Aluula introduces lightweight composite materials for wind sports and beyond
The company’s proprietary UHMWPE fabrics combined with technical films in a patented fusion process are said to increase performance and recyclability.
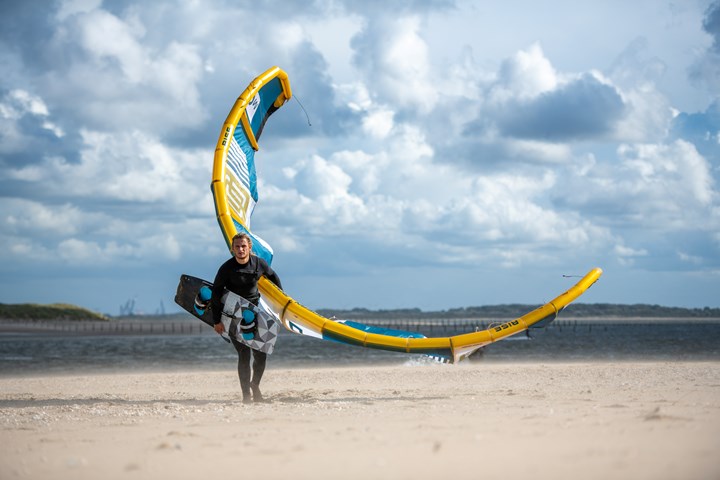
Ocean Rodeo pro rider Giel Vlugt with his Rise kite featuring an Aluula air frame. Photo Credit: Rein Rijke, via Aluula Composites Inc.
Advanced materials technology firm Aluula Composites Inc. (Victoria, British Columbia, Canada) introduces a range of ultra-strong lightweight fabrics that combine with polymer films in a patented fusion process to increase performance in windsports and other applications.
Founded in 2019, Aluula is the brainchild of chemists and engineers with a passion for outdoor sports. The initial objective was to engineer materials that would better serve kiteboarding and the quickly growing wing foiling market. Both markets had inherited legacy materials and seaming techniques from the sail industry, and technical and material developments had stalled. However, surging interest in these wind sports started driving innovation and development of new materials. The Aluula Composites team set out to develop materials with kiteboarding weight, strength and performance objectives in mind, as well as toughness and ability to withstand harsh sun and abrasive beach environments.
The resulting product line, according to Aluula, is a new class of composite materials built from components with eight times the strength-to-weight ratio of steel, and yet are lighter than nylon, polyester or aramid. Aluula’s technology combines one of several Aluula Core fabrics with one of the company’s technical films, via its patented Aluula Fuse process.
Aluula Cores are said to be proprietary formulations of 100% ultra-high molecular weight polyethylene (UHMWPE). These include Aluula Gold GC-82, an 82-gsm fabric used within wind sports for lightweight, rigid airframe structures, and ultra-durable, lightweight Aluula Durlyte HH-140 for reinforcing airframe seaming.
Aluula Fuse is a fusion process for binding high-tech fabrics and technical films together without the use of heavy glues. This process is said to result in a stronger, lighter material that will not delaminate and is less susceptible to UV and general abuse. Fusing materials without glues in this way is also said to make the fabrics recyclable at their end of life (EOL).
Alongside developing new fabrics and films to suit different needs, the company also says it can develop customized materials for unique applications.
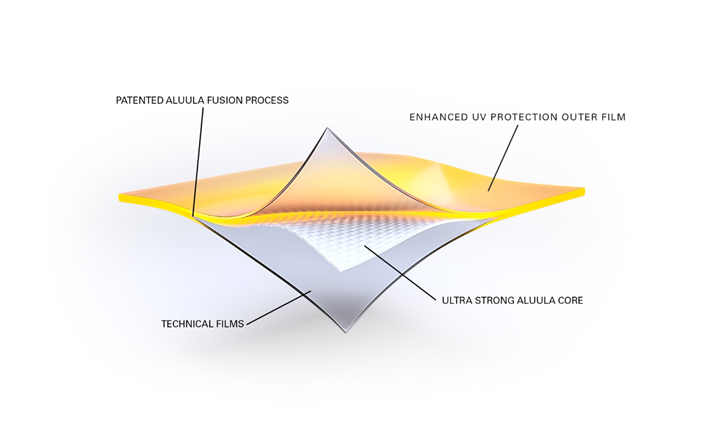
Within wind sports, Aluula’s materials are said to be half the weight of traditional materials, and also stiffer and stronger than existing composite options. Specifically, kite and wing airframes are built by sewing patterned pieces of fabric together to create 3D shapes. An internal bladder is then installed and inflated at high pressure to create the kite’s structure and rigidity.
Aluula says that kiteboarders using a lightweight Aluula composite kite can fly in much lighter wind, while increased stiffness delivers much better performance in stronger winds.
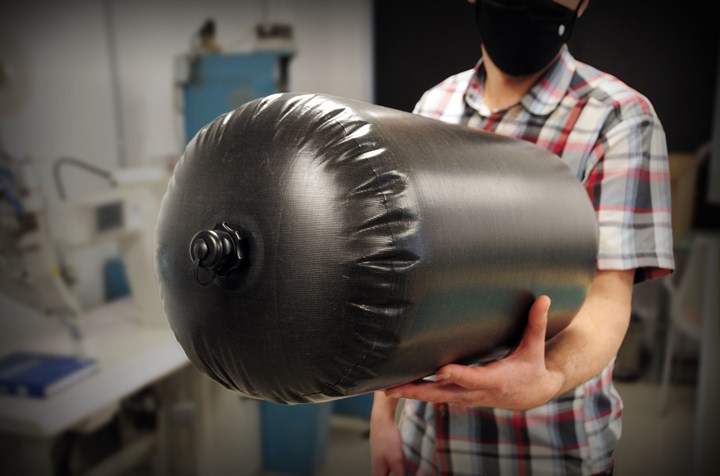
Beyond wind sports, Aluula is now working with industry partners to develop next-level materials for applications in aerospace, outdoor gear, sailing and defense markets. These efforts are driving further innovation and intellectual property in the material bonding sciences. Meanwhile, promising additional cross-linking technology development continues between Aluula and its chemistry partners. The company also says it is exploring additional manufacturing techniques including heat welding, steam taping and molding in the development of air- and water-tight structures.
Related Content
Natural fiber composites: Growing to fit sustainability needs
Led by global and industry-wide sustainability goals, commercial interest in flax and hemp fiber-reinforced composites grows into higher-performance, higher-volume applications.
Read MoreThe potential for thermoplastic composite nacelles
Collins Aerospace draws on global team, decades of experience to demonstrate large, curved AFP and welded structures for the next generation of aircraft.
Read MoreManufacturing the MFFD thermoplastic composite fuselage
Demonstrator’s upper, lower shells and assembly prove materials and new processes for lighter, cheaper and more sustainable high-rate future aircraft.
Read MoreInfinite Composites: Type V tanks for space, hydrogen, automotive and more
After a decade of proving its linerless, weight-saving composite tanks with NASA and more than 30 aerospace companies, this CryoSphere pioneer is scaling for growth in commercial space and sustainable transportation on Earth.
Read MoreRead Next
All-recycled, needle-punched nonwoven CFRP slashes carbon footprint of Formula 2 seat
Dallara and Tenowo collaborate to produce a race-ready Formula 2 seat using recycled carbon fiber, reducing CO2 emissions by 97.5% compared to virgin materials.
Read MoreDeveloping bonded composite repair for ships, offshore units
Bureau Veritas and industry partners issue guidelines and pave the way for certification via StrengthBond Offshore project.
Read More“Structured air” TPS safeguards composite structures
Powered by an 85% air/15% pure polyimide aerogel, Blueshift’s novel material system protects structures during transient thermal events from -200°C to beyond 2400°C for rockets, battery boxes and more.
Read More