3D printing for a Bonneville run
As a former (amateur vintage) racer myself, I appreciate all things motorsports. CRP USA LLC (Mooresville, NC, US), the maker of Windform SLS 3D printing materials as well as provider of custom additive manufacturing and machining services, sent me a case study of a motorsports team that recently set a new class record at the Bonneville Salt Flats, thanks to the fast part production possible with 3D printing.
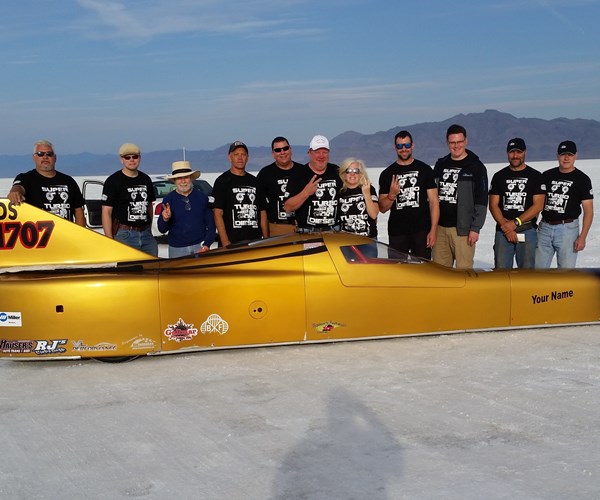
Victory Motorsports celebrates their class win at Bonneville Salt Flats.
As a former (amateur vintage) racer myself, I appreciate all things motor sports, from Formula 1 down to kids’ go carts. And anyone familiar with racing knows the Bonneville Salt Flats, that great dry lake east of Wendover, UT, US. For more than 100 years, Bonneville has created a competitive spirit that has attracted racers from the likes of Mickey Thompson, Bobby Issac (of NASCAR fame), and Valerie Thompson (the fastest female motorcycle racer), and challenged racers, and their machines, to test the limits of speed.
It’s an equal opportunity environment: you don’t need a giant budget or big blocks to run. Engine classes run from 30 cubic Inches (490 cc) to 501 cubic Inches (8 liters), in 12 different engine size classes. Some speed records are still less than 100 mph, so with creativity, smart use of budget, and a lot of courage, anyone has a shot at the record books.
The folks at CRP USA LLC (Mooresville, NC, US), who offer Windform SLS 3D printing materials as well as custom additive manufacturing and machining services, sent me a case study of a motor sports team that recently set a new class record, thanks to the fast part production possible with 3D printing. I’ve summarized the case study here.
Burton Brown of Victory Motorsports (Dale, WI, US) heads a small team that has worked to set speed records with their Streamliner, a low-slung, custom-bodied Salt Flats racer. His crew is a combination of skilled craftsmen and weekend warriors that dedicate their time to a form of racing that requires a strong team approach. Burton explains his thoughts on the speed records: “Getting into the 200 mph club was always a goal, and my dad and I always talked about someday getting a ‘red hat’ [given to those in the club]. I promised him I’d get him one someday, so that had always been something I intended to do. We knew from the start our Streamliner could top 300 mph, so we had a few goals during Speed Week 2017 we hoped to accomplish. The first one was to break the long-standing F/DS [streamliner] record of 199.015 mph from 1979. Additionally, we hoped to not only break the record, but go 250+ and obtain an AA License, which would have allowed us to take a shot of going 300 mph [you need different licenses to go higher speeds].”
Burton continues, “We named this venture ‘The Junkyard 300’ as the engine we were using came directly out of the salvage yard in January without disassembly. We then fabricated a header, added a Borg Warner S300Turbo and an OM606 fuel injection pump by Dieselmeken AB Sweden [Aneby, Sweden] as the only major changes. We don’t have the budget that some of the teams have, so there are many parts on the car that we obtained very cheaply. We try to cut costs where we can, so we can use the money we save for the trip back and forth from the Salt. That is part of the fun for me.”
Another key component for Victory Motorsports’ attempt to meet their goals would be a new intake duct designed by David Woodruff from Design Dreams LLC (Cincinnati, OH, US) for the Streamliner. Burton knew of CRP USA, because the company had printed velocity stacks for another Bonneville record-setting race car, a Datsun (now Nissan) 240Z. However, a new engine for the 240Z was not going to be ready, so the team began concentrating all efforts on the Streamliner. With less than a week to go before the deadline to load the car onto the trailer for the 1,600-mile, 32-hour drive, the team realized that the complex design of the duct from David Woodruff could not be fabricated in time using normal methods, and the anticipated combination of high-frequency vibration, intense sun, and high temperatures started narrowing the options. Burton was running out of time.
“Stewart Davis from CRP USA had called to check on the progress of the Z engine and I had to tell him we couldn’t make it with the 240Z and that we had switched our complete focus towards the Streamliner,” says Burton. “I explained we were struggling with the duct and asked if Stewart and his team could help us with that challenge. So, we talked more about the possibility of CRP making the part. Without hesitation, Stewart asked for the model and CRP USA produced an absolutely perfect piece.”
The inlet part, called a NACA duct, was nearly 0.72m long and with a complex interior design, and presented an interesting challenge. By way of background, a NACA duct (or scoop, or inlet), is a low-drag air inlet design, originally developed by the U.S. National Advisory Committee for Aeronautics (NACA), the precursor to NASA, in 1945. Being familiar with such ducts, the CRP USA team knew the work involved to make the surfaces smooth, a necessity for optimum air flow. Says Davis, “The design has some extra complexity to help the air flow at the base of the turbo inlet, and it looked a bit daunting. We had to build it in 3 sections, but our finishing team was able to apply their knowledge and skill to give an expert polish.” CRP USA received the final model on July 26th. When completed, the part was sent to Victory Motorsports, and arrived on August 1st.
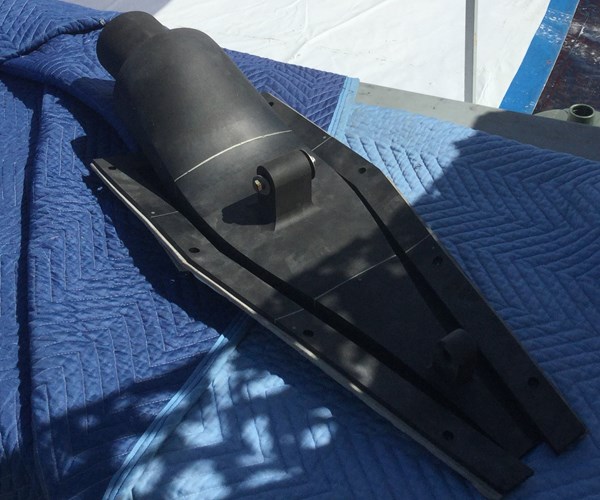
The NACA duct made by 3D printing by CRP, using Windform SP
Upon arrival, the duct was installed in the engine bay just fine; however, a complication arose when the newly painted body fairing arrived. Says Burton of the fitment, “The fit to the engine was great but the curvature created some challenges getting it to fit to the body.” With the clock ticking, the team loaded everything into the truck, and headed for Utah. Stewart also headed for Bonneville: “Burton had invited me to come and see the Streamliner. When I arrived on Friday morning, we reviewed the fitment issues,” Stewart continues. “Attempting to force the part was not working. The Windform SP is a very tough material, so the decision was made to fracture a section of the part to allow a little give, so it would match the curve of the fairing, and then reinforce it by riveting an aluminum backing plate.” Utilizing onsite tools, the team worked Saturday and Sunday to prepare, both for the first runs, and to modify and refit the NACA duct.
On Sunday, the Streamliner passed tech, and the team prepared for a Monday morning run. The opening speed week passes on Saturday had yielded two runs above 400 mph, so Burton knew that the potential for breaking the record in their class was a possibility. Conditions were good Sunday, but the track had started to get rough in some areas. Burton elaborates, “The track was a lot rougher than I had ever experienced at Bonneville. The Streamliner withstood some damage to the fiberglass due to the roughness of the salt/silt surface. Our exit speed at mile 6 was 234 mph.“ The radio announced that the team had qualified for the record, and the car was placed in impound for inspection prior to the follow-up run. To gain the record, each team must complete two runs, with the average used to calculate the new record. The second run to establish the two-pass average was Tuesday morning, prior to 7 am.
On Tuesday morning, the team celebrated the radio announcer’s call of a new class record. With the engine making plenty of power, it was the rough surface that made it a challenge to get power to the salt. “I was pretty sure we got the record but needed verification from the crew. With the traction issues and exit speed of 234 MPH, we know there is a lot more in this car and setup,” says Burton.
“The Windform SP part performed extremely well, and held up to all of the abuse, even being heavily modified while on the salt flats, with limited tools and time. I am still completely amazed at its strength. It gave us no issues withstanding the speed and the rough track and vibrations. It is a very light, strong material that can also take the extreme heat generated in the very tightly-fitted body. A few years ago, I wouldn’t have dreamed of having something like this on the Streamliner,” concludes Burton.
Stewart Davis stated, “It was great to be a part of the team’s record-setting run, and we congratulate Burton and his team on the record. We are fortunate to work with teams that are dedicated to their sport, and the Victory Motorsports Team is a great example of the hard work and determination it takes to be successful.” Learn more about CRP at www.crp-usa.net.
Related Content
Bio-based acrylonitrile for carbon fiber manufacture
The quest for a sustainable source of acrylonitrile for carbon fiber manufacture has made the leap from the lab to the market.
Read MoreThe potential for thermoplastic composite nacelles
Collins Aerospace draws on global team, decades of experience to demonstrate large, curved AFP and welded structures for the next generation of aircraft.
Read MoreTU Munich develops cuboidal conformable tanks using carbon fiber composites for increased hydrogen storage
Flat tank enabling standard platform for BEV and FCEV uses thermoplastic and thermoset composites, overwrapped skeleton design in pursuit of 25% more H2 storage.
Read MorePlant tour: Teijin Carbon America Inc., Greenwood, S.C., U.S.
In 2018, Teijin broke ground on a facility that is reportedly the largest capacity carbon fiber line currently in existence. The line has been fully functional for nearly two years and has plenty of room for expansion.
Read MoreRead Next
VIDEO: High-volume processing for fiberglass components
Cannon Ergos, a company specializing in high-ton presses and equipment for composites fabrication and plastics processing, displayed automotive and industrial components at CAMX 2024.
Read MorePlant tour: Daher Shap’in TechCenter and composites production plant, Saint-Aignan-de-Grandlieu, France
Co-located R&D and production advance OOA thermosets, thermoplastics, welding, recycling and digital technologies for faster processing and certification of lighter, more sustainable composites.
Read MoreDeveloping bonded composite repair for ships, offshore units
Bureau Veritas and industry partners issue guidelines and pave the way for certification via StrengthBond Offshore project.
Read More