Composites manufacturing from a different angle
A bunch of really smart engineers showed up in Long Beach, CA, US this week for the Society of Manufacturing Engineers’ (SME, Dearborn, MI, US) AeroDef conference and exhibition. All were focused on looking at ways to manufacture products — composite or not — more efficiently.
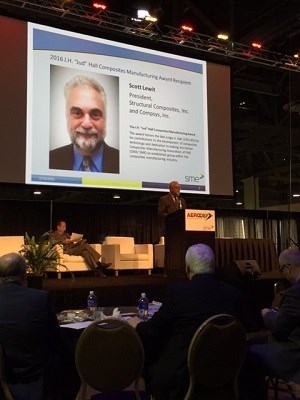
Manufacturing excellence was the focus at this week's SME AeroDef event in California. Scott Lewit, shown here, was the Jud Hall Composites Manufacturing Award winner.
A bunch of really smart engineers showed up in Long Beach, CA, US this week for the Society of Manufacturing Engineers’ (SME, Dearborn, MI, US) AeroDef conference and exhibition. All were focused on looking at ways to manufacture products — composite or not — more efficiently. In fact, some attendees admitted they were there to learn more about composites from the technical sessions. The big themes, gleaned from hearing attendee chit-chat as well as speakers and panelists, were automation in manufacturing, and developing a robust digital thread, and eventually a digital tapestry, using data analytics that reduce manufacturing risk and, eventually, the need for today’s extensive build/test and inspection cycles. As one attendee noted, manufacturing of composites has likely become more critical and complex today than the upfront part design process.
Pre-show, I had the chance to tour with some other attendees the facility of Coast Composites (an Ascent Aerospace company, Santa Ana, CA, US). Company CEO Paul Walsh gave the tour, which provided a close-up view of huge Invar wing skin layup tools made to tight tolerance for Airbus, and how those tools are welded and formed. A view of the composite tool production area was also provided. A key point that Walsh pointed out was how Coast manages and tracks its work flow to detect bottlenecks or issues before they can adversely affect delivery (keeping with the data analytics theme).
Kicking off the event was Scott Willoughby, Northrop Grumman Aerospace Systems vice president and the program manager for the James Webb space Telescope, who described the daunting telescope project. This huge space structure, set to launch in 2018 and to be positioned 1.5 million km from Earth, must be folded like origami to fit inside its Ariane 5 launch vehicle, and thus requires 178 release devices to deploy or unfold 40 structures over a period of 14 days after launch, explained Willoughby, who stressed that manufacturing with a huge variety of materials and deployable structures, including composites and beryllium for the mirrors, has been “very challenging.”
Dr. Leslie Cohen of Hitco chaired the following panel on data analytics, which included George Barnych, the director of research and development at the Digital Manufacturing and Design Innovation Institute (DMDII), Roland Dutton, chief of the Manufacturing and Industrial Technologies Division at the Air Force Research Laboratory (AFRL) and Ray Johnson, formerly with Lockheed Martin and a big proponent for analytics. Attendees listened closely and questioned the panel on the role of data collection and analysis to make manufacturing and logistics more affordable and sustainable, which, said Johnson, “is really happening. We have a huge opportunity here.”
The winner of the 2016 Jud Hall Composites Manufacturing Award, SME’s most prestigious, was Scott Lewit of Structural Composites. Ever inventive and dynamic, Lewit has pushed the boundaries of composites designs and manufacturing, as evidenced by his ability to move technologies developed for the U.S. Navy into consumer marine and now, transportation applications. Here’s a link to our recent CAMX event coverage that describes Lewit’s work with Wabash National, a major semi-truck trailer manufacturer: http://www.compositesworld.com/blog/post/camx-redux-more-green-more-customized-composites-even-in-space-and-more-growth. Lewit was able to develop a resin technology that mixes higher-performance resin with low-cost commodity resin in areas of the part that need more strength, while keeping material costs low enough for parity with traditional materials.
Many technical papers covered new, or evolving, technologies that have the potential for lowering manufacturing costs and complexities. David Lahrman, vice president of business development for LSP Technologies (Dublin, OH, US), spoke about his company’s technology that inspects adhesive bond lines, post-bond. The Boeing Co. originally contacted LSP to see if such a concept was possible, and Lahrman says his group was able to develop, under a small business innovation research (SBIR) program, a short pulse infrared laser system it calls Laser Bond Inspection (LBI) that generates a non-destructive compressive stress wave through the bonded composite material that doesn’t affect a strong, good bond but will show an altered signal if a “kissing” bond or weak bond is present. A prototype mobile system with an articulating arm was delivered to Boeing several years ago that performs “spot” checks at defined locations, but Lahrman says much still needs to be done, including increasing laser efficiency and developing standards and a common data base to govern the procedure and allow correlation to bond strength. Still, if LBI could be combined with manufacturing and process controls for adhesive bonding such as those developed for the TRUST project (here’s the link to our TRUST article: http://www.compositesworld.com/articles/building-trust-in-bonded-primary-structures ), we might get closer to bonded primary aerospace structure, without redundant fasteners. Here’s a link to LSP’s Web site, with more information: http://www.lsptechnologies.com/non-destructive-bond-inspection.php.
Automated machining and lamination sessions were of interest, and a paper presented by Asier Huertas of the Danobat Group (Elgoibar, Spain) stood out, for me. Danobat has been on my mind for years since I had heard of its dry fabric automated laydown machine designed for a proprietary wind blade manufacturer. With a rich history in multi-axis machine tools, including milling and grinding, boring, plasma cutting and more, and 1400 employees, nevertheless the company stayed out of the composites spotlight until this event. Huertas, the director of Danobat’s composites division, described the Automated Dry Material Placement (ADMP) precision head that has the capability of laying dry, multiaxial fabrics up to 2m in width, or more, depending on the application, equipped with 6-axis and cut on the fly capability. He showed examples of the efficiency of laying pre-kitted biaxial fabrics for a wing skin followed by out of autoclave processing, saving considerable laydown time over traditional automated prepreg tape laying. A key aspect of the Danobat technology is the head’s ability to pick and place multiaxials without causing sleaze or fiber distortion.
At the end of the day, the insight I gained, at this event geared to incorporating automation, was that it all comes down to people — bright, engaged humans make automation projects happen. During a tutorial session, I sat near two young Boeing engineers, one a woman, and two young SpaceX engineers. When the presenter asked everyone to split into teams, I was part of this group. Our task: how would you adhesively join composite panels to underlying metallic bulkheads on an aircraft structure, and do it within very tight tolerances? Well, I couldn’t answer, but it was interesting and revealing to see the interchange and the collaboration that took place among the four engineers, conducted with humor, good grace and obvious knowledge. In another session, a young Northrop Grumman engineer pointed out manufacturing success comes down to trust: yes, we may have an awesome automated laser projector showing ply or component placement, but do you trust the person who programmed that device? Good relationships and partnerships, coupled with robotics and artificial intelligence, together will drive the maturation of composites manufacturing.
Related Content
From the CW Archives: Airbus A400M cargo door
The inaugural CW From the Archives revisits Sara Black’s 2007 story on out-of-autoclave infusion used to fabricate the massive composite upper cargo door for the Airbus A400M military airlifter.
Read MoreVIDEO: One-Piece, OOA Infusion for Aerospace Composites
Tier-1 aerostructures manufacturer Spirit AeroSystems developed an out-of-autoclave (OOA), one-shot resin infusion process to reduce weight, labor and fasteners for a multi-spar aircraft torque box.
Read MoreCompPair adds swift prepreg line to HealTech Standard product family
The HealTech Standard product family from CompPair has been expanded with the addition of CS02, a swift prepreg line.
Read MorePlant tour: Albany Engineered Composites, Rochester, N.H., U.S.
Efficient, high-quality, well-controlled composites manufacturing at volume is the mantra for this 3D weaving specialist.
Read MoreRead Next
VIDEO: High-volume processing for fiberglass components
Cannon Ergos, a company specializing in high-ton presses and equipment for composites fabrication and plastics processing, displayed automotive and industrial components at CAMX 2024.
Read MorePlant tour: Daher Shap’in TechCenter and composites production plant, Saint-Aignan-de-Grandlieu, France
Co-located R&D and production advance OOA thermosets, thermoplastics, welding, recycling and digital technologies for faster processing and certification of lighter, more sustainable composites.
Read More“Structured air” TPS safeguards composite structures
Powered by an 85% air/15% pure polyimide aerogel, Blueshift’s novel material system protects structures during transient thermal events from -200°C to beyond 2400°C for rockets, battery boxes and more.
Read More