WMG prototypes CFRP frame for Very Light Rail (VLR) demonstration vehicle
Braided thermoplastic composite frame enables lightweight, recyclability and high-volume manufacturing.
Share
Read Next
Revolution VLR is a consortium in the U.K. — led by Transport Design International Ltd (TDI, Stratford upon Avon) — which won funding in 2013 to develop a self-powered rail bogie with an integral, hybrid propulsion system. TDI believes that designing lighter “light rail” vehicles — i.e., very light rail (VLR) — is crucial for providing the next generation of sustainable public transport. In phase 2 of the VLR project, a complete 18-meter-long diesel-battery demonstrator vehicle will be available for testing in 2020.
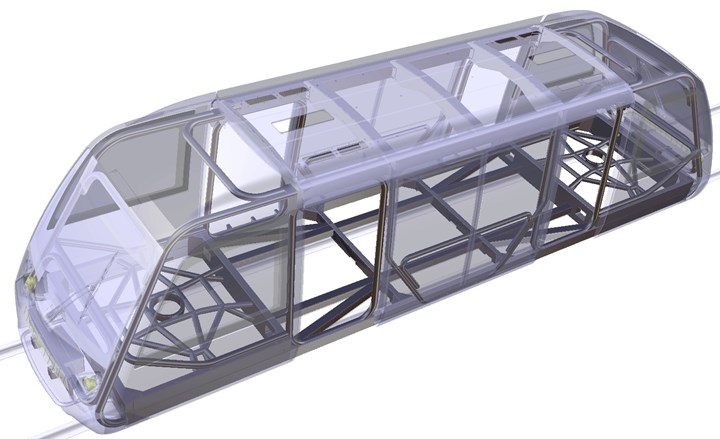
The Very Light Rail (VLR) demonstrator is an 18-meter-long bogie with integrated diesel-battery hybrid propulsion system and a lightweight chassis made from braided composite tubes. SOURCE | University of Warwick.
An original member of Revolution VLR, WMG at the University of Warwick has developed a carbon fiber reinforced plastic (CFRP) frame for this demonstration VLR vehicle. WMG is a long-time supporter of composites, with initiatives such as the National Automotive Innovation Centre, the Materials Engineering Centre and the International Institute for Nanocomposites Manufacturing. WMG’s partners for this “BRAINSTORM VLR” project include TDI, the UK Government’s Innovate UK (which funds composites), lightweight structural composite components developer Far Composites and Composite Braiding. The frame is made from a series of braided thermoplastic composite tubes which are easily assembled via adhesive bonding and simple welding.
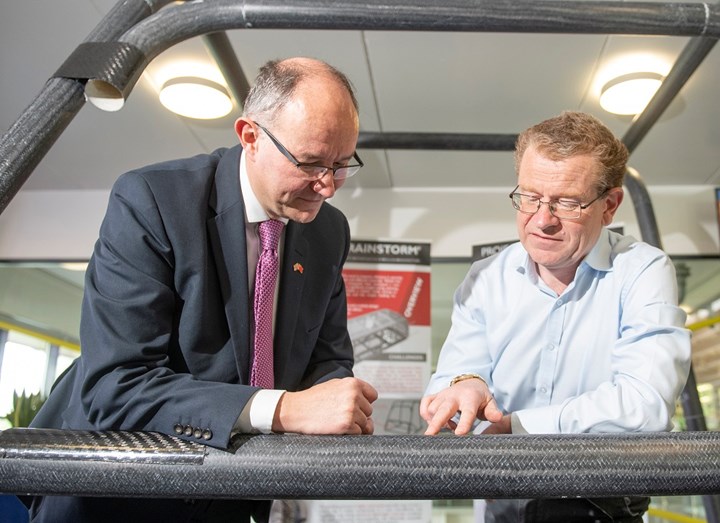
The VLR prototype/demonstrator vehicle will use a spaceframe chassis made from braided carbon fiber-reinforced thermoplastic composite tubes which are easily assembled via adhesive bonding and simple welding. SOURCE | University of Warwick.
The tube outside diameters are kept the same, with different load and attachment requirements handled by varying the wall thicknesses. This keeps tooling costs low and means that joins can be standardized. Braiding enables a highly automated manufacturing process — rates for the reinforcement alone can exceed 1 mile/day — as well as a tailorable set of materials, including other fibers (e.g., glass, aramid, thermoplastic) and thermoplastic matrix materials from low-cost polypropylene to high-end polyetheretherketone (PEEK). Meanwhile, WMG has demonstrated a complete molding cycle that can be reduced to less than five minutes, highlighting the potential of this affordable process for high-volume applications.
Braiding enables highly automated manufacturing … a tailorable set of materials … a complete molding cycle that can be reduced to less than five minutes, highlighting the potential of this affordable process for high-volume applications.
Thermoplastics also provide for recyclability, according to David Goodwin, engineering manager at Far-UK. “With composites you can save a lot of weight, which is obviously appealing for the operation of the [rail] car,” he begins, “but with traditional composites, at the end of the car’s life it is simply placed in landfill, which is not ideal. With this [design], there is a route to recycle the car body when it eventually goes out of service, or, alternatively, if it suffers an impact and part of it has to be repaired and replaced.”
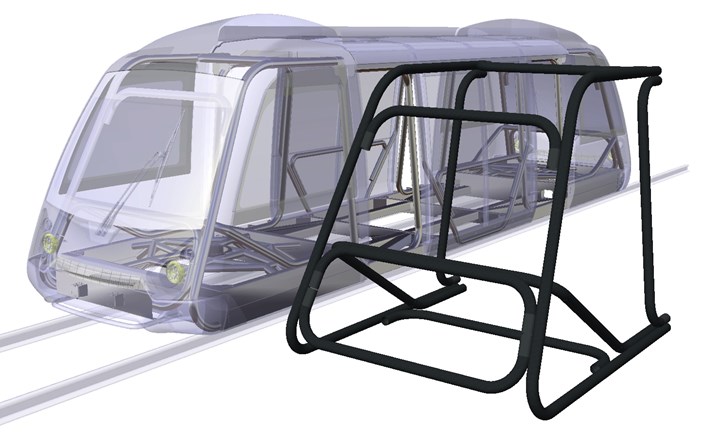
University of Warwick
The tubular spaceframe chassis design also aids in this approach, allowing any damage tubes to be simply removed and replaced with a new or repaired one. “Our BRAINSTORM VLR research partnership has achieved significant weight-saving, allowing VLR services to accommodate more passengers while reducing the energy required to propel the vehicle and the weight stress it will place on its rails and road surface,” explains Dr. Darren Hughes, associate professor in Materials and Manufacturing at WMG University of Warwick. “The technology also ensures that the vehicle is tough for a long life in service, easily repairable when accidents happen and strong enough to protect the passengers on board.”
“The BRAINSTORM Project feels like a real step forward to the team at Far Composites,” says Far-UK director and general manager Lyndon Sanders. “Being able to tap into the industry experience of TDI to hone the principle of a new type of body structure for mass transit applications was great. Add to that the collaborative working with Composites Braiding and WMG to turn that thinking into a physical demonstrator to show what it would be like in practice was really powerful. Now it’s more than a good idea, it’s an eye opener for industry players who can see it, touch it and even pick it up.”
Related Content
Optimizing a thermoplastic composite helicopter door hinge
9T Labs used Additive Fusion Technology to iterate CFRTP designs, fully exploit continuous fiber printing and outperform stainless steel and black metal designs in failure load and weight.
Read MoreTU Munich develops cuboidal conformable tanks using carbon fiber composites for increased hydrogen storage
Flat tank enabling standard platform for BEV and FCEV uses thermoplastic and thermoset composites, overwrapped skeleton design in pursuit of 25% more H2 storage.
Read MoreManufacturing the MFFD thermoplastic composite fuselage
Demonstrator’s upper, lower shells and assembly prove materials and new processes for lighter, cheaper and more sustainable high-rate future aircraft.
Read MorePlant tour: Airbus, Illescas, Spain
Airbus’ Illescas facility, featuring highly automated composites processes for the A350 lower wing cover and one-piece Section 19 fuselage barrels, works toward production ramp-ups and next-generation aircraft.
Read MoreRead Next
VIDEO: High-volume processing for fiberglass components
Cannon Ergos, a company specializing in high-ton presses and equipment for composites fabrication and plastics processing, displayed automotive and industrial components at CAMX 2024.
Read MoreAll-recycled, needle-punched nonwoven CFRP slashes carbon footprint of Formula 2 seat
Dallara and Tenowo collaborate to produce a race-ready Formula 2 seat using recycled carbon fiber, reducing CO2 emissions by 97.5% compared to virgin materials.
Read MorePlant tour: Daher Shap’in TechCenter and composites production plant, Saint-Aignan-de-Grandlieu, France
Co-located R&D and production advance OOA thermosets, thermoplastics, welding, recycling and digital technologies for faster processing and certification of lighter, more sustainable composites.
Read More