Whitewater Technology debuts high-performance, recycled carbon fiber paddle range
Paddles consist of high-impact, non-woven composite that combines 40% recycled carbon fiber with a thermoplastic resin system and an aramid puncture-resistant layer for identical weight, strength and stiffness properties to non-recycled products.
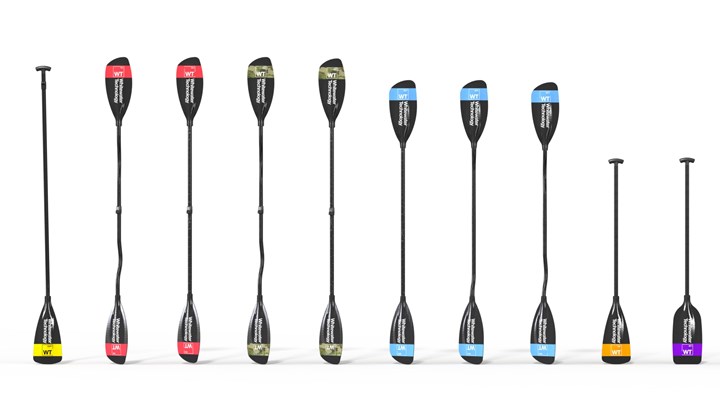
Photo Credit: Whitewater Technology
Whitewater Technology (WT, Greenville, S.C., U.S.), part of the C12 Technology Group, launched in late October it’s debut paddle range featuring high-performance paddles made with 100% recycled carbon fiber.
The range, which features paddles for all disciplines, was designed by leading advanced materials engineer and whitewater kayaker Ollie Wainwright. Using his composites background in the motorsports industry, WT’s first paddles are the result of two years of intensive R&D into the use of recycled carbon fiber in high-performance outdoor and sporting goods.
“As both a serious paddler and materials engineer I had grown frustrated with the lack of a sustainable high-performance paddle option. We’re out there in nature every weekend using a product that ultimately ends up in landfill... so a few years ago we set out to try and change this,” says Wainwright. He acknowledges that he’s pleased with the results and what the WT has been able to accomplish with the sustainable composites’ design.
WT’s paddles reportedly use a custom-made, high-impact, non-woven composite that combines 40% recycled carbon fiber with a thermoplastic resin system and an aramid puncture-resistant layer. The result is a high-performance paddle with identical weight, strength and stiffness properties to a non-recycled product.
Available initially as a pre-order via the WT website in addition to specialty retailers, the range includes paddles for whitewater, touring, fishing, SUP, rafting and canoe with a variety of adjustable length and shaped shafts.
Pre-sale pricing starts at $240 including free shipping, five-year warranty and crash replacement.
Related Content
-
Composites manufacturing for general aviation aircraft
General aviation, certified and experimental, has increasingly embraced composites over the decades, a path further driven by leveraged innovation in materials and processes and the evolving AAM market.
-
Plant tour: Airbus, Illescas, Spain
Airbus’ Illescas facility, featuring highly automated composites processes for the A350 lower wing cover and one-piece Section 19 fuselage barrels, works toward production ramp-ups and next-generation aircraft.
-
Manufacturing the MFFD thermoplastic composite fuselage
Demonstrator’s upper, lower shells and assembly prove materials and new processes for lighter, cheaper and more sustainable high-rate future aircraft.