NREL explores novel manufacturing approach for next-generation wind turbine blades
3D printing of thermoplastic blades enables thermal welding and improves recyclability, offering the potential to reduce turbine blade weight and cost by at least 10%, and production cycle time by 15%.
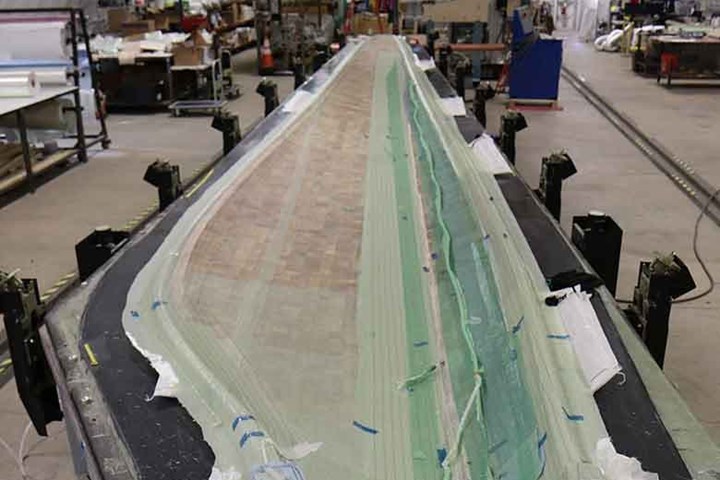
Using the Composites Manufacturing Education and Technology Facility (CoMET), an NREL research team built a 13-meter thermoplastic blade to innovate wind turbine blade manufacturing. Photo Credit: Ryan Beach, NREL
A team of National Renewable Energy Laboratory (NREL, Golden, Colo., U.S.) researchers, led by NREL senior wind technology engineer Derek Berry, are continuing to advance their novel techniques to manufacture advanced wind turbine blades by furthering their combination of recyclable thermoplastics and additive manufacturing (AM). The advance was made possible by funding from the U.S. Department of Energy’s Advanced Manufacturing Office — awards designed to stimulate technology innovation, improve the energy productivity of U.S. manufacturing and enable the manufacturing of cutting-edge products.
Today, most utility-scale wind turbine blades have the same clamshell design: Two fiberglass blade skins are bonded together with adhesive and use one or several composite stiffening components called shear webs, a process optimized for efficiency over the past 25 years. However, to make wind turbine blades lighter, longer, less expensive and more efficient at capturing wind energy — improvements critical to the goal of cutting greenhouse gas emissions in part by increasing wind energy production — researchers must entirely rethink the conventional clamshell, something that is the NREL team’s primary focus.
To start, the NREL team is focusing on the resin matrix material. Current designs rely on thermoset resin systems like epoxies, polyesters and vinyl esters, polymers that, once cured, cross-link like brambles.
“Once you produce a blade with a thermoset resin system, you cannot reverse the process,” Berry says. “That [also] makes the blade difficult to recycle.”
Working with the Institute for Advanced Composites Manufacturing Innovation (IACMI, Knoxville, Tenn., U.S.) in NREL’s Composites Manufacturing Education and Technology (CoMET) Facility, the multi-institution team developed systems that use thermoplastics, which, unlike thermoset materials, can be heated to separate the original polymers, enabling end-of-life (EOL) recyclability.
Thermoplastic blade parts can also be joined using a thermal welding process that could eliminate the need for adhesives — often heavy and expensive materials — further enhancing blade recyclability.
“With two thermoplastic blade components, you have the ability to bring them together and, through the application of heat and pressure, join them,” Berry says. “You cannot do that with thermoset materials.”
Moving forward, NREL, along with project partners TPI Composites (Scottsdale, Ariz., U.S.), Additive Engineering Solutions (Akron, Ohio, U.S.), Ingersoll Machine Tools (Rockford, Ill., U.S.), Vanderbilt University (Knoxville) and IACMI, will develop innovative blade core structures to enable the cost-efficient production of high-performance, very long blades — well over 100 meters in length — that are relatively low weight.
By using 3D printing, the research team says it can produce the kinds of designs needed to modernize turbine blades with highly engineered, net-shaped structural cores of varying densities and geometries between the structural skins of the turbine blade. The blade skins will be infused using a thermoplastic resin system.
If they succeed, the team will reduce turbine blade weight and cost by 10% (or more) and production cycle time by at least 15%.
In addition to the prime AMO FOA award for AM thermoplastic wind turbine blade structures, two subgrant projects will also explore advanced wind turbine manufacturing techniques. Colorado State University (Fort Collins) is leading a project that also uses 3D printing to make fiber-reinforced composites for novel internal wind blade structures, with Owens Corning (Toledo, Ohio, U.S.), NREL, Arkema Inc. (King of Prussa, Pa., U.S.), and Vestas Blades America (Brighton, Colo., U.S.) as partners. The second project, led by GE Research (Niskayuna, N.Y., U.S.), is dubbed AMERICA: Additive and Modular-Enabled Rotor Blades and Integrated Composites Assembly. Partnering with GE Research are Oak Ridge National Laboratory (ORNL, Oak Ridge, Tenn., U.S.), NREL, LM Wind Power (Kolding, Denmark) and GE Renewable Energy (Paris, France).
Related Content
NCC reaches milestone in composite cryogenic hydrogen program
The National Composites Centre is testing composite cryogenic storage tank demonstrators with increasing complexity, to support U.K. transition to the hydrogen economy.
Read MoreUpdate: THOR project for industrialized, recyclable thermoplastic composite tanks for hydrogen storage
A look into the tape/liner materials, LATW/recycling processes, design software and new equipment toward commercialization of Type 4.5 tanks.
Read MoreComposites end markets: Automotive (2024)
Recent trends in automotive composites include new materials and developments for battery electric vehicles, hydrogen fuel cell technologies, and recycled and bio-based materials.
Read MoreDrag-based wind turbine design for higher energy capture
Claiming significantly higher power generation capacity than traditional blades, Xenecore aims to scale up its current monocoque, fan-shaped wind blades, made via compression molded carbon fiber/epoxy with I-beam ribs and microsphere structural foam.
Read MoreRead Next
“Structured air” TPS safeguards composite structures
Powered by an 85% air/15% pure polyimide aerogel, Blueshift’s novel material system protects structures during transient thermal events from -200°C to beyond 2400°C for rockets, battery boxes and more.
Read MoreAll-recycled, needle-punched nonwoven CFRP slashes carbon footprint of Formula 2 seat
Dallara and Tenowo collaborate to produce a race-ready Formula 2 seat using recycled carbon fiber, reducing CO2 emissions by 97.5% compared to virgin materials.
Read MoreDeveloping bonded composite repair for ships, offshore units
Bureau Veritas and industry partners issue guidelines and pave the way for certification via StrengthBond Offshore project.
Read More