Polybenzoxazine on the horizon?
Benzoxazine veteran Dr. Hatsuro Ishida at Case Western Reserve University has developed what he calls the fourth generation of this versatile high-heat, high-strength matrix resin.
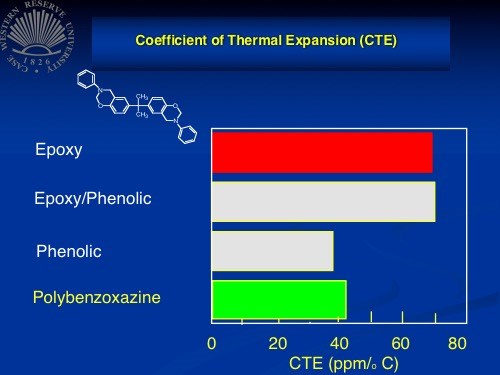
CTE of polybenzoxazine compared to epoxy, epoxy/phenolic and phenolic. These data, provided by
Dr. Hatsuro Ishida at Case Western Reserve University, come from the US Federal Aviation Administration (FAA).
Dr. Hatsuro Ishida, professor at Case Western Reserve Univeristy (Cleveland, OH, US), has been at the forefront of benzoxazine research and development and formulation since the polymer was adopted by the composites industry in the early 1990s. He has continued this work and reported, at the SPE Thermoset Topcon (April 19-20), on his latest development.
Ishida says the latest benzoxazine resins to come out of his lab represent the fourth generation of this versatile matrix resin and signals a step-change in physical and mechanical properties. Polybenzoxazine is formulated by the synthesis of a benzoxazine monomer that is synthesized from phenol, formaldehyde and a primary amine.
The list of properties available with polybenzoxazine, says Ishida, are considerable:
- <1% volumetric change or expansion
- Fast Tg development with low conversion
- Low crosslink density with very high modulus
- Up to 84% char yield at 800°C
- <2% water absorption at saturation
- 13 mJ/m2 surface free energy (less than Teflon)
- Extremely high molecular design flexibility
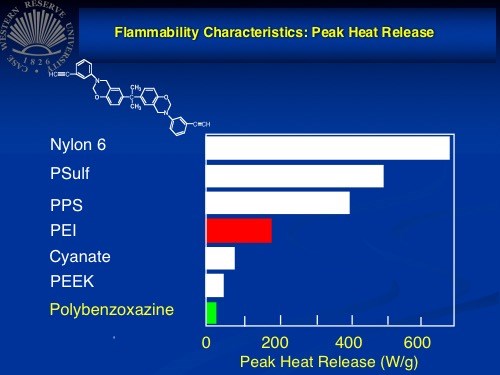
Polybenzoxazine's flammability characteristics appear to make it a strong
candidate for aerocomposites applications.
In testing, Ishida reports, polybenzoxazine showed mechanical properties and shrinkage better than epoxy, fire performance second only to phenolic, use temperature comparable to or better than BMI, and cost on par with epoxy. It also features a dielectric constant better than epoxy, a CTE of 41 ppm/°C, a peak heat release in flammability tests of <50 W/g, and a flex strength much higher than the corresponding epoxy or phenolic composites.
Benzoxazines currently on the market in the composites industry are supplied by Henkel Corp. (Rocky Hill, CT, US), Huntsman Advanced Materials (The Woodlands, TX, US), and Shikoku Chemicals (Kagawa, Japan). The resin’s high-temperature and flammability performance, high strength, thermal stability and nearly unrestricted outtime, have made it attractive in applications — particularly in aerospace — where BMI traditionally has been favored.
Ishida says that neither he nor Case Western Reserve University are equipped to commercialize his formulations, but he is very open about his lab’s benzoxazines chemistries and encourages resin suppliers to adopt them. Ishida can be reached at hxi3@case.edu.
Related Content
-
Plant tour: Daher Shap’in TechCenter and composites production plant, Saint-Aignan-de-Grandlieu, France
Co-located R&D and production advance OOA thermosets, thermoplastics, welding, recycling and digital technologies for faster processing and certification of lighter, more sustainable composites.
-
“Structured air” TPS safeguards composite structures
Powered by an 85% air/15% pure polyimide aerogel, Blueshift’s novel material system protects structures during transient thermal events from -200°C to beyond 2400°C for rockets, battery boxes and more.
-
Monadnock HTAC Veil protects GFRP equipment against corrosion
Binder-free ECTFE-apertured reinforcement maintains a high resistance against chemicals and abrasion at high temperatures, extending performance and integrity of composite systems.