CAMX 2021 exhibit preview: Regloplas
Regloplas thermal control units (TCU) offer energy-efficient, rapid heating and cooling solutions for composite tooling.
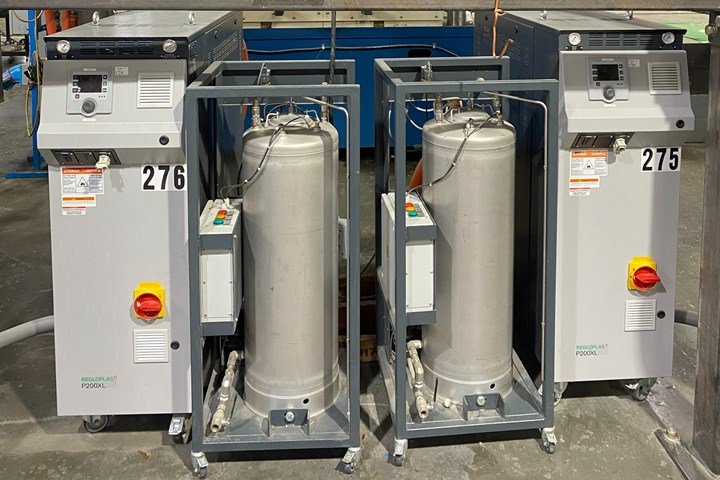
Regloplas USA (St. Joseph, Mich., U.S.) provides pressurized water-based heating and cooling technology to enable advanced composite manufacturers to meet cycle time and cost targets. Advantages are said to include energy savings, high-temperature capability, precise temperature control, fast ramp rates and the ability to cool.
According to the company, its thermal control units (TCU) offer a alternative to autoclaves, ovens, presses and electric cartridge heaters — which often consume large amounts of electricity, do not offer cooling and may provide inconsistent heating — for heating composite molds.
Regloplas says TCUs can be used as an out-of-autoclave (OOA) process to rapidly heat and cool tooling for thermoset and thermoplastic composites, or it can be used in conjunction with an autoclave, driving heating and cooling while the autoclave vessel provides compaction pressure.
The smart TCU product line features temperature ranges from 195 to 285°F, pressurized high-temperature water product line temperatures of 212 to 446°F. Both lines serve as a safer, energy-efficient alternative to hot oil processes. Regloplas also offers hot oil units that range from 300 to 662°F and come in various models, sizes and flows.
Additional benefits to Regloplas solutions include:
- Lower facilities operating costs
- Consumes 65% or more less energy than oil systems
- Heats and cools the tool in the same circuit
- Compact packaging to reduce plant floor space requirements
- Quick disconnects allow for modular plant equipment designs/layout
- Qater has higher density, specific heat and thermal conductivity than oil or steam for better heat transfer
- High temperature range (446°F) for epoxy, cyanate ester, polyimide and BMI resin systems
- Fast ramp rates on heat up and rapid consistent cool down
- Precise temperature control (±2°F) across the tool
- Safe at a line break, with low temperature water vapor due to decompression.
Related Content
-
R&D focus underpins quality gelcoat offerings
CAMX 2024: HK Research strives for innovation and customer satisfaction through meticulously produced polymers, liquid pigments and specialty additives and customer support.
-
Getting ready for CAMX 2024
The Composites and Advanced Materials Expo’s 10th anniversary trade show and conference will be held in San Diego from Sept. 9-12, 2024.
-
One-stop composites manufacturer, distributor
CAMX 2023: FiberGlass Coatings provides B2B and B2C and services to meet fiberglass and coating product needs.