Offshore oil composites: Designing in cost savings
In offshore oil structures, composites offer the potential to save weight, reduce maintenance, enhance safety, limit adverse environmental impact and improve durability.
In offshore oil structures, composites offer the potential to save weight, reduce maintenance, enhance safety, limit adverse environmental impact and improve durability. Advancements in materials (e.g., fire-resistant phenolic resin) and in design and fabrication methods have addressed safety issues and improved performance and reliability. Safety-critical components constructed of fiberglass and polymeric resin now are routinely specified for offshore platforms. These include firewater piping and secondary structures, such as gratings, handrails and stairs. More structurally demanding applications, such as composite high-pressure riser tensioner accumulator vessels and carbon fiber rod-reinforced umbilicals (see photo, at right), have been successfully introduced offshore. Synthetic fiber mooring lines are used extensively for station keeping of deepwater platforms. Onshore, spoolable composite pipe is a rapidly growing application for oil and gas transport. In fact, a very wide range of applications is under investigation or in development.
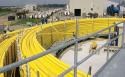
Spoolable pipe: These carbon fiber rod-reinforced deepsea umbilicals, introduced by Aker Solutions (Lysaker, Norway), now service subsea offshore oil installations 1.5 miles below the water’s surface in the Gulf of Mexico.
Photo Credit: Spoolable Pipe
Although the past decade witnessed reasonable growth in offshore composites, large-scale projects continue to be hindered by perceived technical, emotional and business barriers. Many factors contribute to successful introductions of composites in this market, including clear advantages over existing technology, superior material properties (e.g., light weight and fatigue resistance), advanced design capability, safety and, ultimately, cost.
Further deployment of composites in critical applications will depend on how well the offshore oil industry and regulatory agencies understand the characteristic limitations of candidate material systems and structural concepts. For example, failure modes are different for metals and composites: Compression failure modes for composites include delamination and shear crippling that involves microbuckling of the fibers. Additionally, the properties of both the matrix and the fiber can affect failure modes and strength. Successful offshore composites introductions have come and will continue to come about through basic research, intensive testing and critical laboratory and field demonstrations — all done in very close interaction with regulators.
Composites also offer the opportunity to locally tailor structural strength and stiffness. Efficient minimum-weight and minimum-cost design depends on capturing this flexibility. It also depends on careful selection of the composite materials because there is significant variation in the cost of raw components (resins and fibers) as well as the processes that could be used to fabricate the structure with the selected materials. Because designers must balance performance requirements with the need to minimize cost, many offshore structures reflect a bias toward all-glass or hybrid constructions in which glass fibers are used in combination with carbon or aramid. But a move from glass to less dense, stiffer carbon fiber is likely if suppliers deliver on the promise of low-cost carbon fiber.
Another advantage of composites is that it is now possible to test monitor their structural performance in service. Fiber optics or electrical conductors can be integrated into the composite structure, providing a protected, nonintrusive means to transport structural monitoring information from remote or downhole locations — an important emerging technology in the oil industry for proving reliability.
When designers evaluate composites vs. metals for offshore applications, they must be aware that the underlying issue is whether the composite application will be cost-effective. Four criteria should be considered:
- Is the job currently performed satisfactorily with lower cost carbon steel? If so, it will be difficult to be cost-competitive with composites.
- Is corrosion a significant problem? If so, composites will probably be the better choice.
- Does saving weight provide value? Composites usually provide weight savings, relative to steel, of 50 to 75 percent.
- Will composites provide enabling capability or yield a system solution that is less expensive than a metal design? A decision to use composites in most offshore applications ultimately hinges on cost savings. These cost savings can be greatly magnified if designers consider composites in the initial design phase rather than as a retrofit, so that composite benefits cascade throughout the entire project.
Schedule-driven offshore projects have little tolerance for failure. For that reason, every effort must be made to consider in the design all the potential load scenarios and exposure environments. Readiness extends beyond the produced composite product and must include demonstrated installation procedures and due consideration of potential service irregularities. Also, it is important to conduct and carefully scrutinize the results of laboratory and field tests to provide a definitive understanding of failure modes and to guide design refinements, where necessary.
Finally, there is a great need for industry champions who will take up the cause of composites in offshore applications and for manufacturers who are willing to accept the challenge of making advanced composite components for new applications in accordance with established guidance.
Dr. Williams wishes to thank several individuals (who represent the following Houston, Texas-based organizations) for their suggestions in the preparation of this column: Bill W. Cole of the University of Houston’s Composites Engineering and Applications Center (CEAC), Mamdouh M. Salama of ConocoPhillips, King Him Lo of Shell, William Stringfellow of Glastek Tubular Services and Mike Feechan of Fiberspar Corporation.
Jerry G. Williams, Ph.D., P.E., is a consultant in the oil and gas industry (Petroleum Composites, The Woodlands, Texas). After earning BS and MS degrees at Oklahoma State University, Williams began working at the NASA Langley Research Center (Hampton, Va.) where his primary focus was R&D on composite materials for aircraft primary structures. While there, he earned a Ph.D at Virginia Polytechnic Institute and State University. He joined ConocoPhillips (Houston, Texas) in 1985 to explore opportunities to use composite materials in the petroleum industry. He was a founder of and served with the Composites Engineering and Applications Center at the University of Houston, and he is listed as an inventor on over 30 patents, including several related to spoolable composite pipe and the structural monitoring of composite structures and mooring ropes, using optical fibers.
Related Content
Thermoset-thermoplastic joining, natural fibers enable sustainability-focused brake cover
Award-winning motorcycle brake disc cover showcases potential for KTM Technologies’ Conexus joining technology and flax fiber composites.
Read MoreComposites end markets: Electronics (2024)
Increasingly, prototype and production-ready smart devices featuring thermoplastic composite cases and other components provide lightweight, optimized sustainable alternatives to metal.
Read MoreMicrowave heating for more sustainable carbon fiber
Skeptics say it won’t work — Osaka-based Microwave Chemical Co. says it already has — and continues to advance its simulation-based technology to slash energy use and emissions in manufacturing.
Read MoreASCEND program update: Designing next-gen, high-rate auto and aerospace composites
GKN Aerospace, McLaren Automotive and U.K.-based partners share goals and progress aiming at high-rate, Industry 4.0-enabled, sustainable materials and processes.
Read MoreRead Next
Composites Alive And Well In Offshore Oil Applications
The petroleum industry is moving forward with many interesting projects that will increase composite demand.
Read MoreOffshore Applications: The Future Is Now
The number of composites installations continues to grow on new and existing offshore facilities.
Read More