Polygon PolySlide composite tubing replaces metal for pneumatic and hydraulic cylinders
The filament-wound glass fiber composite tubing exhibits high strength, dimensional stability and resistance to corrosion.
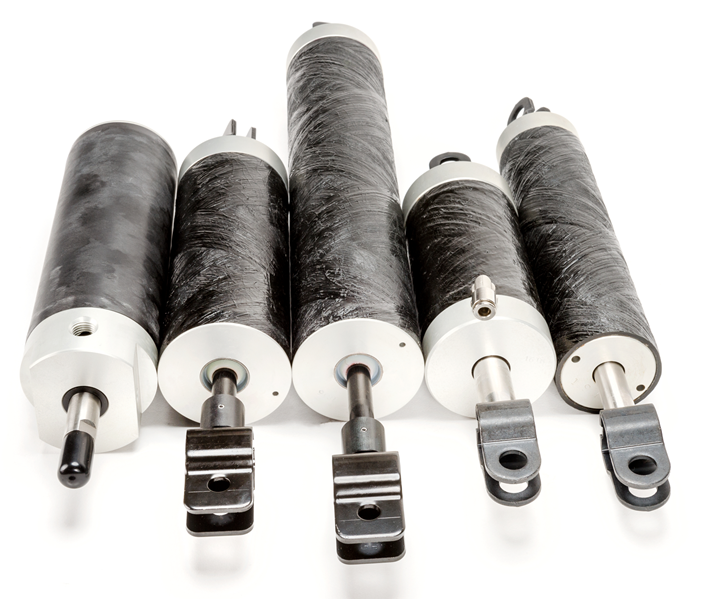
Source | Polygon
Polygon Composites Technology (Walkerton, Ind., U.S.), manufacturer of composite tubing solutions for bearings, dielectric applications, surgical devices and more, has launched PolySlide composite tubing for pneumatic and hydraulic cylinders. PolySlide tubing replaces metallic material in a variety of cylinder applications.
Supplied as a cylinder tube for customer assembly, or as fully engineered cylinder assemblies for equipment manufacturer applications, the tubing is made of continuous filament-wound glass fiber and polymer resins. The fiberglass filament and resin materials combine together to form a high-strength component that exhibits dimensional stability, is non-corroding, impingement-resistant and is non-conductive. The cylinder tubing is said to perform in high and low temperatures, grease, grit, salt, chemicals and other extreme conditions.
PolySlide cylinder tubing sizes range from as low as 0.25" inner diameter (ID) up to industrial-sized 24" IDs. The features of the tubing allow the seal to slide over the bore surface contour, minimizing interlocking friction. The inside diameter of the tubing has a smooth finish. Contact with the non-metallic rod guide bearing prevents galling and provides for a low coefficient of friction. A wear-resistant material incorporated into the bore surface further increases the lifespan of the composite cylinder tubing.
According to Polygon, common applications of this product include use with pneumatic and low-pressure hydraulic applications, such as fifth wheel actuation, gate valve actuators, water treatment flow control mechanisms, tie rod cylinders and more. A translucent version of the composite cylinder tubing is also available.
Related Content
-
Sulapac introduces Sulapac Flow 1.7 to replace PLA, ABS and PP in FDM, FGF
Available as filament and granules for extrusion, new wood composite matches properties yet is compostable, eliminates microplastics and reduces carbon footprint.
-
PEEK vs. PEKK vs. PAEK and continuous compression molding
Suppliers of thermoplastics and carbon fiber chime in regarding PEEK vs. PEKK, and now PAEK, as well as in-situ consolidation — the supply chain for thermoplastic tape composites continues to evolve.
-
Pultrusion: The basics
A primer describing what pultrusion is, its advantages and disadvantages, and typical applications.