Mojave area for the first time and the evaluation of the separation environment. Onboard data systems on Roc and TA-0 are said to have provided the company critical information regarding aerodynamic loads and moments prior to TA-0’s release, helping to ensure safe separation of the vehicle from Roc. The flight team also practiced chase formation and communication sequencing for the upcoming separation test.A flight data review will determine the next steps on the test timeline.
In November 2022, Stratolaunch also received a contract with the U.S. Air Force Research Laboratory (AFRL, Wright-Patterson Air Force Base, Ohio, U.S.) to support the flight test of the company’s first expendable Talon-A hypersonic test vehicle, TA-1. Stratolaunch anticipates flying the vehicle in the first quarter of 2023.
The first Talon-A vehicle is an expendable configuration. The next generation of Talon-A vehicles will be capable of reusable hypersonic flight.
Related Content
-
Combining multifunctional thermoplastic composites, additive manufacturing for next-gen airframe structures
The DOMMINIO project combines AFP with 3D printed gyroid cores, embedded SHM sensors and smart materials for induction-driven disassembly of parts at end of life.
-
Welding is not bonding
Discussion of the issues in our understanding of thermoplastic composite welded structures and certification of the latest materials and welding technologies for future airframes.
-
Manufacturing the MFFD thermoplastic composite fuselage
Demonstrator’s upper, lower shells and assembly prove materials and new processes for lighter, cheaper and more sustainable high-rate future aircraft.