
Clockwise from top left, induction welded thermoplastic composite skin stringer demonstrator, infrared monitoring of induction welding stringers onto panel, continuous compression molding (CCM) of thermoplastic composite stringer, chopped carbon fiber tow for materials testing and (bottom left), computer simulation of induction welding process. SOURCE for all images | CETMA.
Established in 1994, Centro di Ricerche Europeo di Technologie, Design e Materiali (CETMA, Brindisi, Italy) is one of the largest independent research and technology organizations in Italy, with a 4,000-square meter facility and 75 employees. For more than 20 years, CETMA has invested strongly in composites, resulting in a wide range of expertise:
- Component design and prototyping
- New composite processes
- Recycling processes for composites and plastics
- Process optimization for cost, sustainability, rate, etc.
- Real-time process monitoring
- Nondestructive testing (NDT)
- Structural health monitoring (SHM) real-time and remotely during production and service
- REACH consulting
- Thermoplastic stamping, continuous compression molding (CCM) and prepreg compression molding (PCM)
- Liquid infusion, resin transfer molding (RTM) and same qualified RTM (SQRTM)
- Out of autoclave (OOA) prepreg
- Induction welding
CETMA’s main goal is to support companies and innovation. Served by four main labs, CETMA’s composites activities are organized within its Advanced Materials and Processes (AMP) department which also comprises four areas:
- Materials and Characterization
- Technologies and Processes
- Modeling and Simulation
- Diagnostics and Structural Health Monitoring
AMP employs 30 staff including material, aeronautical, civil and chemical engineers as well as a chemist, material scientist, architect and multiple technicians — conforming to its belief in multidisciplinary teams.
Strength in thermoplastic composites
“We offer a full spectrum of services in composites,” notes Alessandra Passaro, head of the AMP department at CETMA, “but our activities in thermoplastic materials is one of our priority areas, currently. All of the different kinds of thermoplastic matrix polymers have been processed in our lab. We started working with TWINTEX commingled fiber in 2004 and with compression molding using a simple press roughly 15 years ago. Now, we have developed patented continuous compression molding (CCM) and induction welding technologies. We have analyzed all of the thermoplastic composite materials that can be used in these processes.”

Carbon fiber composite parts made using CETMA’s continuous compression molding (CCM) line.
The CCM line can manufacture constant section parts using PPS, PEEK, PEKK or PAEK. But how is the CETMA process different than what is being used by companies like XELIS (Markdorf, Germany) and ATC Manufacturing (Post Falls, Idaho, U.S.)? (See CW articles: “Aerospace-grade compression molding” and “Accelerating thermoplastic composites in aerospace”.) Passaro explains, “There are some specific details in the design of the mold we use. Our technology is more flexible regarding geometries and matrix materials that can be used. It is still in development.” Though patented, the technology is still being developed and some aspects are proprietary. The reason why CETMA has pursued CCM is not. “We saw the increased use and need for continuous thermoplastic composite processes,” says Passaro. “XELIS is a products company, not a machine supplier. We are an independent R&D organization and so invest in and develop the technology from a different viewpoint.”
One example of this is the extensive process simulation to analyze the temperature distribution in the mold. “The simulation results let us have a complete picture of the temperature evolution in the material over time,” she explains, “which is very difficult to monitor inline from one side, and yet it is crucial for minimizing defects in the composite.”

CETMA used CCM to produce the stringers and plates from carbon fiber/PEKK unidirectional tapes and then joined them using induction welding for this keel beam demonstrator in the Clean Sky 2 KEELBEMAN project.
Induction welding for assembly
Another key part of CETMA’s thermoplastic composites expertise is patented induction welding technology, which includes a control system and cooling to maintain heat within the weldline. CETMA used the technology with partner EURECAT (Barcelona, Spain) to assemble CCM profiles and plates into a thermoplastic composite keel beam for an Airbus A320 type aircraft in the Clean Sky 2 KEELBEMAN project. My Jan 2020 blog, “Advancing thermoplastic composites and RTM for Clean Sky 2 …”, gives more detail on this project as well as the details of CETMA’s welding.
CETMA robotic induction welding system (top) building a thermoplastic composite door for the Clean Sky 2 project TOD and demonstration work (bottom) completed in the Clean Sky project Eco-Fairs (2010-2013) showing that welded woven carbon fiber/PPS stringers buckled before any separation from the skin.
“We have developed two types of induction welding systems,” notes Passaro.“One is a fixed machine for flat surfaces and one that is robot-based for complex, 3D geometries. Both enable continuous welds on an industrial scale without requiring additional materials in the weldline yet deliver very high adhesion performance in assemblies.”
CETMA has demonstrated induction welding on composite laminates made using carbon fiber woven fabric and unidirectional (UD) tape as well as a range of matrix materials: PPS, PEEK, PEI, PEKK, PP, PA6, PA12 and a hybrid thermoset epoxy/PVB (polyvinyl butyral) thermoplastic system.
It has also applied its expertise in computer modeling and simulation to the induction welding process. “This allows us to predict the temperature evolution in the join area during welding, providing a fundamental help in optimizing the process parameters,” says Passaro.

CETMA has developed 3D finite element models for induction welding that couple electromagnetic and heat transfer equations with matrix melting and crystallization, showing good agreement with experimental temperature measurements. SOURCE | “Finite element modeling of continuous induction welding of thermoplastic matrix composites” by Francesca Lionetto and Alfonso Maffezzoli (University of Salento, Lecce, Italy) and Silvio Pappadà and Giuseppe Buccoliero (CETMA).
Clean Sky 2 and composites R&D projects
In addition to KEELBEMAN, CETMA’s AMP Department is currently involved in four other Clean Sky 2 projects.
TRINITI - Multi-material thermoplastic high-pressure nitrogen tanks for aircraft (JTI-CS2-CFP09-2018-02). The two-year project, which began in 2019, aims to build a prototype aircraft tank for long-term storage of nitrogen for firefighting purposes. Diehl Aviation (Gilching and Dresden, Germany), is the topic manager for the project. Partners also include aerospace R&D lab Novotech s.r.l. (Naples, Italy), Composites Testing Laboratory (Inverin, Co. Galway, Ireland). The project will manufacture multi-material thermoplastic composite tanks through a combination of processes such as co-extrusion to form a multi-layer and multifunctional liner/laminate, followed by in-situ consolidation (ISC) using laser-assisted automated fiber placement (AFP). (For more about ISC AFP, see “Consolidating thermoplastic composite aerostructures in place, Part 1 and Part 2”.) One goal within TRINITI is to reduce or even eliminate micro-cracking in cryogenic environments. Currently CETMA is working to identify all thermoplastic materials that can satisfy the requirements of the aerospace pressure vessels.
SPARE – Full scale innovative composite pax and cargo floor grids for regional Aircraft Fuselage barrel on-ground demonstrators – (JTI-CS2-2017-CfP07-REG-01-14). Started in Oct 2018, this 18-month project aims to manufacture full-scale passenger and cargo floor grids made using carbon fiber-reinforced thermoplastic (TP) composites. The highly automated production comprises progressive roll forming and induction welding for assembly. The objective is to reduce weight and recurring costs compared to traditional metal and thermoset composite solutions. The composite floor grids will be assembled into the Clean Sky 2 regional aircraft fuselage demonstrators for on-ground testing and will be evaluated for technical and economic impact as well as flame resistance performance per FAR 25.583 regulations. Topic leader is Leonardo while CETMA coordinates the project in collaboration with machine manufacturer OMI S.r.l. (Fogliano Redipuglia, Italy).


One of CETMA’s main contributions to SPARE is the development of infrared thermography (IRT) for inline monitoring of the progressive roll forming. This process subjects rolls of TP composite laminate to compaction and heating until the material process temperature, complex shape and design thickness is reached. “However, it is important to make sure that the innermost plies experience complete melting of the matrix and consolidation,” explains Passaro. “Moreover, there is a narrow temperature window which ensures melt but does not degrade the polymer. IRT is a non-contact method that measures radiated heat energy across the part surface with high accuracy.”
CETMA used windows made of zinc selenurium (ZnSe) to look inside the closed equipment. Transparent to IR waves, they perform at temperatures up to 500°C. Two such windows were constructed in the SPARE project progressive roll-forming line with IRT cameras suspended above to have a nearly perpendicular view of the processed material. Editable control software made it possible to monitor, record and alarm if values fell outside the defined target range.
Layout of the IRT cameras in the SPARE progressive roll-forming line (top). From these cameras, Fig. 19 shows the surface temperature distribution during production (bottom left) and Fig. 20 shows a 3D analysis of that data (bottom right).
Uniformity of the material temperature through the profile cross-section was evaluated at the two limit points — line 1 is close to the heating step and line 2 is further along the forming process. Each was divided into 3 successive steps (Fig. 19): initial phase (step 1), forming process started (step 2) and forming with reduced speed (step 3). IRT showed that temperature at the outer edges of the laminate was lower than in the central area, leading to uneven heating and mechanical properties. A 3D representation of the IRT-recorded surface temperatures (Fig. 20) provided a visual aid to better understand the temperature distribution.
TOD – Thermoplastic on Doors (JTI-CS2-2017-CfP07-REG-01-12). TOD aims to develop and validate rapid production and assembly of a full-scale thermoplastic composite door (including fuselage substructures) for a regional aircraft. TOD is part of the Clean Sky 2 Regional Aircraft IADP (Innovative Aircraft Demonstrator Platform), which takes the integration of technologies developed in the Clean Sky phase one Green Regional Aircraft ITD (Innovative Technology Demonstrator) to a higher level of complexity and maturity via two flying test-beds and three large integrated ground demonstrators. Led by Leonardo, CETMA will work with project partners The Welding Institute (TWI, Cambridge, U.K.) and aerospace Tier 1 and engineering/industrialization firm DEMA (Design Manufacturing SpA, Somma Vesuviana, Italy).
The proposed approach includes optimization and validation of thermoforming for component fabrication and joining processes such as induction welding (IW) and resistive implant welding (RIW), which enable weight reduction by eliminating mechanical fasteners. TOD will also advance industry 4.0 automation and inline monitoring to support high-rate production of high-quality parts (zero defects) with robust process control. Expected benefits include:
- Minimum 15% weight reduction
- Reduction of waste and scrap by 10% through sensors and inline monitoring
- Up to 75% energy savings versus standard autoclave processing
- Reduced recurring costs via adaptive smart manufacturing (increased flexibility, decreased full line tools cost)
- Improved CO2 emissions during manufacturing and lighter-weight aircraft operation.
CETMA is involved in numerous other development projects. One example is NHYTE (New Hybrid Thermoplastic Composite Aerostructures manufactured by Out of Autoclave Continuous Automated Technologies) which aims to demonstrate innovative integrated aerostructures made from hybrid thermoplastic matrix materials with multifunctional capabilities.
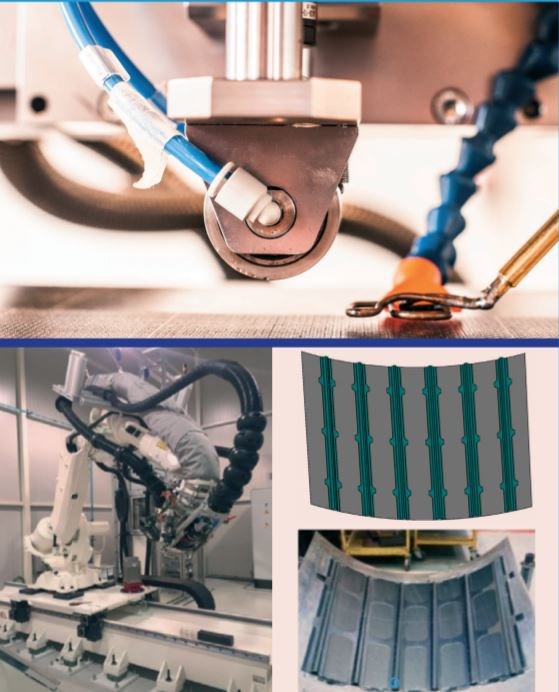
SOURCE | NHYTE Poster
Funded under the Horizon 2020 program and led by NOVOTECH (Naples, Italy),NHYTE began in Sep 2018 and was scheduled to end in Jan 2020. The high-performance hybrid material is based on a commercial carbon fiber/PEEK prepreg with added amorphous PEI films to enable in-situ consolidation with automated fiber placement (ISC AFP) and then assembly via CETMA’s patented induction welding technology. CETMA has completed a broad characterization campaign comprising physical-mechanical and virtual testing of the hybrid composite material and induction welding process setup.
Recycling carbon fiber
Another key area for CETMA is recycling. The CIRCE project aims to use prepreg scraps generated during composite parts manufacturing by recycling it into a compression molding compound, which will then be used to mold toe inserts for safety shoes. CETMA will characterize this secondary raw material and develop a numerical model to predict the structural performance of the shoe inserts. This model will help analyze and verify impact behavior to meet safety regulations, with results used to refine and finalize the toe inserts design. The Italian project team includes Base Protection (Barletta), composite motorsports/automotive parts manufacturer HP Composites (Ascoli Piceno), machine and production line specialist Elks Group (Ascoli Piceno) and Petroceramics (Stezzano).
The REVALUE project aimed to combine pyrolysis-recycled carbon fiber with thermoplastics to replace current materials in a range of automotive applications.
Perhaps CETMA’s largest investment in recycling to date has been via the REVALUE project aimed at REcycled carbon fibers for high VALUE composites. Funded by the European Institute of Innovation & Technology (EIT, Budapest, Hungary), the goal of the REVALUE project is to take recycled carbon fiber (RCF) provided by leading producer ELG Carbon Fibre (Coseley, U.K.) using pyrolysis and combine it with virgin and recycled thermoplastic polymers to replace current materials used by Centro Ricerche Fiat (CRF, Turin, Italy) for the production of selected automotive components.
Unsized recycled carbon fiber (RCF) is prone to fiber breakage and separating into filaments, appearing as “fluffy” (top left) compared to virgin CF (top right). CETMA developed a pilot plant for applying sizing to RCF to improve processability and increase interface strength with selected thermoplastic matrices.
However, as noted in the Jan-Feb 2020 JEC Composites magazine article, “New sizing formulation for recycled carbon fibres” by Alessandra Passaro, et. al., RCF produced by pyrolysis has no sizing, making the brittle fibers prone to frequent breaking during handling as well as separation of the fiber tows into filaments, resulting in an entangled, “fluffy” form with low bulk density. As part of REVALUE, CETMA developed a specific formulation of sizing for RCF, compatible with virgin or recycled polypropylene (PP) and PA6. It then evaluated the sizing ability to improve RCF processability and increase interface with the selected thermoplastic matrices.
To do this, CETMA developed a pilot plant for sizing RCF, able to apply the sizing in kilogram quantities and, at the same time, evaluate the effect of the main parameters on the deposition process. The plant comprises three main stations: treatment of sizing and washing of the fibers; handling the dry fibers before and after treatment; and oven-drying the fibers. Four kilograms of RCF can be treated per day in a continuous cycle.
The sized RCF from CETMA were then used by the French research center CEA and French compounder SUEZ to produce a molding compound using virgin and recycled thermoplastic polymers. Physical-chemical characterization of the compounds was completed, and the ability of the CETMA sizing to improve final composite mechanical performance was verified.
Physical testing on specimens made with CETMA-sized RCF showed improvement in both tensile and flexural composite properties.
The innovative RCF molding compounds were then used to injection mold automotive semi-structural components that are currently made with glass fiber-reinforced PP or PA6. Beyond the obvious advantage in recycling and reuse of materials, reduction of vehicle weight, fuel consumption and CO2 emissions were also demonstrated.
Outside of REVALUE, CETMA has also further developed and evaluated sizing for RCF in multiple composites processes including compression molding, vacuum infusion and RTM, showing improved properties in all cases.
CETMA has worked with a range of fiber optic, Fiber Bragg Grating (FBG), piezoelectric and strain sensors for in-situ monitoring during processing, testing and service, including micro-optical connections (top right) for lifetime monitoring with minimal impact on geometry.
Structural health monitoring (SHM)
This final key area of composites activity for CETMA is also a growing emphasis in the industry. “We have many years of experience with applying SHM for construction and building applications,” notes Passaro. “And we have also done a lot of work with SHM in composites. We know this will be important for future applications and we are interested to continue working with composites manufacturers and the industry to push this technology forward.”
Related Content
Bio-based acrylonitrile for carbon fiber manufacture
The quest for a sustainable source of acrylonitrile for carbon fiber manufacture has made the leap from the lab to the market.
Read MoreJEC World 2023 highlights: Recyclable resins, renewable energy solutions, award-winning automotive
CW technical editor Hannah Mason recaps some of the technology on display at JEC World, including natural, bio-based or recyclable materials solutions, innovative automotive and renewable energy components and more.
Read MorePlant tour: Arris Composites, Berkeley, Calif., U.S.
The creator of Additive Molding is leveraging automation and thermoplastics to provide high-volume, high-quality, sustainable composites manufacturing services.
Read MoreMicrowave heating for more sustainable carbon fiber
Skeptics say it won’t work — Osaka-based Microwave Chemical Co. says it already has — and continues to advance its simulation-based technology to slash energy use and emissions in manufacturing.
Read MoreRead Next
Advancing thermoplastic composites and RTM for Clean Sky 2 in Spain
EURECAT leads projects for TPC keel beam, window frames and thermoset RTM fuselage frames with TPC shear ties for next-gen aircraft.
Read MorePlant tour: Daher Shap’in TechCenter and composites production plant, Saint-Aignan-de-Grandlieu, France
Co-located R&D and production advance OOA thermosets, thermoplastics, welding, recycling and digital technologies for faster processing and certification of lighter, more sustainable composites.
Read MoreVIDEO: High-volume processing for fiberglass components
Cannon Ergos, a company specializing in high-ton presses and equipment for composites fabrication and plastics processing, displayed automotive and industrial components at CAMX 2024.
Read More