A look inside Fraunhofer ICT
Fraunhofer-Gesellschaft (Munich, Germany) is the largest applied research organization in Europe, with more than 67 institutes and research units located throughout Germany staffed by 24,500 people, mostly scientists and engineers. CW recently got a chance to tour one, Fraunhofer ICT in Pfintzal, Germany.
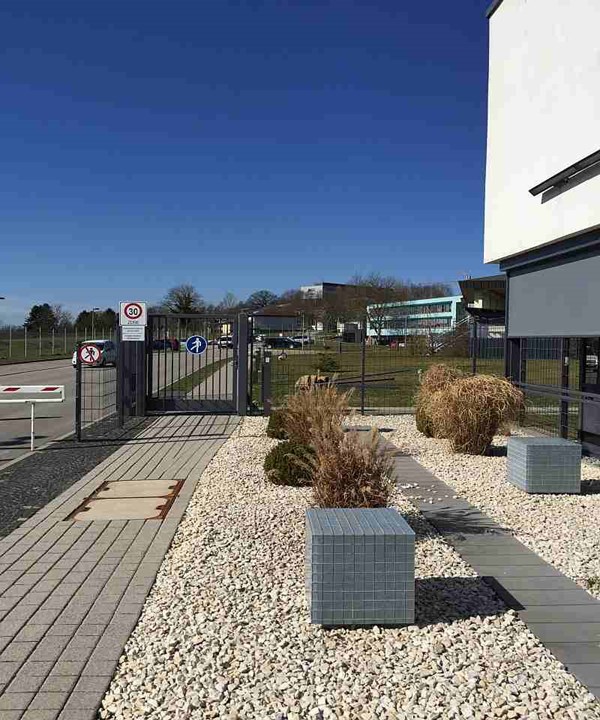
The view of Fraunhofer ICT from the gatehouse.
Fraunhofer-Gesellschaft (Munich, Germany) is the largest applied research organization in Europe, with more than 67 institutes and research units located throughout Germany staffed by 24,500 people, mostly scientists and engineers. Thirty-four research units are located beyond Germany. More than 70% of the group’s annual budget, which tops 2 billion Euro ($2.35 billion USD), comes from contract research with industry and publicly financed research projects, covering the gamut of scientific topics.
But this massive organization tends to be dispersed unobtrusively, with its centers typically located a bit off the beaten path, as is the case with Fraunhofer Institute for Chemical Technology (Institut für Chemische ICT) in Pfintzal, Germany. ICT includes in its research portfolio polymer engineering, and that department includes high-performance fiber composites, nanocomposites, thermoplastic processing, thermoset processing, microwave and plasma heating technology, foams, and compounding/extrusion, all under the direction of department head and ICT deputy director Dr. Frank Henning. And despite its bucolic location, the activities and research projects there have had far-reaching impacts throughout the world of composites.
Bilateral connections
Fraunhofer ICT is found in southwestern Germany, within the state of Baden-Württemberg and a short distance east of Karlsruhe, Germany, a city on the Rhine and the home of the Karlsruhe Institute of Technology (KIT, which maintains a close relationship with Fraunhofer). ICT comprises a sprawling collection of older and newer buildings on a steep-sided hill above the small village of Pfintzal, surrounded by forest and farmland. The Institute was founded in 1959 as the “Institute for Chemical Propellants” and was originally located in an abandoned stone quarry nearby that helped contain its rocket combustion experiments. In 1964, operations moved to the current hilltop site, and were given the new name Institute for Chemical Technology. The 1970s brought contract research from civil and military customers, and the polymer engineering group was begun in 1994. Today, ICT employs more than 500 people and has a yearly turnover of 36.5 million Euro ($40 million USD).
My visit starts at the gate house where directions are given to Building 90, located about a half-mile distant, and further uphill. Luckily, fair weather makes an enjoyable hike to this large, multi-story building that houses much of ICT’s composites activities. There I’m met by Alexander Roch, the head of ICT’s thermoplastic technology “corridor” within polymer engineering. Roch clarifies that there are five main research centers on the campus: Two, involving energetic materials, work mainly (but not exclusively) for the German Ministry of Defense, leaving polymers engineering, environmental engineering (which includes recycling studies and weathering, among other topics) and applied electrochemistry (focused on batteries and fuel cells). One-third of ICT’s budget comes from the German state, another third from industrial partners who contract research, and one-third from funded European Union and public German grants. Roch points out, as an example of an applied electrochemistry project, an energy accumulation system termed RedoxWind designed to test electrical storage of wind energy, and points out workers installing a large wind turbine tower and rotor to test the concept.
“Within the polymer engineering department, we cultivate very strong collaborations with automotive OEMs and Tier 1 suppliers,” states Roch. “Our location in Baden-Württemberg, with an established industrial base, puts us close to Porsche, Diamler and Mercedes-Benz as well as Audi.” He adds that the “bilateral connections” between Fraunhofer and its industrial partners are strictly confidential, and are structured such that OEMs pay for machine time, testing and consultations with Institute staff. Close relationships have also been established with machine and system suppliers such as KraussMaffei Technologies GmbH (Munich, Germany) and Dieffenbacher (Eppingen, Germany) that enable financial arrangements to ensure the best equipment for research. “We are not allowed to make parts for profit, only for prototyping and validation,” he explains.
Glass-shelved display cases in Building 90’s atrium show the wide range of ICT’s activities. Roch points out examples of automotive engine parts made using ICT’s thermoset injection molding process, a project undertaken with SBHPP, the high-performance business unit of Sumitomo Bakelite Co. Ltd. (Tokyo, Japan). An engine cylinder liner was injection molded with SBHPP’s glass fiber-reinforced phenolic (55% fiber content) pourable molding granules, with a cycle time as low as 45 seconds (see Learn More). Also on display are long fiber injection molded parts made with polyurethane resin, biocomposite parts using bioresins as well as bio-based fibers, and complex ribbed parts made using Dieffenbacher’s RELAY technology (developed originally by FiberForge) that have been subsequently overmolded via injection molding methods. Roch shows parts made in a process that he has helped pioneer, as reported by CW (see Learn More): A thermoplastic in-mold foaming technology combined with a controlled mold-opening technique called “breathing mold” produces a foamed core between solid faceskins — both reinforced with chopped glass fibers — with the part formed in a single shot. Roch then leads the way to various laboratories and work areas to show how these innovative materials and processes are realized.
The entire tour will be published in an upcoming print issue of CW magazine, but here are a few excerpts:
A spacious work area is dedicated to research and optimization of injection molding processes, and particularly, long-fiber injection molding (Long Fiber Reinforced Thermoplastics or LFRT), foam injection molding (FIM) as well as thermoset injection molding using thermoset granules. Roch shows ICT’s newest machine from KraussMaffei, a multifunctional GX Series machine capable of all three molding processes. Technicians test the control system as Roch shows me how injection unit barrels can be swapped out in modular fashion, to accommodate different polymers and chopped fiber lengths: “We have a special screw for molding the phenolic thermoset granules.” A robot will be eventually integrated into the machine for material and preform handling and mold loading/unloading. He adds that ICT has a total of six twin-screw extruders on site, as well as 6 injection molding machines, for researching polymer processes.
A large Engel Austria (Schwertberg, Austria) duo 700 pico combi M injection molding machine is usable for standard injection molding, for direct (LFT-D) long fiber molding or foam injection molding of LFT granules using the MuCell microcellular foam process from Trexel Inc. (Wilmington, MA, US). The 700-tonne machine has two injection units, back to back, which enables co-molding, says Roch, and the inner mold part of a stackmold, mounted on a rotary table, can be turned 180° to allow injection from both sides. He points out the glass fiber rovings fed into the machine from above, and the glass fiber package creel: “With this direct LFT technology, you become your own custom compounder, using longer fiber lengths than are available from compounders, and you can save to 20 to 30% of the cost of pre-made pellets.” One of the machine’s injection units is used for making the long-fiber-reinforced in-mold foamed sandwich parts explained by Roch at the beginning of the tour; he points out where the foaming agent enters the barrel, either a chemical foaming agent or nitrogen gas (the MuCell process). In addition, robotic handling of heated organosheet and preforms can be integrated with this machine for overmolding.
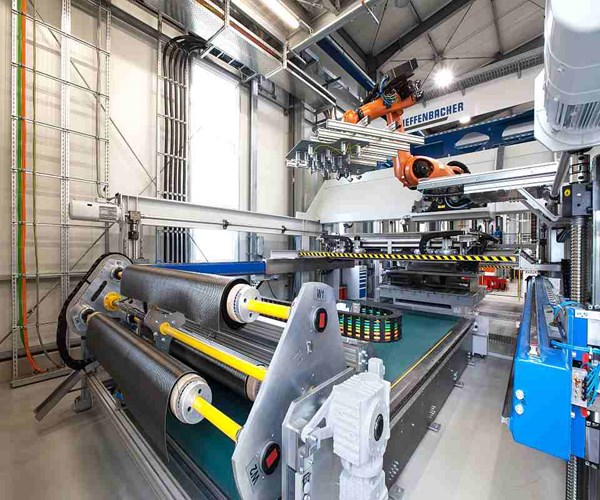
The HP-RTM preforming center.
Next, we walk further downhill to another laboratory building where high-pressure resin transfer molding (HP-RTM) activities are housed. Near the doorway is a preforming center within a safety cage, equipped with a robot to transfer material from an automated cutting table to a heated shaping mold. The preforming setup is similar to the Dieffenbacher North America Inc.PreformCenter installed in Fraunhofer’s Ontario, Canada facility in 2014. Roch explains that the preform shaping mold is capable of complex sequential movements during closing, that allow for a highly shaped part preform without wrinkles. A structural part for Mercedes Benz is displayed outside the cage, which shows how the relatively high areal weight woven carbon fiber twill fabric conforms without pulling or wrinkling.
See CW coverage of some of these technologies:
http://www.compositesworld.com/articles/breathing-mold-process-yields-sandwich-composite-from-lft
http://www.compositesworld.com/articles/composite-engine-piston-cylinder-housings
Related Content
MFFD thermoplastic floor beams — OOA consolidation for next-gen TPC aerostructures
GKN Fokker and Mikrosam develop AFP for the Multifunctional Fuselage Demonstrator’s floor beams and OOA consolidation of 6-meter spars for TPC rudders, elevators and tails.
Read MoreSmartValves offer improvements over traditional vacuum bag ports
Developed to resolve tilting and close-off issues, SmartValves eliminate cutting through vacuum bags while offering reduced process time and maintenance.
Read MoreGKN Aerospace, Joby Aviation sign aerostructures agreement
GKN Aerospace will manufacture thermoplastic composite flight control surfaces for Joby’s all-electric, four-passenger, composites-intensive ride-sharing aircraft.
Read MorePEEK vs. PEKK vs. PAEK and continuous compression molding
Suppliers of thermoplastics and carbon fiber chime in regarding PEEK vs. PEKK, and now PAEK, as well as in-situ consolidation — the supply chain for thermoplastic tape composites continues to evolve.
Read MoreRead Next
Composite engine piston cylinder housings
Phenolic BMC could replace aluminum in car/motorcycle engine housings.
Read MoreBreathing-mold process yields sandwich composite from LFT
In-cavity foaming and controlled mold-opening technique creates core and faceskins from a single injection molded material, reducing part mass and boosting performance.
Read MoreVIDEO: High-volume processing for fiberglass components
Cannon Ergos, a company specializing in high-ton presses and equipment for composites fabrication and plastics processing, displayed automotive and industrial components at CAMX 2024.
Read More