2016 JEC World in Paris (Day 2): Composites in transition
The JEC Europe show has evolved over the past two decades into a very large and very busy convention, with a grown-up feel.
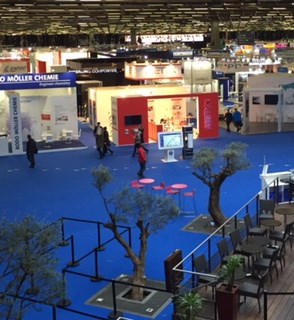
Live olive trees grow inside the 2016 JEC World venue.
It’s a long way from the CNIT La Defense, to Porte de Versailles convention center, to the Paris Nord Parc des Expositions near Charles de Gaulle airport, in both distance and scale. The JEC Europe show has evolved over the past two decades into a very large and very busy convention, with a grown-up feel. “The big trend in composites is industrialization — we’re transitioning from a cottage industry to large-scale production,” said Carmelo Lo Faro in an interview with CW. Lo Faro is executive vice president at Solvay (having spent his career at Cytec) and is responsible for strategy and business development for Solvay’s Composites Materials business. He added “There’s a clear and compelling need being expressed by our customers for lightweight solutions, everywhere in the world.” That light-weighting push has spurred development in materials and process, evident at every stand, for aerospace, industrial apps, and particularly, in automotive. Car parts, cars, and even city buses were parked on the show floor to demonstrate new mobility applications.
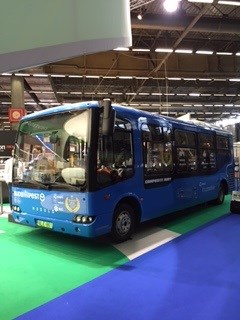
The winner of a JEC Innovation award in the category of urban transportation: an all-composite bus body in use in Budapest, Hungary
Amid the usual intensive meetings, huddles and visitor traffic, several announcements stood out. Continental Structural Plastics (CSP, Auburn Hills, MI, US) and Mitsubishi Rayon Co. Ltd. (MRC, Tokyo, Japan) say they have established a memorandum of understanding regarding the development and manufacturing of innovative carbon fiber structural components for the automotive industry in North America. Under the MOU, CSP and MRC have agreed to commence detailed studies to investigate compression molded components made from carbon fiber reinforced plastic materials, which could include carbon fiber sheet molded compound (SMC) and prepreg carbon fiber compression molding (PCM). These components will include Class A body panels, as well as non-class A structural automotive applications.
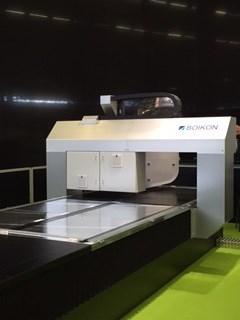
Boikon's automated thermoplastic layup machine with continuous ultrasonic tacking capability.
The growth of thermoplastics is evident, from all-thermoplastic, bonded primary wing structure for aerospace, to sophisticated processing for thermoplastic parts that replace thermoset designs. As one process supplier told me, “Thermoplastic is the only way to go.” And for both TPs and thermosets, automation is exploding. The Stellar Project, a consortium led by UK’s NetComposites (Chesterfield, UK) that includes Fraunhofer IPT and others, is aimed at developing rapid, automated thermoplastic tape layup. NetComposites showed the fruits of the group’s progress with prototype parts and a demonstration of the tape laying concept. On display in the Demo area was an automated machine by Boikon (Leek, The Netherlands) that the company says is the world’s first automated layup system based on continuous ultrasonic tacking technology. The “Falko” head lays unidirectional thermoplastic tapes that are tacked to one another in a safe and consistent process that allows near-net shape laminates to be easily handled prior to consolidation.
Pinette Emidecau Industries (Chalon Sur Saone, France) announced the successful completion of a complete turnkey plant in Vietnam for a Canadian customer that includes nearly 100 machines (metal milling, forming presses, and more, for the entire product process) to make industrial tires and rollers with little operator input. And Mikrosam (Prilep, Macedonia) revealed it is working on its most sophisticated filament winding line yet, an almost fully-automated production facility capable of making any type of compressed natural gas (CNG) tank at high rate with very little human interaction.
And materials of all types, optimized with fast serial production in mind, are on display. As one example, 3B Binani (Battice, Belgium) offered a new pelletized and agglomerated chopped glass product for polyamides that eliminates “fuzz and fly” and reportedly enables faster processing with better part quality.
There will be a lot more to follow from CW about the show. As Lo Faro summed up, “I feel extremely lucky to be working in this industry. We’re entering a phase of tremendous growth and innovation."
Related Content
Co-molding SMC with braided glass fiber demonstrates truck bed potential
Prepreg co-molding compound by IDI Composites International and A&P Technology enables new geometries and levels of strength and resiliency for automotive, mobility.
Read MoreDieffenbacher acquires Schmidt & Heinzmann composites business
The acquisition, which includes all intangible assets of the business unit, will expand Dieffenbacher’s SMC delivery spectrum, enable potential for portfolio growth and synergies.
Read MoreComposite materials, design enable challenging Corvette exterior components
General Motors and partners Premix-Hadlock and Albar cite creative engineering and a move toward pigmented sheet molding compound (SMC) to produce cosmetic components that met strict thermal requirements.
Read MoreComprehensive service formulates standard, custom SMCs
CAMX 2024: As an SMC product manufacturer, Molding Products LLC provides SMC formulations and technical support for diverse markets, from R&D to post-production.
Read MoreRead Next
VIDEO: High-rate composites production for aerospace
Westlake Epoxy’s process on display at CAMX 2024 reduces cycle time from hours to just 15 minutes.
Read MorePlant tour: A&P, Cincinnati, OH
A&P has made a name for itself as a braider, but the depth and breadth of its technical aptitude comes into sharp focus with a peek behind usually closed doors.
Read MoreModeling and characterization of crushable composite structures
How the predictive tool “CZone” is applied to simulate the axial crushing response of composites, providing valuable insights into their use for motorsport applications.
Read More