Innovative molding technology for high-performance apps
Composites are relatively new materials, and since their begining, able and motivated individuals have been diligently trying to make them better. A case in point is TEK-USA (Canal Fulton, OH, US).
Share
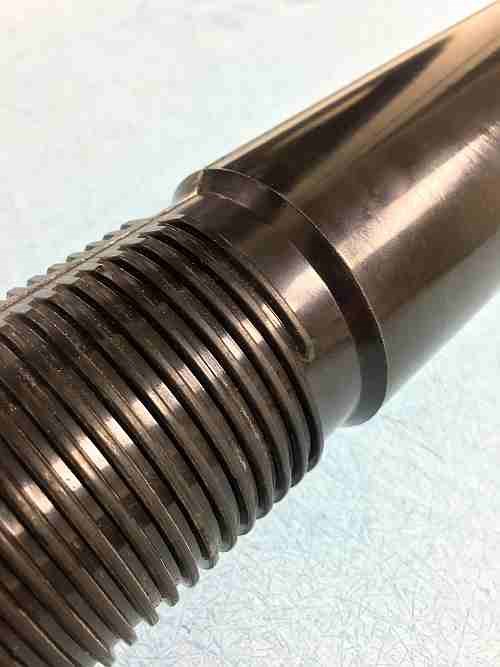
TEK-USA's compression-molded, net-shape component needs no post-cure machining.
Composites are relatively new materials, and since their begining, able and motivated individuals have been diligently trying to make them better. A case in point is TEK-USA (Canal Fulton, OH, US). I had the chance recently to talk at length with the president and CEO of the company, Chris Willison, who described how the enterprise has morphed from an Akron-area job shop making metal compression molds, tools and plastic parts into a high-tech composites fabricator supplying the oil and gas industry, as well as many more industrial clients. It’s a fascinating journey involving a lot of creativity: “We had to reinvent ourselves — mold technology was going away. Fortunately, we have retained those legacy skills, which has really helped us with our composite products,” says Willison.
The company began machining complex and detailed metal parts and molds for a few major oilfield supply company in the mid-2000s, while meanwhile developing a compression-molded composite version of a “slip” for the industry (a “slip” is a conical wedge with teeth or other gripping elements that is critical for the performance of fracking and bridge plugs used to isolate specific zones in a borehole. Slips prevent the plug from slipping further down into the hole, thanks to the gripping elements that wedge against the inner wall of the well casing; they are milled out after work on that specific zone is complete). Willison says his company was one of the first able to produce a cost- and production-efficient composite slip (in a patent-pending process), which took years to perfect and a lot of effort to sell the client on the benefits, but which is now a benchmark in the oil and gas industry, thanks to a major client. “The metallic business for oil and gas was instrumental in creating the opportunity to exploit our core expertise: composites!” says Willison.
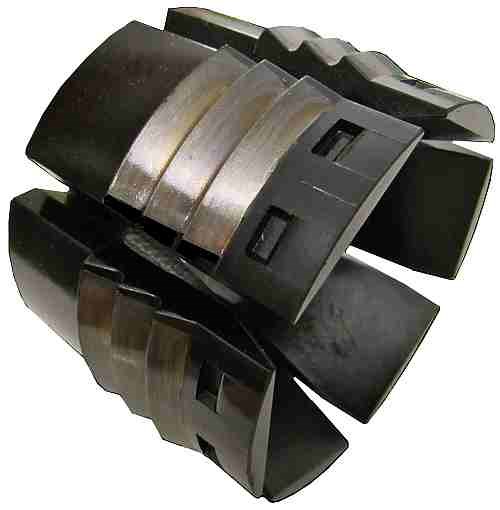
TEK-USA's compression-molded composite slip component.
The decline of natural gas prices and consolidation in the oil and gas industry over the past several years resulted in a near-disaster for the company, which lost contracts and had to create new business. “We needed some alternative, disruptive technologies,” says Willison, who believed that there were better materials for frac plug components, given his knowledge of the downhole oil and gas market (see CW’s articles about frac plugs, here: http://www.compositesworld.com/articles/a-critical-market-sector-downhole-composites-in-oil-and-gas, and here: http://www.compositesworld.com/blog/post/composites-boon-from-hydraulic-fracturing ), components that were stronger and could stand up to higher pressures and temperatures downhole. At the same time, his company’s technology could transfer to industries other than oil and gas.
Willison’s group first developed a phenolic resin system for higher temperature frac and bridge plug components, branded as PhenoliX molding compounds. With a better understanding of how to manufacture and compound PhenoliX materials, TEK-USA believed that it could do the same with a hybrid epoxy, which it branded Zepoxy, which had the potential for better performance than phenolic in specific applications; the drawback was that there was no one utilizing this type of material technology, says Willison. With proprietary additives, good material management and process controls, Zepoxy offers significant benefits, he adds: “We had spent years trying to convince customers that machining of cured composite frac bodies was a mistake, causing fiber breakage and reducing part strength and structural integrity, particularly in critical geometries such as threaded areas.”
TEK-USA’s view was that a frac plug body could be filament wound using glass fiber and the Zepoxy system, but then compression-molded while green, to literally shift fibers and resin into a final net shape that required no post-cure machining. This technology, trademarked ZCORE Filament Wound ISO-molded Composites and in the process of being patented, creates a frac plug body (or bearings, or tubular sleeves, or – the list is long) with “Precision Fiber Integration (PFI)” that adds fiber buildups in key areas, such as in threaded areas. The Zepoxy resin is a hybrid system, formulated in-house, with a Tg of 154°C and a service temperature of 220°C, giving it a heat resistance significantly above oil industry standards, says Willison. With molds and custom presses produced in-house, TEK-USA is able to de-gas the filament-wound parts for virtually zero void content, which enhances part strength (they are able to withstand 28,600 kgs of compressive force). Metallic coatings for wear can also be applied. While no details were shared, the frac plug component technology looks to be ready to transition into a number of alternative industrial applications.
“We’re cross-pollinating technology across many industries,” asserts Willison. “We’re the only company I know of that can effectively compression mold with hybrid epoxy for net shape products — we’ve got many ideas and potential products.” With an ISO 9001- and 17025-certified 5574m2 facility fully-equipped for machining, molding, testing, formulation, quality control and production, using Six-Sigma methods, the company is now serving aerospace, defense, nuclear and the energy and exploration markets. Watch for more announcements from this innovative industrial composites company. Here’s TEK-USA’s Web site for more information and contact details: http://tekusa.com/.
Related Content
Carbon fiber, bionic design achieve peak performance in race-ready production vehicle
Porsche worked with Action Composites to design and manufacture an innovative carbon fiber safety cage option to lightweight one of its series race vehicles, built in a one-shot compression molding process.
Read MoreCorebon induction heating
This sidebar to CW’s August 2024 feature article reviews this technology for more efficient composites manufacturing and why it aligns with Koridion active core molding.
Read MorePEEK vs. PEKK vs. PAEK and continuous compression molding
Suppliers of thermoplastics and carbon fiber chime in regarding PEEK vs. PEKK, and now PAEK, as well as in-situ consolidation — the supply chain for thermoplastic tape composites continues to evolve.
Read MorePlant tour: Arris Composites, Berkeley, Calif., U.S.
The creator of Additive Molding is leveraging automation and thermoplastics to provide high-volume, high-quality, sustainable composites manufacturing services.
Read MoreRead Next
Plant tour: Daher Shap’in TechCenter and composites production plant, Saint-Aignan-de-Grandlieu, France
Co-located R&D and production advance OOA thermosets, thermoplastics, welding, recycling and digital technologies for faster processing and certification of lighter, more sustainable composites.
Read MoreAll-recycled, needle-punched nonwoven CFRP slashes carbon footprint of Formula 2 seat
Dallara and Tenowo collaborate to produce a race-ready Formula 2 seat using recycled carbon fiber, reducing CO2 emissions by 97.5% compared to virgin materials.
Read MoreVIDEO: High-volume processing for fiberglass components
Cannon Ergos, a company specializing in high-ton presses and equipment for composites fabrication and plastics processing, displayed automotive and industrial components at CAMX 2024.
Read More