U.K.’s first wind turbine blade recycling pilot project secures funding
The £2 million, three-year project aims to ensure global wind and composites sustainability via commercialization of a novel method of separating glass fiber reinforcements from its resin system.
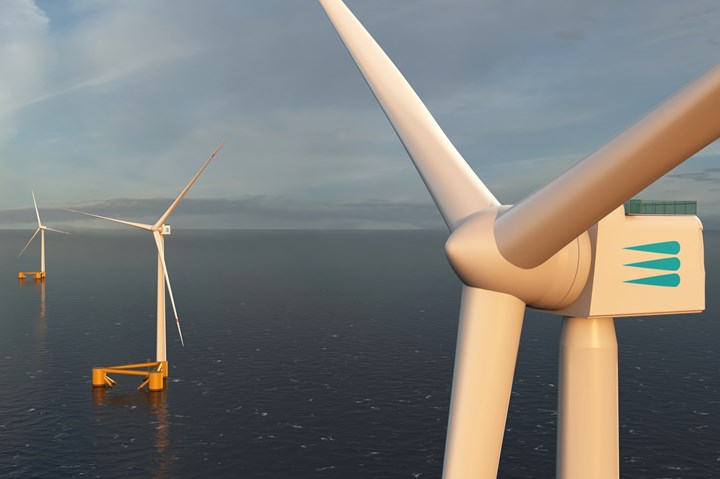
Photo Credit: Composites UK
Trade body Composites UK (Berkhamsted, U.K.) announces its involvement in a new major project to develop wind turbine blade recycling in the U.K., which has officially been given the go-ahead after the project proposal won a UK Government grant, as well as the contribution of more than £500,000 by project lead Aker Offshore Wind (Lysaker, Norway).
The £2 million, three-year project involves a consortium that also includes researchers from the University of Strathclyde’s (Scotland) Advanced Composites Group and Lightweight Manufacturing Centre, the University of Nottingham, global waste management firm Suez (Paris, France), composite distributor GRP Solutions (Havant, U.K.) and composite part manufacturer Cubis (Armagh, Ireland). The primary aim of the pilot project is to ensure a more sustainable future for the global wind industry and the wider composites manufacturing industry — all of which will ultimately accelerate the drive towards net zero emissions and waste, and create new skills and job opportunities in the U.K.
The project is set up to commercialize a novel method developed by the University of Strathclyde to separate the glass fiber and resin components in composites and recover the fiber reinforcement, which can then be reprocessed, molded and reused in other industries, such as the motor trade and the construction industry.
“Wind energy is a key component of the transition to net zero and it is essential that the technology and materials that provide renewable energy are as sustainable as they can be,” notes Strathclyde Principal Professor Sir Jim McDonald. “As we have seen at COP26 [2021 United Nations Climate Change Conference] in Glasgow, a global move to renewable, sustainable sources of energy will help to make some of the biggest advances in the quest to tackle climate change. At Strathclyde, we have developed novel processes for recycling and reusing wind turbine blades, which will help to reduce waste in the renewables sector and wider industry.”
According to project partners, the environmental benefits from this project cannot be understated. Waste from wind turbine blades alone are expected to reach around 2 million tonnes globally by 2050, and the U.K. volumes of composite waste already exceed 100,000 tonnes per year. Aker Offshore Wind has pledged its support to trade body WindEurope’s call for a Europe-wide landfill ban on decommissioned wind turbine blades by 2025 and considers this project a crucial step towards setting a new standard for the industry.
“Composite materials combining glass fiber and polymer resin systems have a huge role to play in enabling the U.K. economy to transition to net zero and we need effective recycling at end of life [EOL] to ensure that composite materials achieve high levels of circularity in future,” concludes Malcolm Forsyth, sustainability manager at Composites UK and overall project leader.
Related Content
-
MingYang reveals 18-MW offshore wind turbine model with 140-meter-long blades
The Chinese wind turbine manufacturer surpasses its 16-MW platform, optimizes wind farm construction costs for 1-GW wind farms.
-
Composites end markets: Automotive (2024)
Recent trends in automotive composites include new materials and developments for battery electric vehicles, hydrogen fuel cell technologies, and recycled and bio-based materials.
-
Composites end markets: Pressure vessels (2024)
The market for pressure vessels used to store zero-emission fuels is rapidly growing, with ongoing developments and commercialization of Type 3, 4 and 5 tanks.